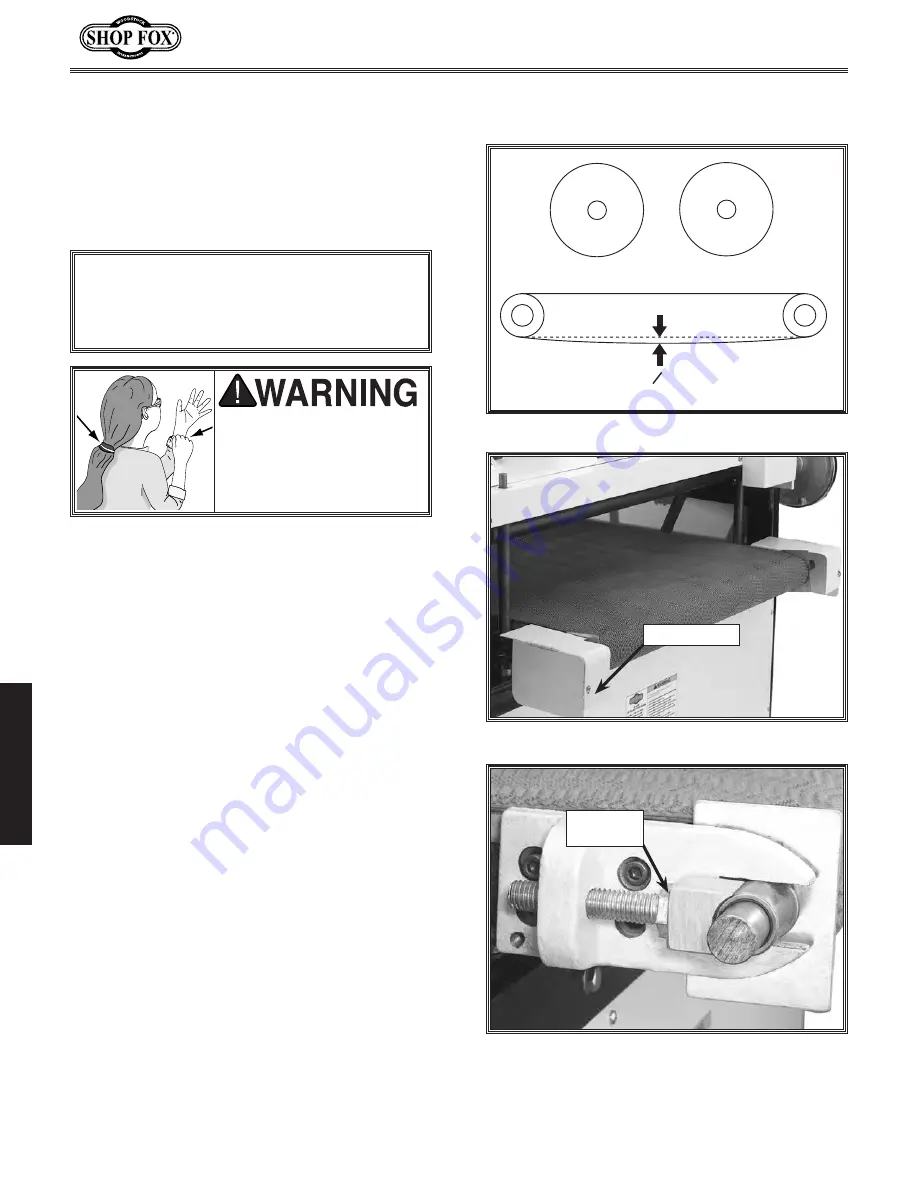
ADJUSTMENTS
-22-
Conveyor Belt
For this adjustment, you will adjust the feed
conveyor belt hanging gap and the tracking, so the
conveyor runs in the center of the table and the
drive roller does not slip at maximum sanding
load. See
Figure 39
.
To adjust the feed conveyor belt tension and
tracking, do these steps:
1.
Remove the screws from the feed conveyor
safety covers and open the covers. See
Figure
40
.
2.
Locate the conveyor roller adjustment bolts
at the infeed roller. See
Figure 41
.
• If the feed conveyor belt is loose, turn both
conveyor roller adjustment bolts counter-
clockwise the same amount until the belt
hangs with a
1
⁄
2
" gap.
• If the feed conveyor belt tracks to the right,
start the conveyor and slightly turn the
right-side conveyor roller adjustment bolt
counter-clockwise.
• If the feed conveyor belt tracks to the left,
start the conveyor and slightly turn the left-
side conveyor roller adjustment bolt
counter-clockwise.
3.
Close the safety covers and run the feed conveyor
for 15 minutes at the fastest setting to make sure
the belt tracks in the center of the table.
4.
Repeat
Steps
2
and
3
until the belt tracks in
the center of the table.
5.
Turn the feed conveyor
OFF
and install the
safety cover screws.
2"
1
Figure 39.
Conveyor belt hanging gap.
NOTICE
ONLY
make adjustments to the infeed roller side
so the drive-chain tension is not affected.
Make sure loose clothing
and long hair is secured
and kept away from all
moving parts.
Figure 41.
Conveyor roller adjustment bolts.
Figure 40.
Infeed-conveyor safety covers.
Cover Screws
Adjustment
Hex
Summary of Contents for SHOP FOX W1678
Page 48: ...NOTES...
Page 49: ......