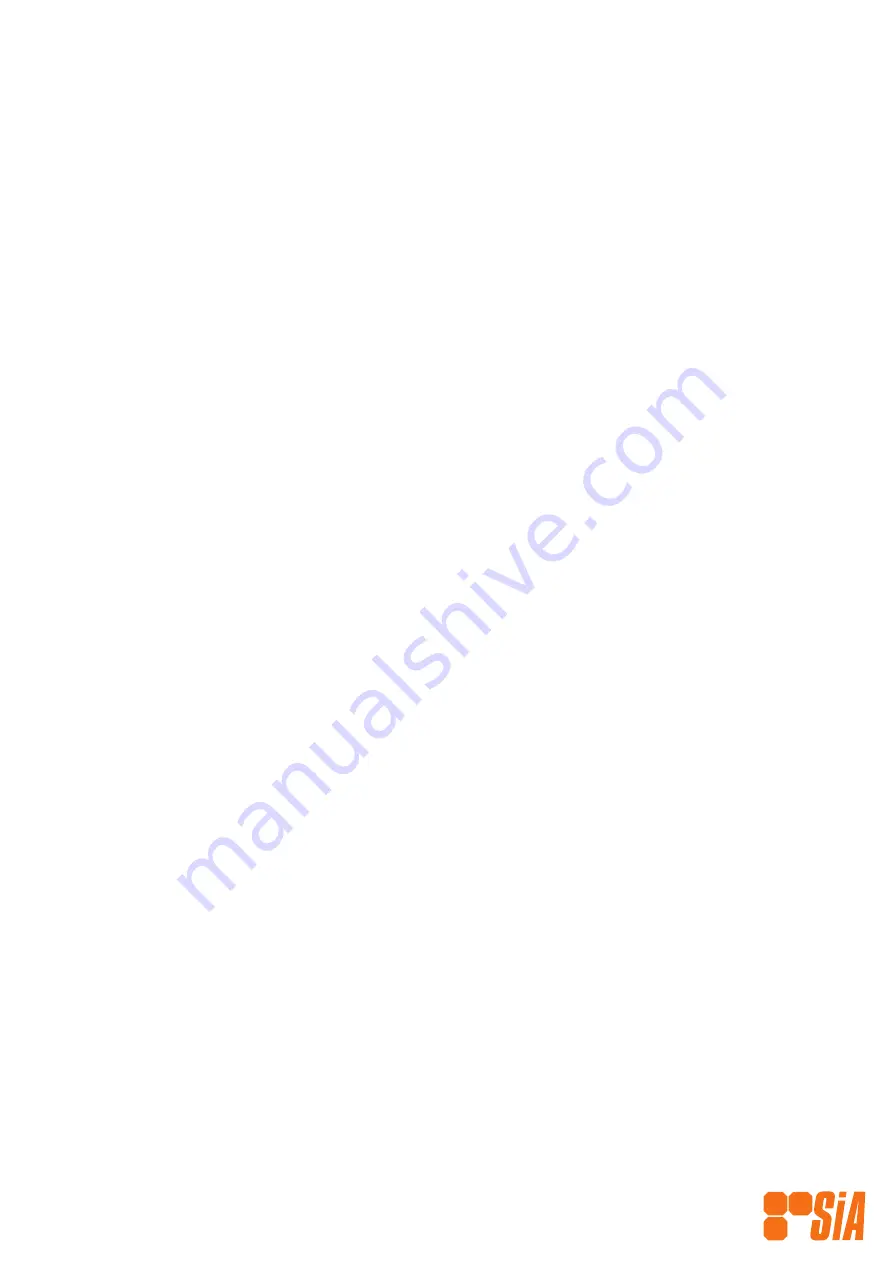
9
2.1 Mounting,Orientation & Environment
The preferred orientation for mounting is with the Liquid End pointing down, the Timer Module
on top and the Gearmotor horizontal to the ground. This facilitates “bleeding” of the pump and
maximises the life of the seals within the pump. The inlet of the Liquid End should be no higher
than level with the lowest chemical level, to ensure a positive head on the inlet check valve. With
Duplex configurations (ie 2 liquid ends on 1 drive), the Liquid Ends will be horizontal to the ground
and the position of the inlet and outlet check valves will be reversed. Ensure that the inlet check
valves, which are gravity-style, are facing downwards.
We recommend installing the assembly within a weatherproof enclosure. Where this is not practical,
ensure as much weather and dust protection is afforded the whole assembly and the motor in
particular. An SiA custom cover for the motor and gearbox assembly can be ordered separately if
required.
Where environmental conditions are harsh, ie very wet, where there is salt water &/or dust or
snow, consider coating the assembly with an appropriate coating or cover. In wet conditions in
particular, we recommend use of a non hardening mastic on all mating parts, which is available
as an option. Please contact Solar Injection Australia or an SiA Authorised Technical Agent before
finalising the design of the installation.
Use the two M6 mounting holes to securely mount the assembly to any rigid frame or sub-
assembly with mounting brackets (not supplied but available).
2.2 Installation — Step by Step
1. Discard all plastic closures on the Liquid End and align pump connections as dictated by your
overall system design.
2.
Connect the suction check valve to a gravity-fed chemical source. This pump requires a flooded
suction. We recommend installation of filters to the suction of each Liquid End and some form
of pump inlet isolation. Warranty may be affected if you do not.
3. Connect the discharge check valve to the process line. We recommend installation of a pressure
relief valve to the discharge of each Liquid End. Warranty may be affected if you do not.
4.
Check that the pump adaptor ring is firm.
5.
Open the bleeder valve until chemical starts to flow then re-tighten.
6. Ensure that the DC power supply that you are using corresponds to the DC power required. 12
volts supply to 12 volts equipment. 24 volts supply to 24 volts equipment
WARNING
: Ensure the DC power supply to the DC Drive Motor is fused with the correct
fuse. See Section 2.0 for details.
WARNING
: For AC models, all AC equipment must be installed by licenced electrical
personnel.
7. Before connecting the supply leads to the DC motor make ensure the supply is isolated.
8. Connect motor power leads to supply, Red to Red (+) and Black to Black (-).
If installing with an SIAT75001 Timer/Controller, connect the battery power supply and
motor leads to the four screw terminals clearly marked and located on the lower front
face of the timer.
WARNING
: Connecting the main power supply in the reverse polarity can cause
immediate failure of the electronics within the timer module.
WARNING
: As the control and isolation of the DC Drive is supplied by the operator,
care must be taken in selecting equipment to carry out these functions. We recommend
discussing alternative operator-designed control methods prior to installation.