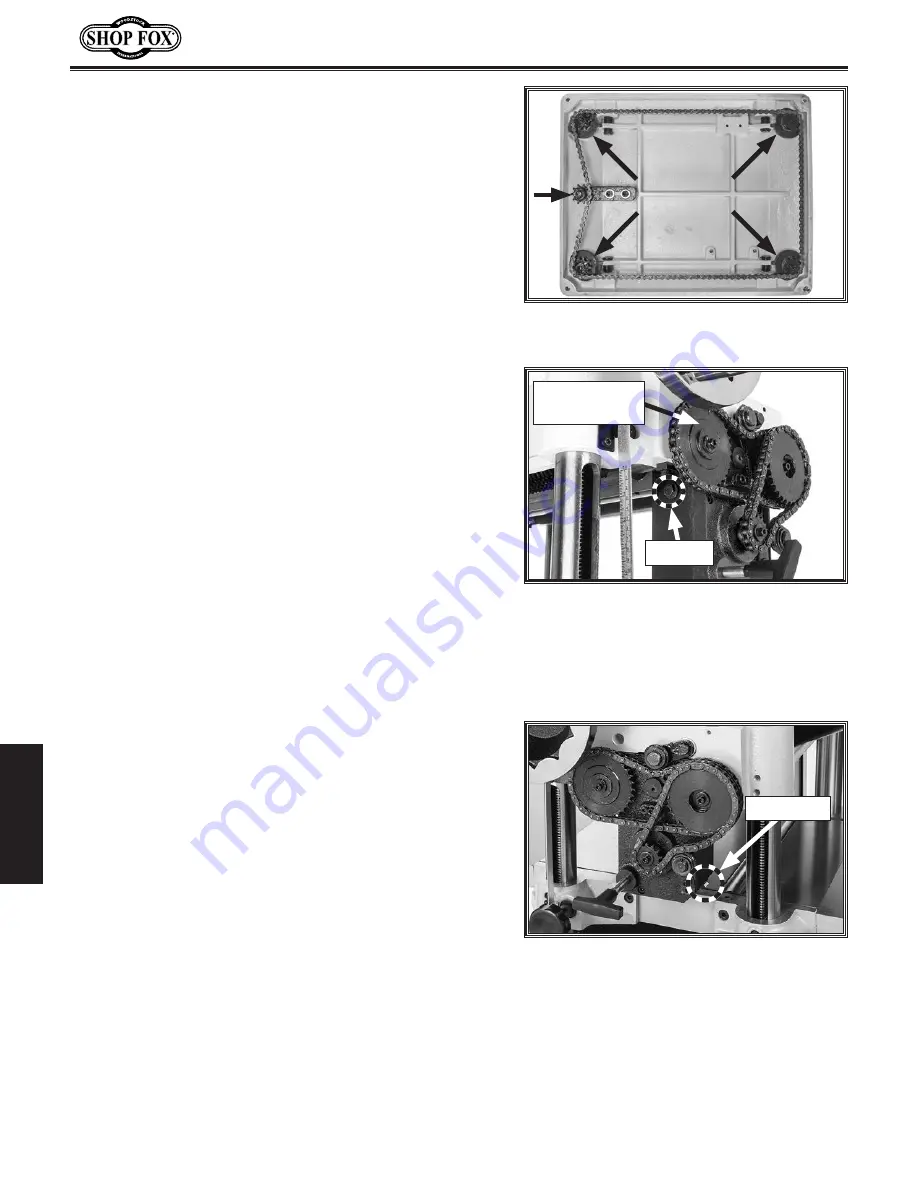
-34-
M
A
INTE
N
A
N
CE
W1742W, W1742SW, W1754W, W1754SW (Mfd. Since 9/15)
Table.Height.Chain.&.Sprockets
Grease Type ........................... Lithium-Based NLGI#2
Frequency ..................... Every 160 Hours of Operation
The table leadscrews are synchronized by the table height
chain and sprockets located underneath the planer base
(see
Figure.36
). Use shop rags and mineral spirits to clean
away debris and grime, then brush on a light coat of
multi-purpose grease to the chain and sprockets.
Figure.36.
Table height chain and
sprockets as viewed from underneath base.
Drive.Chain.&.Sprockets
Grease Type ........................... Lithium-Based NLGI#2
Frequency ..................... Every 160 Hours of Operation
The infeed and outfeed rollers receive the transferred
power from the cutterhead through the drive chain
system on the right side of the machine, as shown in
Figure.37
.
Remove the table height handwheel and the safety covers
attached to the inside of the drive chain cover, then
remove the cover to access these parts.
Use shop rags and mineral spirits to clean away any debris
and grime, then brush on a light coat of multi-purpose
grease to the chain and sprockets.
Gearbox.Oil
Oil Type ......................... ISO 320 or SAE 140 Gear Oil
Oil Amount ................................................ 20 Oz.
Frequency ................ After First 20 Hours, Then Yearly
Note:
SAE 85W-140 multi-weight gear oil may also be used
as a substitute. DO NOT mix oil types!
Note:
We recommend that you replace the gearbox oil
after the first 20 hours of operation. This is a normal
break-in procedure and will help maximize the service life
of the machine by flushing away any particles from the
break-in and manufacturing process.
Although it is not necessary to remove the drive chain
cover to access the fill and drain plugs, it is more
convenient to do so (see
Figures.37–38
). Add oil into the
fill-plug hole until it just reaches the fill plug.
Figure.37.
Location of drive chains,
sprockets, and fill plug.
Fill Plug
Figure.38.
Location of gearbox drain plug.
Drain Plug
Drive Chain
and Sprockets