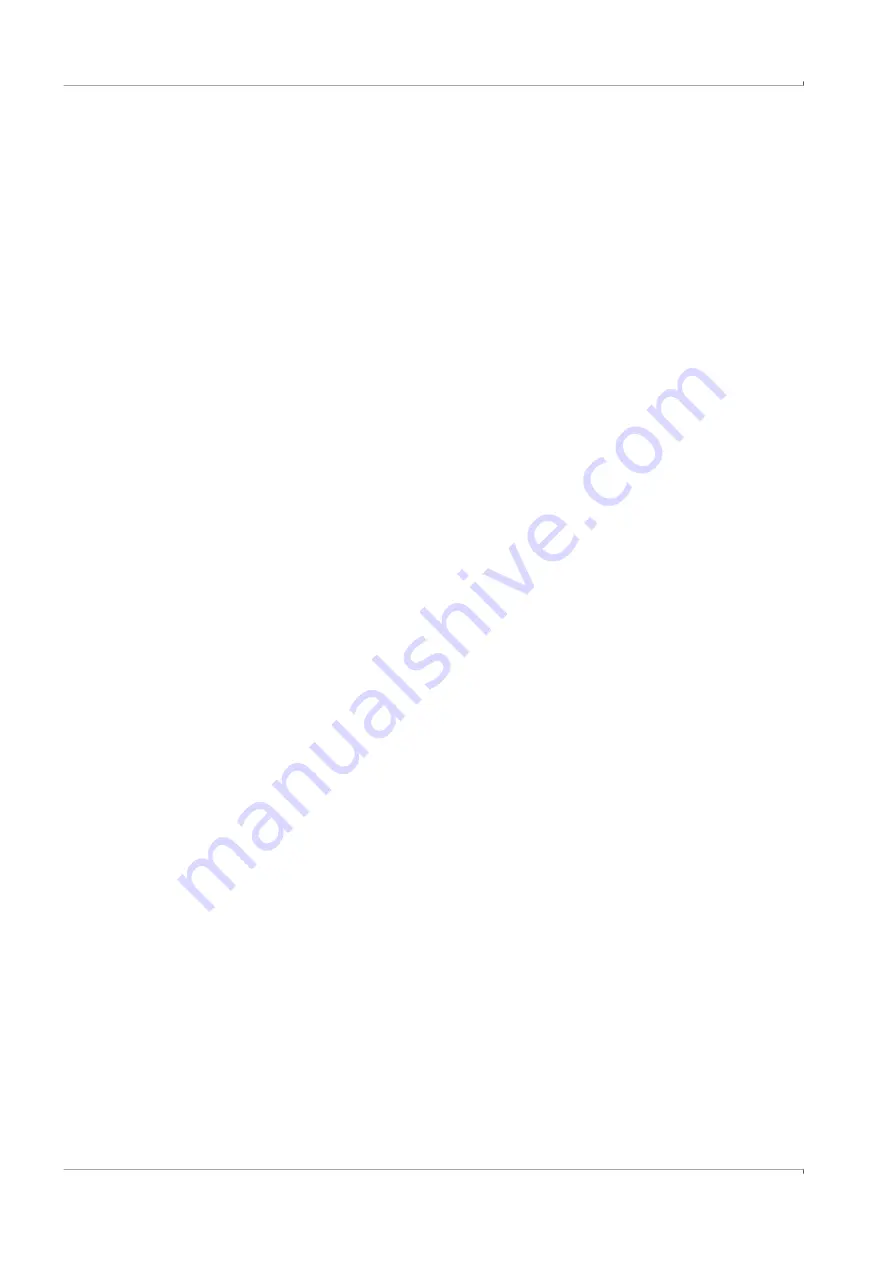
42
FLOWSIC600-XT · Operating Instructions · 8018846/1BHP/V2-1/2021-05 · © SICK Engineering GmbH
Installation
Su
bje
ct to
ch
an
ge
w
ith
ou
t n
otic
e
3.3
Mechanical installation
3.3.1
Preparations
▸
The following tools and materials are required to install the FLOWSIC600-XT:
– Lifting gear or fork lift (load according to the weight specification on the type plate)
– Box wrench with size suitable for flange installation
– Thread seal (e.g. PTFE tape) and flange gaskets
– Bolt lubricant
– Leak detection spray
3.3.2
Choosing flanges, seals and other components
For flange connections only use pipeline flanges, bolts, nuts and gaskets suitable for the
maximum operating pressure, maximum operating temperature as well as ambient and
operating conditions (external and internal corrosion).
The FLOWSIC600-XT can be installed in straight inlet and outlet pipes depending on the
installation configuration (
):
The inlet and outlet pipes must have the same nominal size as the meter body. The inner
diameter is shown in the Data Sheet and is based on the nominal flange value and the
standard. The max. permitted difference of the inner diameter of the inlet pipe from that of
the meter body is 3%. The permitted difference is 1% for meter bodies with straight
measuring section.
Any welding beads and burs on the flanges of the inlet pipe must be removed.
3.3.3
Requirements to the measuring point
● The meter body may be installed in a horizontal or vertical position.
In case of horizontal installation, the meter body must be aligned so that the planes
formed by the measuring paths are horizontal. This prevents dirt in the pipeline from
entering the transducer ports. Vertical installation is only possible when the measuring
system is used for dry, non-condensing gases. The gas flow must be free from any for
-
eign material, dust and liquids. Otherwise use filters and traps.
● Do not mount equipment or fittings which may adversely affect the gas flow directly
before the FLOWSIC600-XT
● Seals on the flange connections between meter body and pipeline must not protrude
into the pipeline. Any protrusion into the flowing gas stream may change the flow profile
and thus adversely affect measuring accuracy.
● Pressure measuring devices must be connected to the pressure tap provided. The
pressure inlet nozzle is marked with p
m
.
● As required by the customer or as standard, the pressure taps are designed as 1/8,
1/4 or 1/2 inch NPT connection (female), depending on meter sizes and customer
requirements.
● For the leak-proof connection on the pressure line, a suitable thread sealing agent (e.g.
PTFE tape) must be used when the pressure connection adapter is screwed in. The leak
tightness must be checked after installation and commissioning. All leaks must be
repaired. Arrange the temperature sensors as shown in