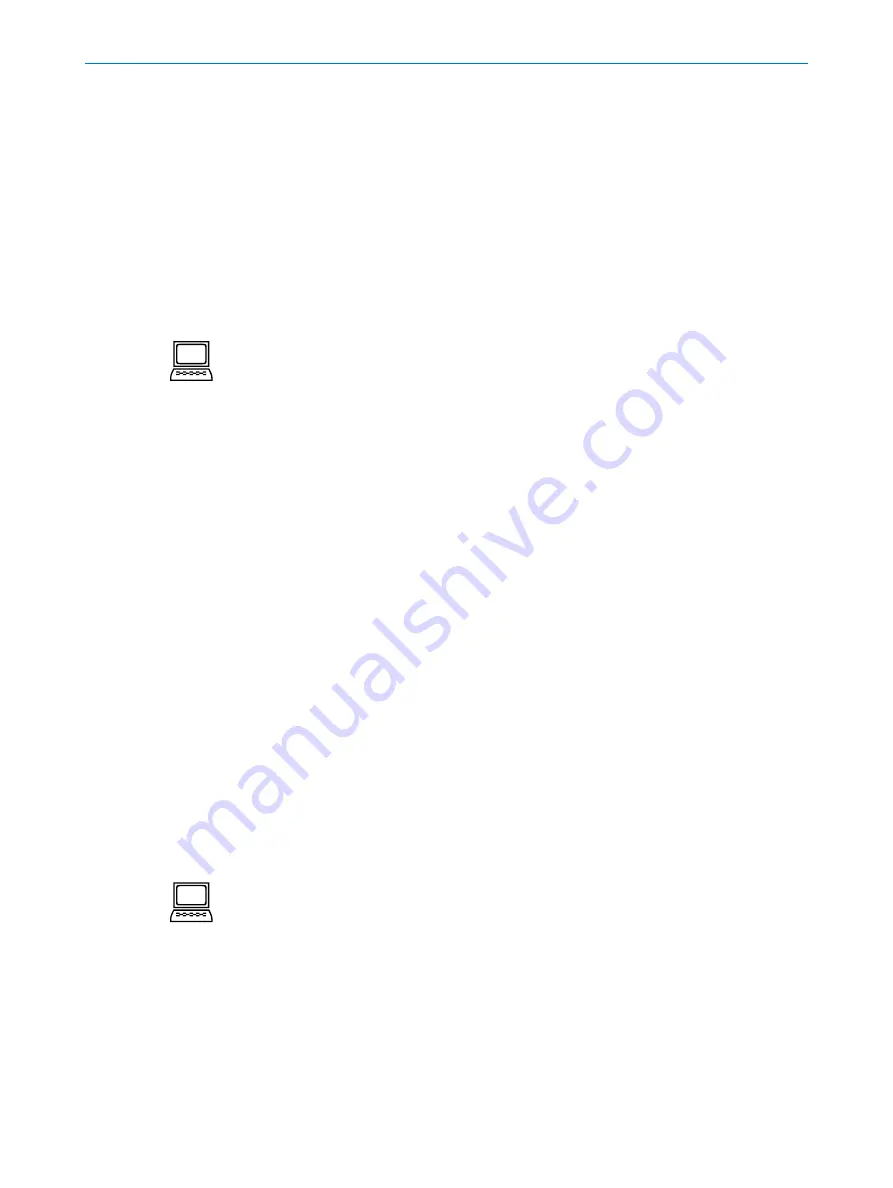
O P E R AT I N G I N S T R U C T I O N S |
Bulkscan LMS511
8014829/ZNC5/2017-06-06|
S I C K
Subject to change without notice
1 7
CONFIGURABLE FUNCTIONS
4.2
Measurement of the volume
The sensor determines the running total of the volume transported.
The sensor calculates the volume from the measured contour and the conveyor¬ belt
speed.
SOPAS indicates this value as a volume sum and the sensor outputs the sum in the
measured value telegram. On the other hand, the volume is signaled as a switching
point per volume quota reached on a digital output, e.g., one switching point per 100
m³.
You can smooth the measured values with the aid of the averaging filter (see "4.11
Averaging filter“ on page 24).
How to configure the calculation of the volume sum:
Switch to the
Measurement
tab.
Configure the
Belt speed
(see "4.1 Setting the belt speed“ on page 16).
Configure the
Flow averaging filter
, if required.
How to configure the signaling of the volume quota on a digital output:
Switch to the
Interfaces
tab.
Click on
Digital outputs
to open the
Digital outputs
tab (see "4.13 Digital outputs“
Select the assignment
Volume quota
for the required output.
Select the required
Logic
.
Configure the
Volume quota
(volume per pulse).
Configure the
Pulse width
.
Ensure that the duration of the pause between pulses is longer than the cycle time
resulting from the scan frequency (see "8.4 Monitoring of the contamination degree“ on
4.3
Measurement of the mass
The sensor determines the running total of the mass transported.
The sensor calculates the mass from the measured contour, the bulk density, and the
belt speed.
SOPAS displays this value as a mass sum and the sensor outputs the sum in the mea-
sured value telegram. On the other hand, the mass is signaled as a switching point per
mass quota reached on a digital output, e.g., one switching point per 10 t.
You can smooth the measured value with the aid of the averaging filter (see "4.13 Digi
How to configure the calculation of the mass sum:
Switch to the
Measurement
tab.
Configure the
Belt speed
(see "4.1 Setting the belt speed“ on page 16).
Configure the mass flow rate as a calculated value.
Configure the
Bulk density
as
Fixed value
or
Analog value
.
Configure the
Flow averaging filter
, if required.
How to configure the signaling of the mass quota on a digital output:
b
Switch to the
Interfaces
tab.
b
Click on
Digital outputs
to open the Digital outputs tab (see "4.13 Digital outputs“ on
Select the assignment
Mass quota
for the required output.
Select the required
Logic.
Note
Note