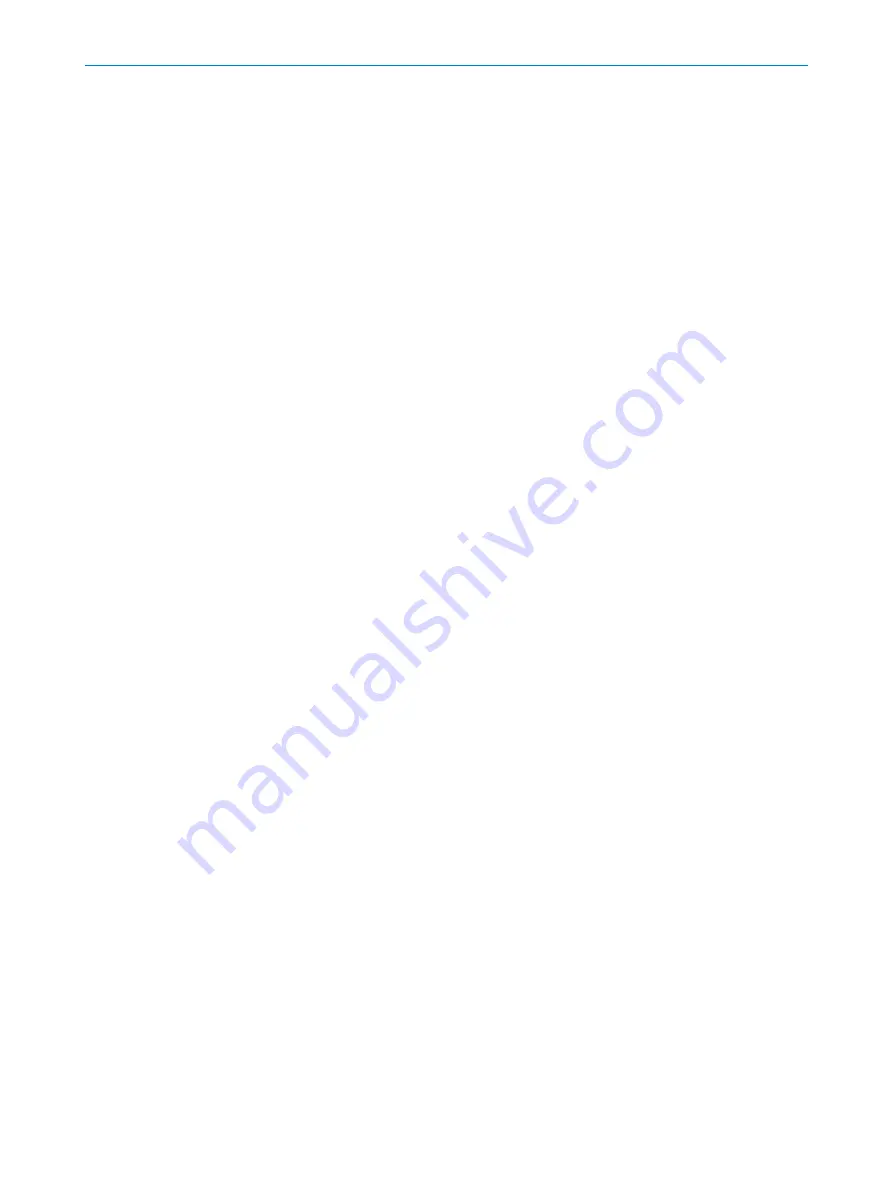
10.1.3
Event handling
Beside the position data the HDSL-system provides a lot of information to the user
[servo controller]. This contains information of the operation conditions, connection
performances as well as error information. These information are available as bit set‐
tings within different registers as well as digital output signals of the IP-core. Within
(SICK-HIPERFACE DSL_event_list; Doc.E_134759) the different information are classi‐
fied into critical, major or minor events. Furthermore a first root cause information is
provided and a first servo controller response. For a stable system during normal opera‐
tion and start-up the event monitoring shall be done as described within (SICK-HIPER‐
FACE DSL_event_list; Doc.E_134759) and in
. For non-safety operation
applications the fast position information needs to be watched only. As long as the fast
position is valid (within the limits of the position estimator set limits) there is no loss of
accuracy in motor controlling and the system can ride through any error situation within
the set tolerances (see position estimator at
10.1.4
Resources
Encoder functions and information are defined as resources. Each individual resource
is identified by a unique resource index (RID). “Long message” transactions enable
access to all resources installed in a HDSL motor feedback system. For further informa‐
tion of the detailed resources handling please refer to
. There are mandatory
resources which are available at all of the HDSL-encoder types. A few of the resources
vary for the different types of the encoders. For the available resources of each encoder
family please refer to the according product information document. At the initial start-
up of the system the servo controller needs to read out the actual encoder configura‐
tion to identify available encoder functionality (see also
10.1.5
Encoder identification
Encoders can have different configurations (resolution, single/multi-turn, motor temper‐
ature reading) or different internal information based on their type (optical or capaci‐
tive). When starting communication initially the electronic type label of the encoder
need to be read to configure the servo controller for the particular encoder:
•
Resolution (steps per turn)
•
Range (revolutions)
•
Motor temperature reading function
•
Encoder type (to differentiate between standard and Safety version)
Based on the actual encoder configuration the according controller settings need to be
done.
10.1.6
Motor commutation
For reading or setting motor commutation no other procedure than laid out for motor
manufacturers in
must be used by the drive controller.
10.1.7
Interface circuit
In
an electrical schematic for the interface circuit is provided with a BOM of
the needed components. Furthermore a description is given with layout design assess‐
ments and advices when designing the PCB-layout and choosing the different compo‐
nents therefore.
10.1.8
DSL line connection
With the HDSL-technology data wires are routed together with motor power lines within
one hybrid cable type. Within the cable certain measures are taken to prevent the data
lines from disturbing electrical noise. At the connection point the data wires need to be
10
DSL COMPONENT INTEROPERABILITY
162
T E C H N I C A L I N F O R M A T I O N | HIPERFACE DSL
®
8017595/ZTW6/2018-01-15 | SICK
Subject to change without notice