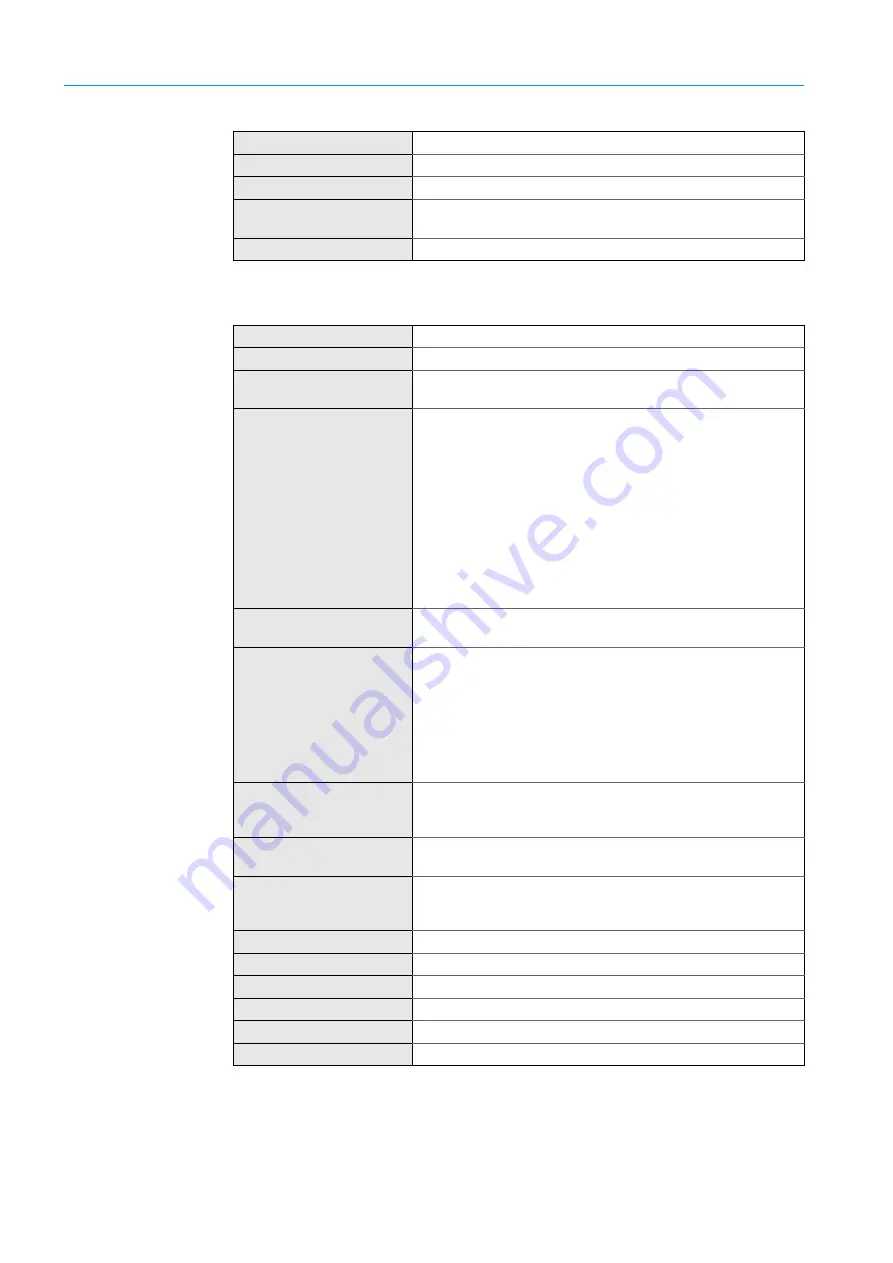
66
8012707/ZVF9/V2-1/2019-04 | SICK
O P E R A T I N G I N S T R U C T I O N S | GM32
Subject to change without notice
9
SPECIFICATIONS
9.2.2
System GM32 TRS-PE
Degree of protection
Standard: IP 65, IP 69K
Operation
Via integrated control unit or SOPAS ET software.
Correction functions
Internal contamination correction
Control functions
Internal zero point control
Check cycle for zero and span point according to QAL3
Options
SCU control unit
Description
In-situ gas analyzer for TRS monitoring in the force-pulp process
Measured variable
NO, NH
3
, SO
2
, CH
3
SH, (CH
3
)
2
S, (CH
3
)
2
S
2,
H
2
S, TRS
Maximum number of
measured variables
8 (plus process temperature and pressure).
Measuring ranges
NH3: 0 ... 30 ppm / 0 ... 50 ppm
NO: 0 ... 40 ppm / 0 ... 150 ppm
SO2: 0 ... 15 ppm / 0 ... 21 ppm
H
2
S: 0 ... 16 ppm / 0 ... 33 ppm
CH
3
SH: 0 ... 7 ppm / 0 ... 23 ppm
(CH
3
)
2
S: 0 ... 5 ppm / 0 ... 18 ppm
(CH
3
)
2
S
2
: 0 ... 6 ppm / 0 ... 12 ppm
TRS: 0 ... 26 ppm / 0 ... 65 ppm
Measuring ranges refer to 1 m measuring path
Measuring ranges depending on application and device version
TRS = H
2
S + CH
3
SH (als H
2
S-equivalent)
For device variant 7: TRS = H
2
S + CH
3
SH + (CH
3
)
2
S + 2x (CH
3
)
2
S
2
Response time (t
90
)
Gas-testable measuring probe (GPP):
≥
120 s, adjustable
Adjustable
Precision
NH
3
:
≥
± 0.7 ppm
NO:
≥
± 0.8 ppm
SO
2
:
≥
± 0.3 ppm
H
2
S:
≥
± 0.7 ppm
CH
3
SH:
≥
± 0.5 ppm
(CH
3
)
2
S:
≥
± 0.4 ppm
(CH
3
)
2
S
2
:
≥
± 0.3 ppm
TRS:
≥
± 1.4 ppm
Ambient temperature
–20 °C ... +55 °C
Temperature change max. ±10 °C/h
For device variant 7: +20 °C ... +30 °C
Storage temperature
–20 °C ... +55 °C
Temperature change max. ±10 °C/h
Ambient humidity
≤
96%
Relative humidity; moisture condensation on optical interfaces not
allowed.
Electrical safety
CE
Degree of protection
Standard: IP 65, IP 69K
Operation
Via integrated control unit or SOPAS ET software.
Correction functions
Internal contamination correction
Control functions
Internal zero and span point test
Options
SCU control unit
Table 21: Technical data GM32 system TRS-PE
Table 20: (Continued)Technical data GM32 system standard Probe version