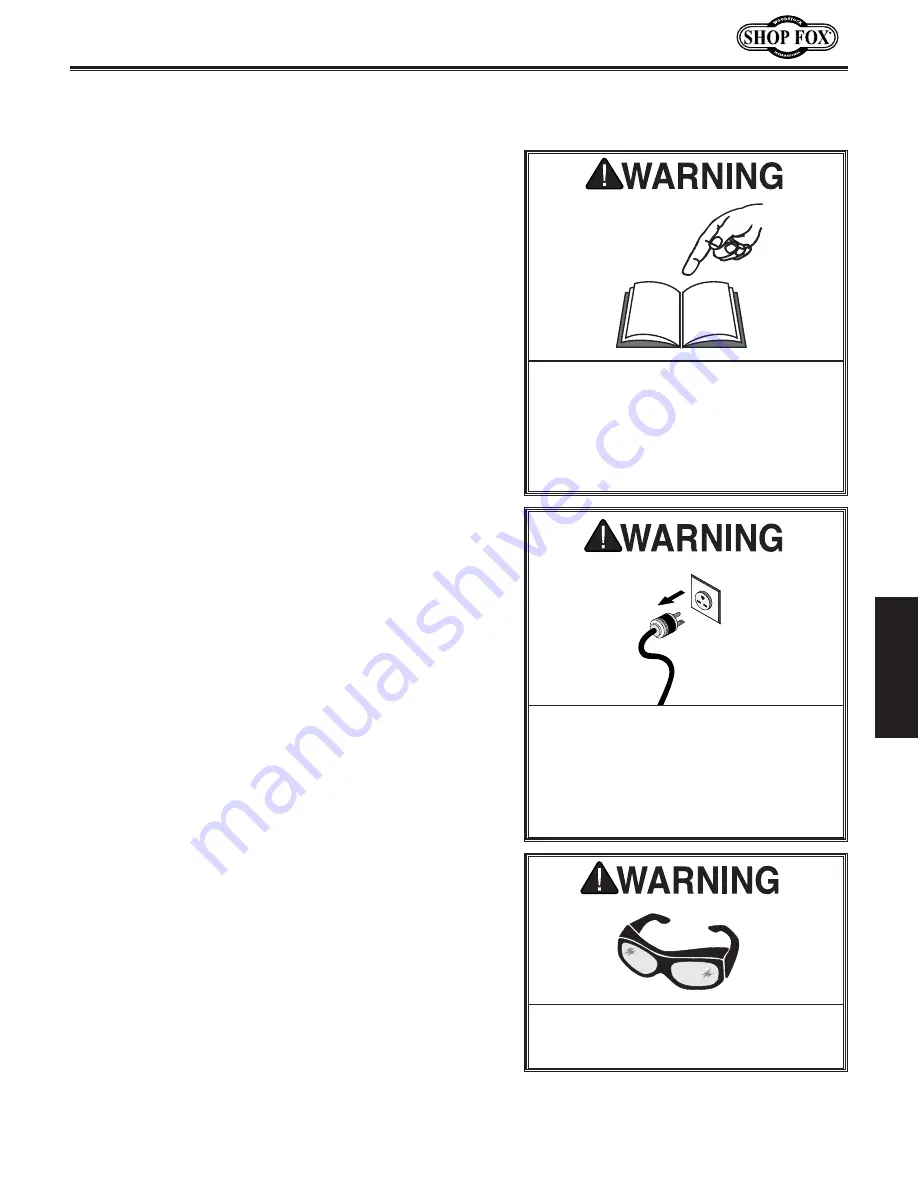
-17-
Model W1768/W1769 (For Machines Mfg. Since 5/07)
O
PE
R
ATIO
NS
OPERATIONS
General
This machine will perform many types of operations
that are beyond the scope of this manual. Many of these
operations can be dangerous or deadly if performed
incorrectly.
The instructions in this section are written with the
understanding that the operator has the necessary
knowledge and skills to operate this machine.
If.at.
any.time.you.experience.difficulties.performing.any.
operation,.stop.using.the.machine!
If you are an inexperienced operator, we strongly
recommend that you read books, trade articles, or seek
training from an experienced power feeder operator
before performing any unfamiliar operations.
Above.all,.
your.safety.should.come.first!
Always.wear.safety.glasses.when.oper-
ating.this.machine..Failure.to.comply.
may.result.in.serious.personal.injury.
DO.NOT.investigate.problems.or.adjust.
the.machine.while.it.is.running..Wait.
until. the. machine. is. turned.
OFF
,.
unplugged. and. all. working. parts.
have.come.to.a.complete.stop.before.
proceeding!
READ. and. understand. this. entire.
instruction. manual. before. using. this.
machine..Serious.personal.injury.may.
occur. if. safety. and. operational. infor-
mation.is.not.understood.and.followed..
DO.NOT.risk.your.safety.by.not.reading!
Basic.Use.and.Care
Power feeders reduce kickback hazards and improve
cutting results by feeding in a consistent and stable
manner. Remember, do not to stand in the path of
potential kickback. When not in use, support the power
feeder with a wooden block so the rubber wheels are
raised above the table and do not compress from the
weight of the power feeder.
The lock levers and handcranks allow you to adjust the
power feeder tracking and height to accommodate many
workpiece sizes. Before loosening any lock lever, always
support the power feeder with a block of wood, so the
power feeder does not drop and cause damage.
Adjust the power feeder so it is toed-in approximately
1° to 1.5° degrees towards the machine fence. This
adjustment will ensure the power feeder wheels slightly
push the workpiece against the fence during cutting
operations (see
Figure.8.
on
.Page.14
). A featherboard
may be used on the infeed side to help feed long or large
stock.
Next, adjust the power feeder so the rubber wheels are
parallel with the table surface, and are
1
⁄
8
" lower than
the thickness of your workpiece. This adjustment ensures
that the workpiece will not slip or hang in the middle of
a cut. Always double check that the power feeder wheels
are slightly lower than the workpiece before you begin
feeding operations. Otherwise, the workpiece may slip
and kickback.