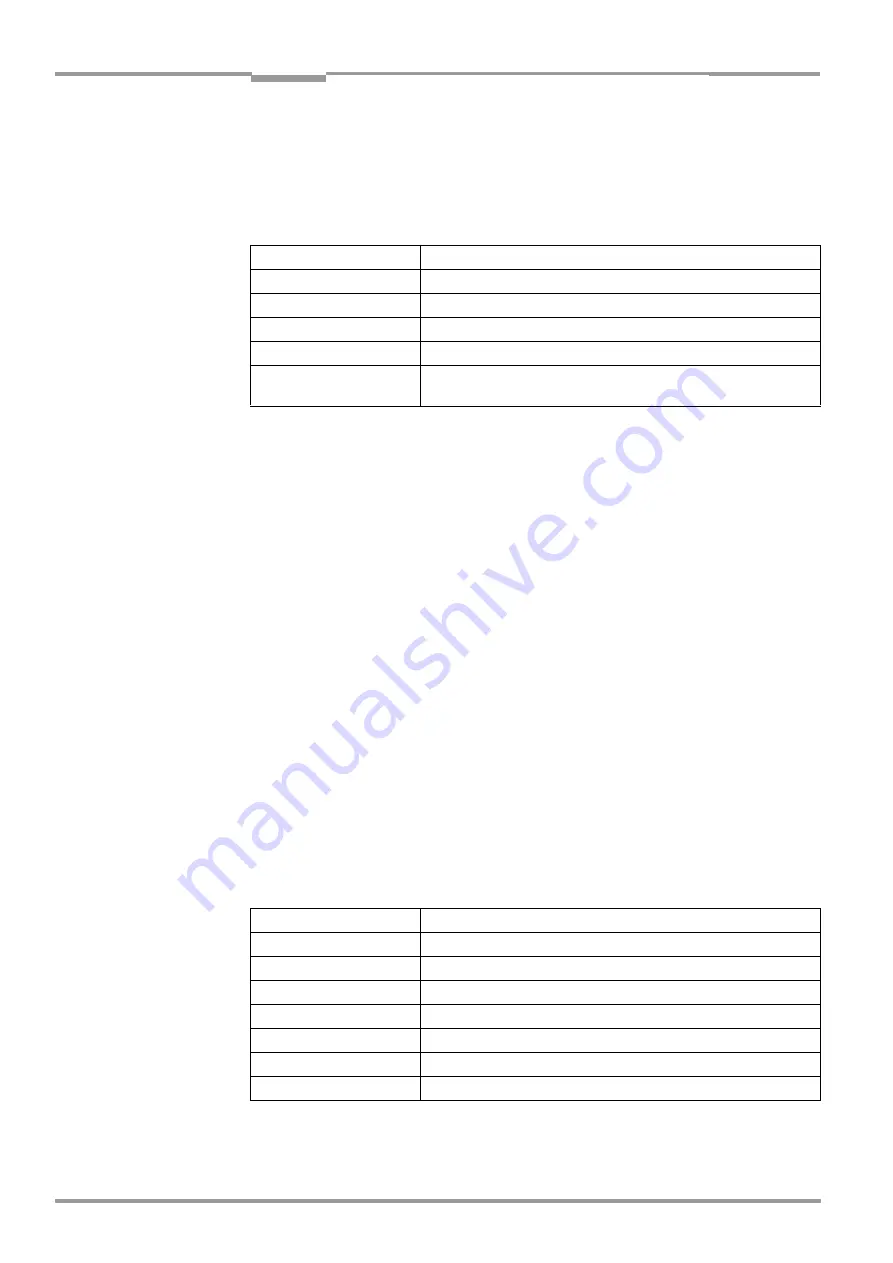
Chapter
10
Operating Instructions
CLV 480 Bar Code Scanner
10-48
©
SICK AG · Division Auto Ident · Germany · All rights reserved
8 010 080/O824/10-02-2005
Appendix
Entering a bar code using a terminal/PC keyboard
1.
Connect the terminal /PC with Terminal Emulation program to the terminal interface on
the CLV (via AMV/S 60).
For the pin assignment, see
Chapter 5.5.5 Connecting the CAN
2.
Set the communication parameters and data output format as shown in
.
3.
Enter the data content of the bar code on the keyboard.
The terminal sends the individual characters to the CLV immediately.
Use the backspace key to correct input errors.
4.
Terminate the data content with the control character <CR>.
The CLV then interprets all further characters as a new data string and ignores other
control characters. The data content itself must not contain any control characters.
5.
Once the active reading pulse has ended, the CLV sends the data received from the PC
to the host via the host interface.
Entering bar codes using a hand-held scanner (with integrated decoder)
1.
Connect the hand-held scanner with decoder to the terminal interface of the CLV (via
AMV/S 60).
For the pin assignment,
see
Chapter 5.5.5 Connecting the CAN interface,
.
2.
Set the data format and communication parameters on the hand-held scanner as
shown in
.
3.
Read the bar code with the hand-held scanner.
Once the active reading pulse has ended, the CLV sends the data received from the PC
to the host via the host interface.
If you connect a SICK Hand-held Scanner from the IT 38xx/46xx/48xx/58xx series, set the
communication parameters and data output (data + terminator) as shown in
.
Parameter
Value
Data transmission rate
9,600 bd
Data bits
8
Parity
None
Stop bits
1
Data output format
Data terminator
e. g. 1234
CR
Table 10-9: Communication parameters on the terminal/PC for the auxiliary input
Parameter
Value
Data transmission rate
9,600 bd
Data bits
8
Parity
No
Stop bits
1
Data interface
RS 232
Prefix (Header)
Clear all Prefixes
Suffix (Terminator)
CR
Table 10-10: Communication parameter settings for the SICK Hand-held Scanner from the
IT 38xx/46xx/48xx/58xx series