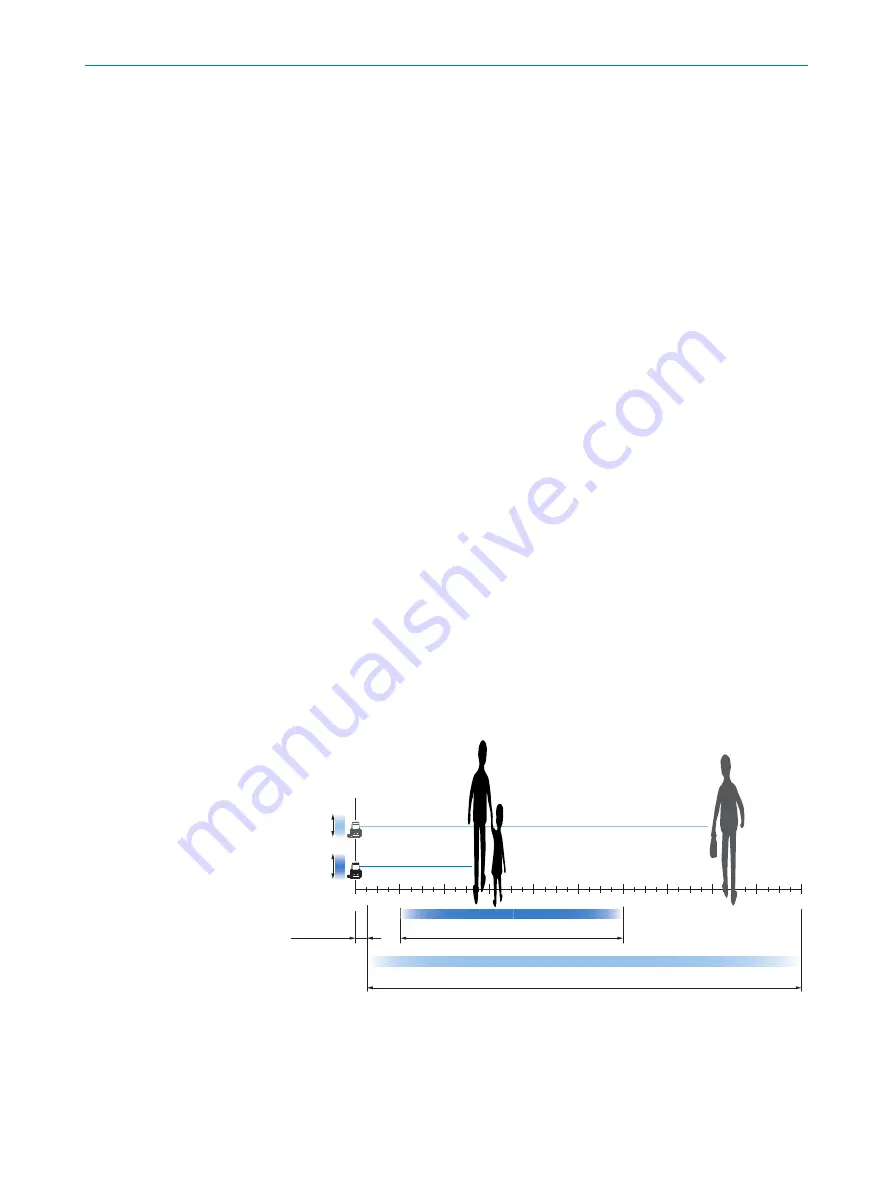
5
Mounting
5.1
Mounting instructions
•
Observe the technical data.
•
Protect the sensor from direct and indirect sunlight.
•
To prevent condensation, avoid exposing the device to rapid changes in tempera‐
ture.
•
The mounting site has to be designed for the weight of the device.
•
The device can be mounted in any position.
•
It should be mounted so that it is exposed to as little shock and vibration as possi‐
ble. Optional mounting accessories are available,
•
In application areas with severe vibrations or shocks caused by vibrations, jolts or
abrupt changes in directions (e.g., when mounted to a manned forklift truck),
mounting with vibration dampers is to be carried out (
). Mount the device in a freely suspended manner.
•
During mounting, make sure there is no reflective surface behind the reference
target,
see "Setup and dimensions", page 11
.
•
To avoid inaccurate measurements when installing multiple devices: Make sure
that the laser spot of one device is not in the visible range of another device,
"Mutual interference", page 18
•
Avoid having shiny or reflective surfaces in the scanning range, e.g., stainless
steel, aluminum, glass, reflectors, or surfaces with these types of coatings.
•
Protect the device from moisture, contamination, and damage.
•
Make sure that the status indicator is clearly visible.
•
The M3 x 5 screws included with delivery are intended for mounting the fastening
clips via the blind hole threads on the rear or underside of the device,
. If the mounting clamps are not used or if other screws
are used, the screws must not be screwed into the thread by more than 2.8 mm.
The maximum tightening torque is 0.8 Nm.
5.2
Mounting position
For reliable function, observe the following framework conditions when positioning the
device.
0.90 ... 1.20
3
0.40 ... 0.60
2
min. 0.25
1
typ. 1.00 ... 6.00
2
0
1
2
3
4
5
6
7
8
9
10
max. 0.25 ... 10.00
3
1
Minimum distance from device to detected people
2
Recommendation: Measurement at knee/upper thigh height (device height 0.4 m to
0.6 m) at a monitoring distance of typ. 1.00 m to 6.00 m.
3
Recommendation: Measurement at hip/stomach height (device height 0.90 m to 1.20 m)
when the maximum monitoring distance of 0.25 m to 10.00 m is utilized.
MOUNTING
5
8025963//2020-08-05 | SICK
O P E R A T I N G I N S T R U C T I O N S | TiM8xx DistanceGuard
17
Subject to change without notice