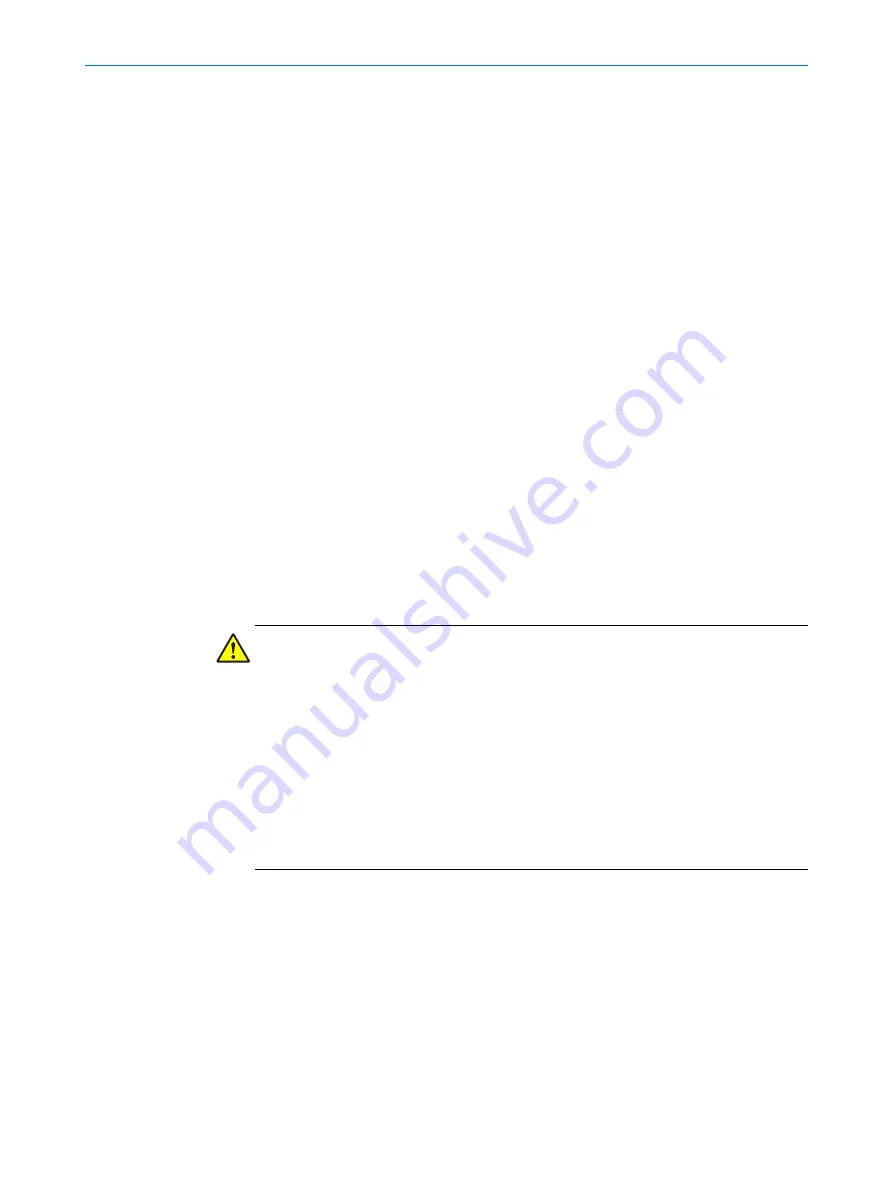
•
ISO 10218 – Robots and robotic devices – Safety requirements for industrial
robots – Part 1: Robots
•
ISO 13849-1 Safety of machinery – Safety-related parts of control systems – Part
1: General principles for design
•
ISO 13849-2 Safety of machinery - Safety-related parts of control systems - Part 2:
Validation
•
ISO 13857 Safety of machinery - Safety distances to prevent hazard zones being
reached by upper and lower limbs
•
ISO 13855 Safety of machinery - Positioning of protective devices with respect to
the approach speeds of parts of the human body
4.1.3
Quantification of components
For quantification of the safety functions, the manufacturer’s safety-relevant data of the
components used was taken into account. Where this data was not available, the typi‐
cal component values in accordance with ISO 13849-1 were used.
The values for the normal operating cycle must be adapted by the machine manufac‐
turer.
In safety function SF01.1 - Preventing an unintentional restart (manual reset), the nor‐
mal operating cycle is estimated with a value of 8,760 cycles/year and the B10d value
is a typical component value of 100,000 cycles.
If this is not adapted to the values of the components used, the pushbuttons must be
replaced after 11 years.
Corresponding changes must be made for this safety system for the emergency stop
pushbutton, the reset pushbutton and the relay.
4.2
Operating entity of the machine
DANGER
Hazard due to lack of effectiveness of the protective device
The dangerous state of the machine may not be stopped or not be stopped in a timely
manner in the event of non-compliance with the following instructions.
b
Changes to the electrical integration of the safety system in the machine control
and changes to the mechanical mounting of the safety system necessitate a new
risk assessment. The results of this risk assessment may require the entity operat‐
ing the machine to meet the obligations of a manufacturer.
b
Changes to the safety system’s configuration may impair the protective function.
The effectiveness of the safety system must be checked after any change to the
configuration. The person carrying out the change is also responsible for maintain‐
ing the protective function of the safety system.
4.3
Performance level
The calculation of the performance level can be carried out using the SISTEMA file. The
file is available on the Internet for this safety system. The manufacturer of the machine
must decide which measures should be taken against failures with the same cause.
These measures must be selected in the SISTEMA project file for each user-defined
sub-system. In addition, the correct values for the value must be chosen for the compo‐
nents that are not part of the scope of delivery,
see "General requirements", page 38
PROJECT PLANNING
4
8023421/12KF/2019-01-22 | SICK
O P E R A T I N G I N S T R U C T I O N S | sBot Stop
25
Subject to change without notice