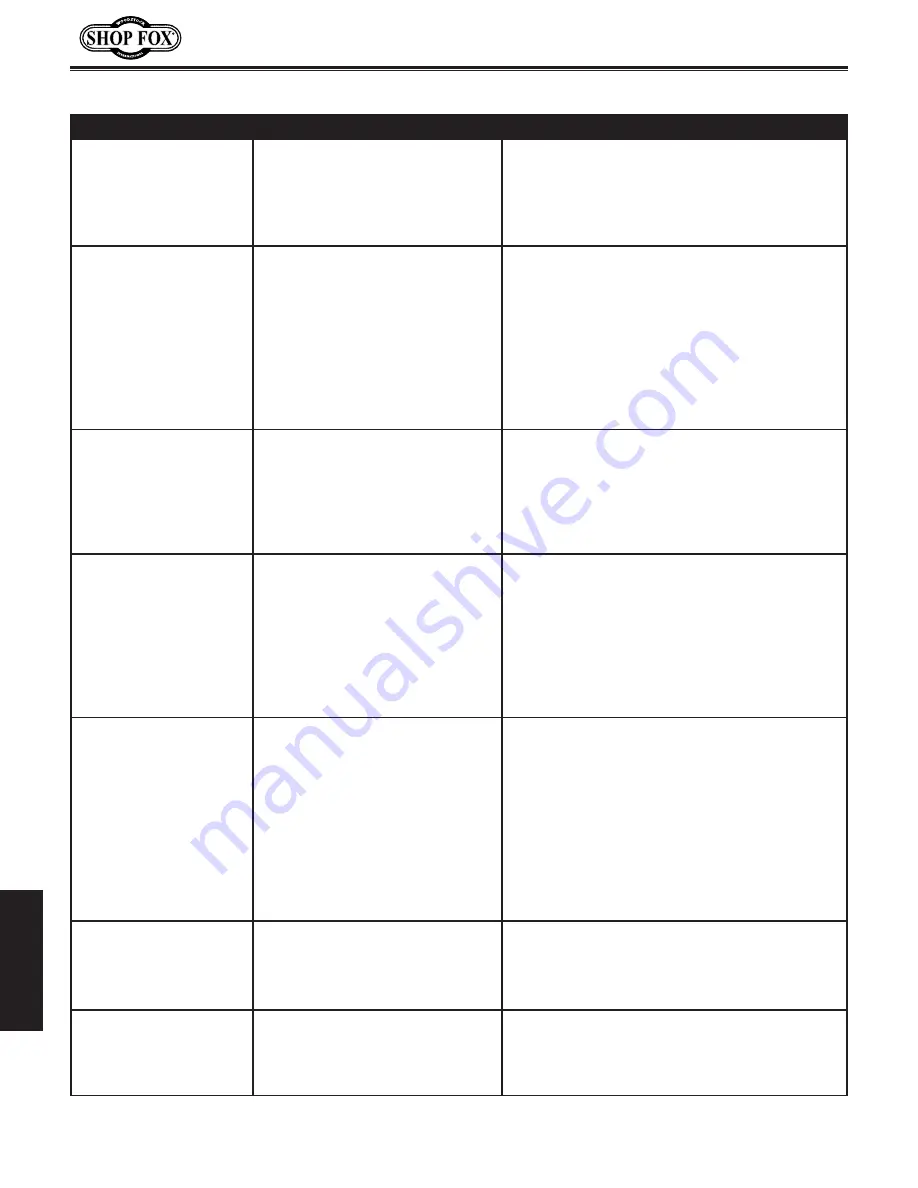
-36-
Model M1116 (For Machines Mfd. Since 06/17)
SE
RV
IC
E
PROBLEM
POSSIBLE.CAUSE
CORRECTIVE.ACTION
Tool loose in spindle.
1. Cutting tool not fully drawn up
into spindle taper.
2. Debris on cutting tool or in spin-
dle taper.
3. Taking too big of cut.
1. Tighten drawbar (do not overtighten) (
Page 25).
2. Clean collet and spindle taper.
3. Lessen depth of cut and allow chips to clear.
Breaking tools or cutters.
1. Spindle speed/feed rate too fast
for depth of cut, cutting tool
size, or workpiece material.
2. Cutting tool too small.
3. Improper or no cutting lubricant/
cutting tool getting too hot.
4. Taking too big of a cut.
5. Spindle extended too far down.
1. Reduce spindle speed (
Page 26); reduce feed
rate; take lighter cut.
2. Use larger cutting tool and slower feed rate.
3. Use proper lubricant for operation.
4. Lessen depth of cut and allow chips to clear.
5. Fully retract spindle and lower headstock. This
increases rigidity.
Workpiece vibrates or
chatters during operation.
1. Table locks not tight.
2. Workpiece not secure.
3. Spindle speed/feed rate too fast.
4. Spindle extended too far down.
1. Tighten table locks (
Page 24).
2. Properly clamp workpiece on table or in vise.
3. Reduce spindle speed (
Page 26); reduce feed
rate.
4. Fully retract spindle and lower headstock. This
increases rigidity.
Table is hard to move.
1. Table locks tightened down.
2. Chips loaded up on ways.
3. Ways are dry and need
lubrication.
4. Table limit stops interfering.
5. Gibs too tight.
1. Release table locks (
Page 24).
2. Frequently clean away chips that load up during
milling operations.
3. Lubricate ways (
Page 29).
4. Adjust table limit stops out of the way
(
Page 24).
5. Adjust gibs (see
Page 32).
Bad surface finish.
1. Spindle speed/feed rate too fast.
2. Dull/incorrect cutting tool.
3. Wrong rotation direction of cut-
ting tool.
4. Workpiece not secure.
5. Spindle extended too far down
during or at beginning of
operation.
1. Reduce spindle speed (
Page 26); reduce feed
rate.
2. Sharpen/replace cutting tool; select better tool
for operation.
3. Check for proper direction of cutting tool
rotation.
4. Properly clamp workpiece on table or in vise.
5. Fully retract spindle and lower headstock. This
increases rigidity.
DRO doesn't give reading.
1. DRO not turned on.
2. Battery dead.
3. Shorted/disconnected wiring/
plugs.
1. Press DRO ON/Power button (
Page 22).
2. Replace battery (
Page 31).
3. Inspect circuit boards, sensors, plugs, and wiring
connections. Replace/repair as necessary.
DRO reading is incorrect.
1. Initial reading incorrect.
2. Sensor has gone bad.
3. Spacing between sensor and scale
incorrect.
1. Zero/Reset DRO at beginning point (
Page 22).
2. Test/replace sensor as necessary.
3. Adjust spacing between sensor and scale.
Operation