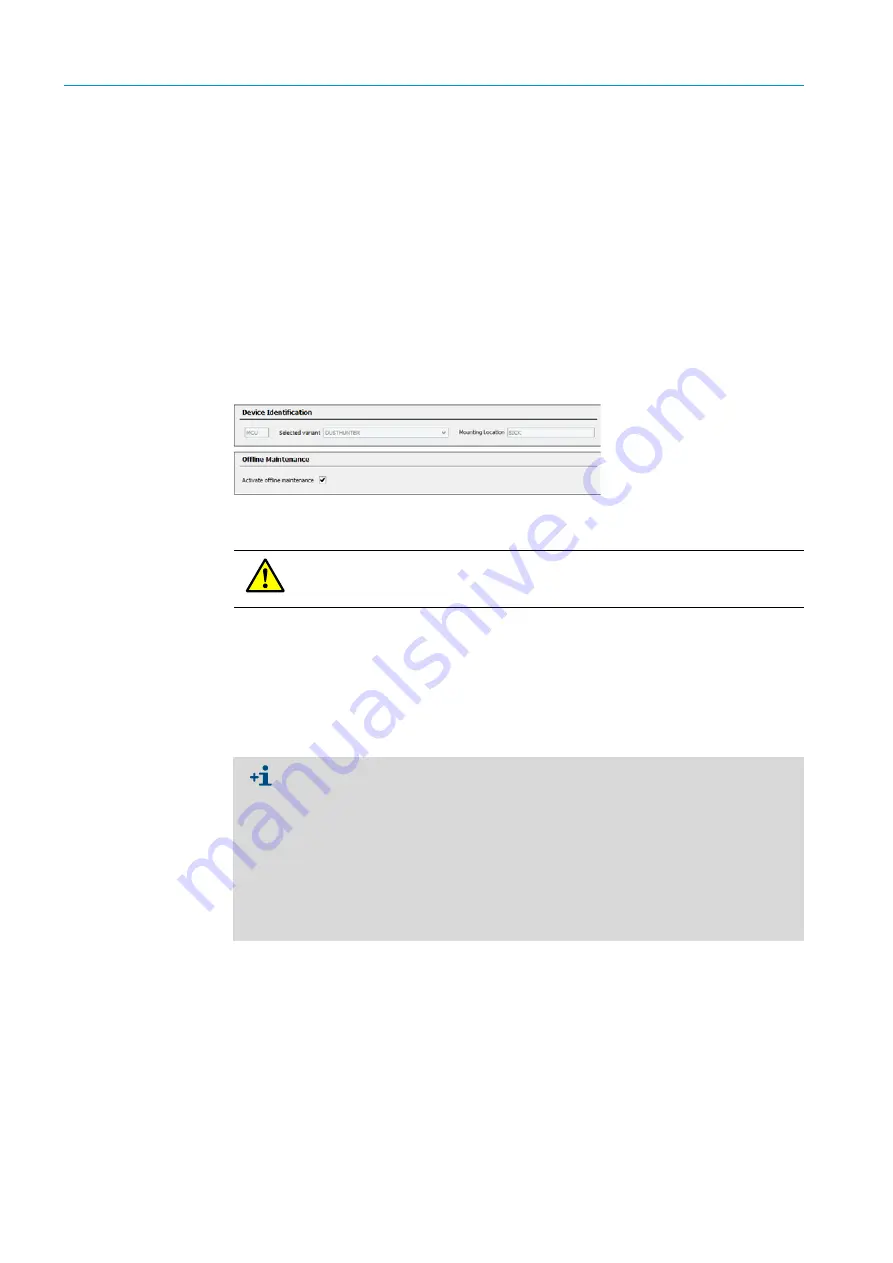
82
8012426/YWL2/3-0/2016-08| SICK
O P E R A T I N G I N S T R U C T I O N S | DUSTHUNTER SP100
Subject to change without notice
5
MAINTENANCE
5
Maintenance
5.1
General
The maintenance work to be carried out is limited to cleaning work and securing the purge
air supply function.
Take the following steps to set the measuring system to “Maintenance” mode before
starting maintenance work.
▸
Connect the MCU to the laptop/PC using the USB line and start program SOPAS ET.
▸
Connect with the MCU (
see “Connection to the device via USB line”, page 55
▸
Enter the Level 1 password (
see “Password and operating levels”, page 75
).
▸
Set the sender/receiver unit to “Maintenance”: Click “Maintenance sensor”)
Fig. 51: SOPAS ET menu: MCU/Maintenance/Maintenance
Resuming measuring operation
Resume measuring operation after completing the work (deactivate the “Maintenance on/
off” checkbox in the “Maintenance / Operation” window and click “Set State”).
Maintenance intervals
The equipment operator must specify the maintenance intervals. The period depends on
existing operating parameters such as dust content and state, gas temperature, how the
equipment is run and ambient conditions.
The equipment operator must specify the specific work to be carried out and its perfor-
mance in a Maintenance Manual.
WARNING:
Observe the relevant safety regulations as well as the safety notices (
) during all work.
●
“Maintenance” mode can also be set using the buttons on the display on the MCU
(
) when the LC-Display option is present or by con-
necting an external maintenance switch to the terminals for Dig In2 (17, 18) in the
MCU (
see “Connecting the MCU control unit”, page 47
●
An automatic function check is not carried out during “Maintenance”.
●
The value set for “Maintenance” is output on the analog output (
analog outputs parameters”, page 65
). This is also applicable when a malfunction is
present (signaled on relay output).
●
The “Maintenance” mode is reset when there is a voltage failure. In this case, the
measuring system switches automatically to “Measurement” after the operating volt-
age is switched on again.