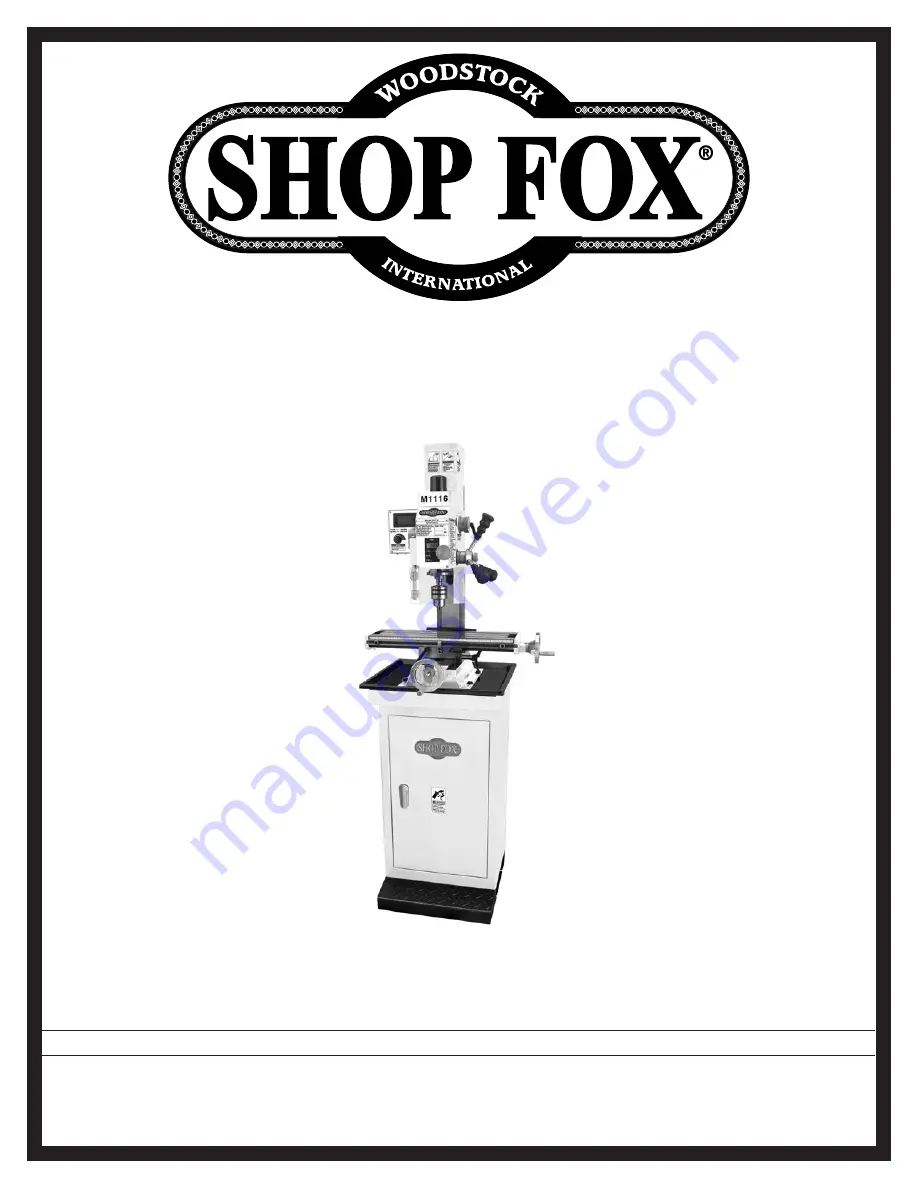
OWNER'S MANUAL
(FOR MODELS MANUFACTURED SINCE 06/17)
MODEL M1116
MILL-DRILL w/DRO
Phone: (360) 734-3482 • Online Technical Support: [email protected]
COPYRIGHT © SEPTEMBER, 2017 BY WOODSTOCK INTERNATIONAL, INC.
WARNING: NO PORTION OF THIS MANUAL MAY BE REPRODUCED IN ANY SHAPE OR FORM WITHOUT
THE WRITTEN APPROVAL OF WOODSTOCK INTERNATIONAL, INC.
#19003KB Printed in China
Shown with Optional D4780 Stand