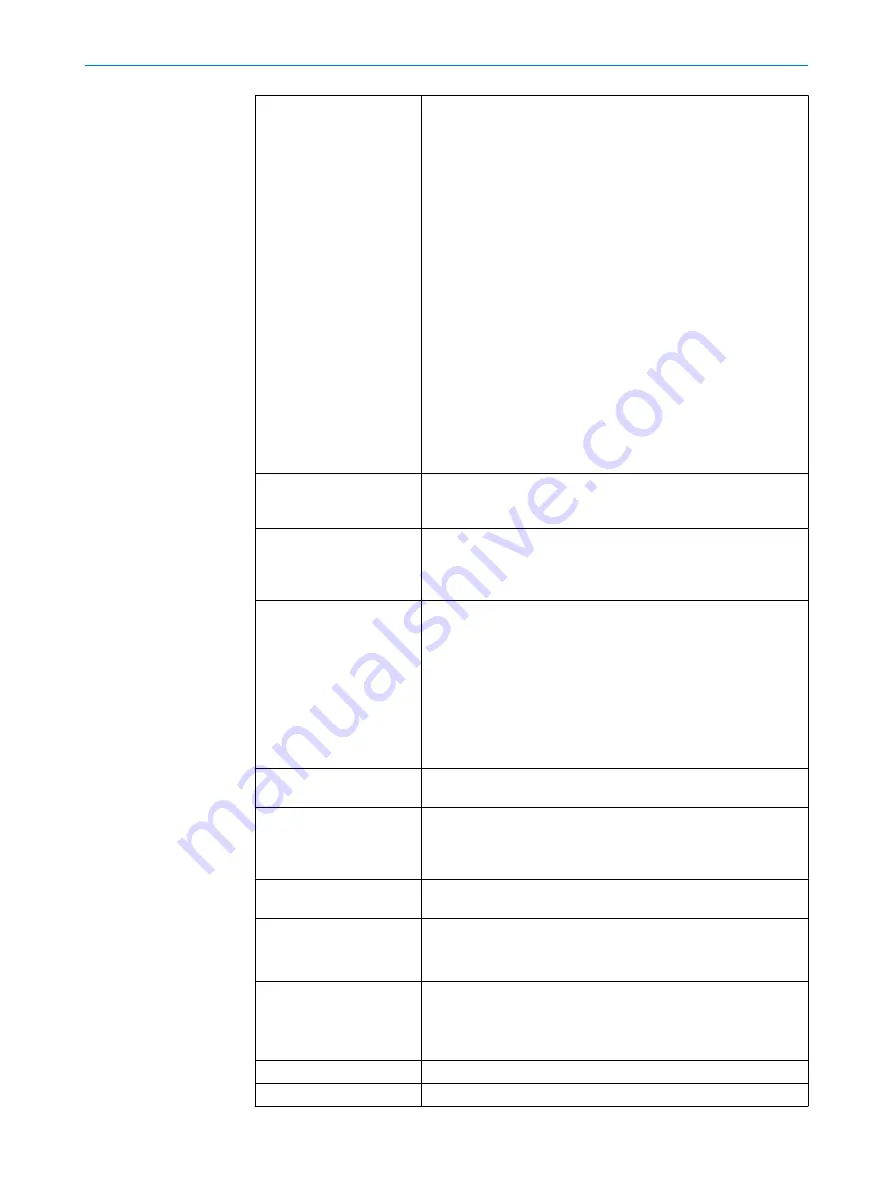
Reset
When a protective device has sent a stop command, the stopped
state must be maintained until a reset device is activated and the
machine can be restarted in a second step.
The reset brings the protective device back to the monitoring state
after it has sent a stop command. The reset also quits the start-up
or restart interlock of a protective device, so that the machine can
be restarted in a second step.
The reset must only be possible, when all safety functions and
protective devices are functional.
The reset of the protective device must not introduce any move‐
ment or dangerous situations itself. The machine is only permitted
to start after the reset once a separate start command has been
sent.
•
Manual resets are performed using a separate, manually oper‐
ated device, such as a reset pushbutton.
•
Automatic resets by the protective device are only permitted in
special cases, if one of the following conditions is met:
°
It must not be possible for people to be in the hazardous
area without triggering the protective device.
°
It must be ensured that no people are in the hazardous
area during or after the reset.
Resolution
The resolution of an active opto-electronic protective device (also
known as the sensor detection capability) is the minimum size of
an object for it to be reliably detected.
Response time
The protective device’s response time is the maximum time
between the occurrence of the event leading to the sensor’s
response and supply of the switch-off signal to the protective devi‐
ce’s interface (for example OFF state of the OSSD pair).
Restart interlock
The restart interlock prevents the machine from automatically
starting up, for example after a protective device has responded
while the machine is operating or after changing the machine’s
operating mode.
The restart interlock can be implemented in the protective device
or in the safety controller.
A command to reset the protective device must be given, for
example using a reset pushbutton, before the machine can be
restarted.
Retroreflector
A retroreflector reflects light back toward the light source largely
independently of the alignment of the retroreflector.
RSSI
Received Signal Strength Indicator (RSSI): Indicator of the strength
of the received signal. A higher value corresponds to a better
reception. There is no universal relationship between a physical
quantity and a specified RSSI.
Safety function
Function of a machine whose failure can result in an immediate
increase of the risk(s). (ISO 12100)
Safety output
A safety output provides safety-related information.
Safety outputs are OSSDs, for example, or safety-related informa‐
tion on a safety-related network.
Scan cycle time
The scan cycle time is the time the sensor needs for a complete
scan of its detection area.
Example: Time required by the mirror of a safety laser scanner for
one rotation.
SIL
Safety integrity level
SILCL
SIL claim limit (IEC 62061)
GLOSSARY
17
8021219/1ELL/2022-01-21 | SICK
O P E R A T I N G I N S T R U C T I O N S | microScan3 – PROFINET
197
Subject to change without notice