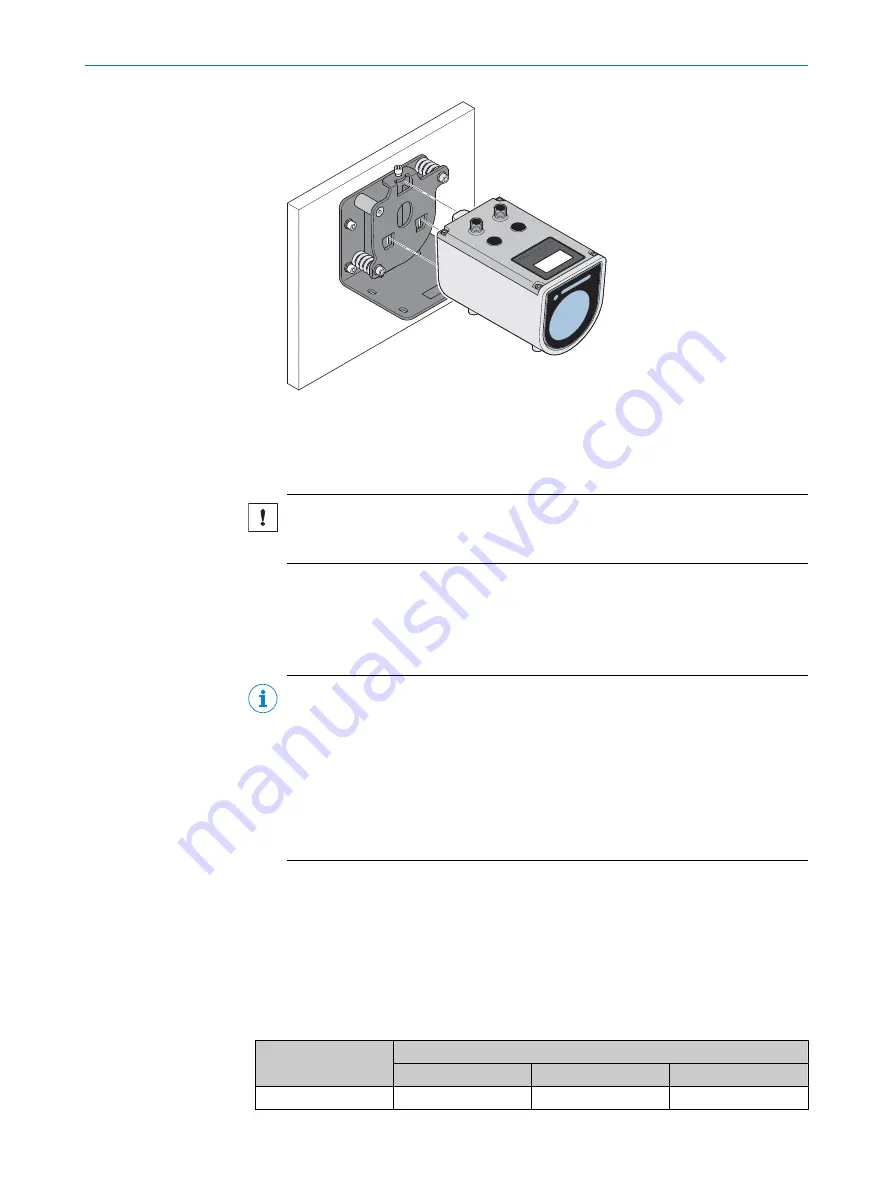
2
3
4
1
2
1
Figure 15: Inserting the distance sensor into the alignment bracket
1
Alignment bracket
2
Distance sensor
4.
Securing the distance sensor with hexagonal socket screw
NOTICE
The hexagon socket screw must be sufficiently tightened (with a torque of at least
3 Nm). Do not counter the hexagonal socket screw.
5.7
Aligning distance sensor
When aligning the distance sensor, you can select between two processes, which you
can also combine:
NOTE
When using the alignment laser, make sure this laser is located about 30 mm
above the measuring laser,
. The max. angular deviation
between the measuring laser optics axis and alignment laser optics axis is 4 mrad
(4 mm per meter distance from the front device edge).
Switch alignment laser on/off,
"Switching the laser on and off", page 79
.
If the alignment laser is not visible when aligning on natural surfaces due to a
large distance or a bright environment, temporary use of (retro-reflective) reflective
tape on the measuring object surface is recommended.
■
Alignment using the alignment laser:
Align the distance sensor so that the light spot of the measuring laser hits the
center of the measuring object.
■
Alignment using the signal level display in the device display, via SOPAS ET or
PROFIBUS:
Align the distance sensor so that a level maximum is displayed at the expected
distance. Recommended at large distances at which the light spot of the align‐
ment laser might no longer be detected with precision.
Table 23: DL1000: Typical signal level on PLxxxDG reflectors
Distance [m]
Signal level
PL240DG
PL560DG
PL880DG
1
10500
10500
10500
MOUNTING
5
8024560/1A19/2021-06-30 | SICK
O P E R A T I N G I N S T R U C T I O N S | DT1000 PROFIBUS DP and DL1000 PROFIBUS DP
47
Subject to change without notice