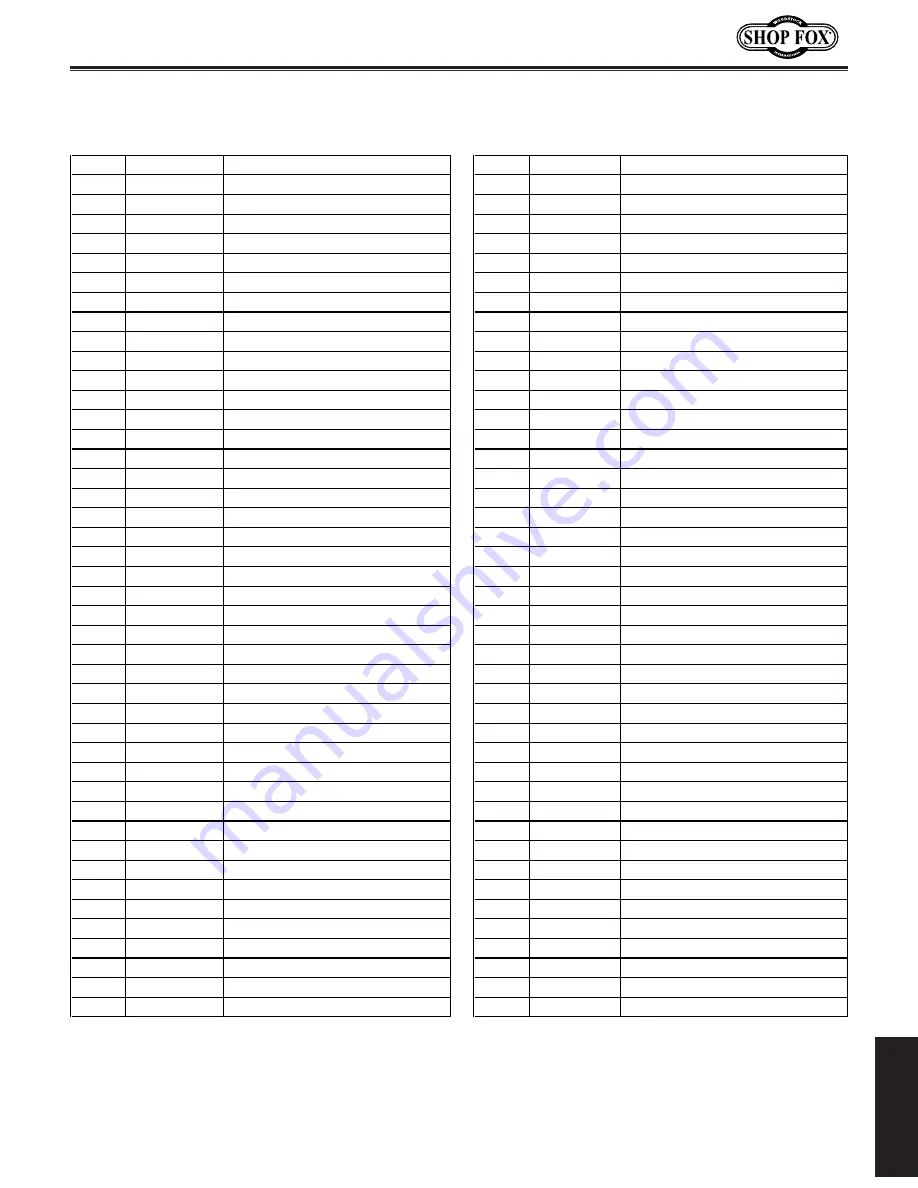
-35-
M1048 10" x 18" Metal Cutting Bandsaw
PA
RT
S
Blade Guides Parts List
REF
PART
�
#
DESCRIPTION
REF
PART
�
#
DESCRIPTION
101
XM1048101
SLIDE
�
SET
157
XM1048157
PLASTIC
�
BUSHING
101-1
XM1048101-1 SLIDE
158
XPSB04M
CAP
�
SCREW
�
M6-1
�
X
�
10
101-2
XM1048101-2 SPECIAL
�
SET
�
SCREW
159
XPLW02
LOCK
�
WASHER
�
1/4
101-3
XPN10
HEX
�
NUT
�
7/16-20
160
XM1048160
HEX
�
NUT
�
M8
101-4
XPW04M
FLAT
�
WASHER
�
10MM
161
XPLW01
LOCK
�
WASHER
�
5/16
101-5
XPSB134M
CAP
�
SCREW
�
M10-1.5
�
X
�
65
163
XM1048163
BLADE
�
GUARD
101-6
XM1048101-6 DISC
�
SPRING
164
XM1048164
BLADE
�
LABEL
101-7
XM1048101-7 INDICATOR
�
DIAL
167
XPLW02
LOCK
�
WASHER
�
1/4
101-8
XM1048101-8 BEARING
�
51204
168
XPSB04M
CAP
�
SCREW
�
M6-1
�
X
�
10
101-9
XPW01
FLAT
�
WASHER
�
1/2
169
XM1048169
SCALE
101-10 XM1048101-10 SPECIAL
�
SCREW
170
XM1048170
RIVET
101-11 XM1048101-11 SCALE
171
XPSB77M
CAP
�
SCREW
�
M12-1.75
�
X
�
30
101-12 XPS05M
PHLP
�
HD
�
SCR
�
M5-.8
�
x
�
8
172
XPSS09M
SET
�
SCREW
�
M8-1.25
�
X
�
20
101-13 XPB32M
HEX
�
BOLT
�
M10-1.5
�
x
�
25
173
XM1048173
COLUMN
101-14 XPLW06M
LOCK
�
WASHER
�
10MM
174
XPSB84M
CAP
�
SCREW
�
M10-1.5
�
X
�
35
101-15 XM1048101-15 GIB
175
XPW04M
FLAT
�
WASHER
�
10MM
101-16 XM1048101-16 BRACKET
176
XPRP49M
ROLL
�
PIN
�
5
�
X
�
25
102
XPRP49M
ROLL
�
PIN
�
5
�
X
�
25
177
XM1048177
LEFT
�
COLUMN
�
SUPPORT
103
XM1048103
COLLAR
178
XPSB05M
CAP
�
SCREW
�
M8-1.25
�
X
�
50
104
XM1048104
LEADSCREW
179
XPLW04M
LOCK
�
WASHER
�
8MM
105
XPK20M
KEY
�
5
�
X
�
5
�
X
�
15
180
XPLW01
LOCK
�
WASHER
�
5/16
106
XM1048106
HANDWHEEL
�
&
�
HANDLE
181
XM1048181
SUPPORT
�
SEAT
107
XM1048107
COMPRESSION
�
SPRING
182
XM1048182
ADJ
�
FIXING
�
PLATE
�
(IDLER)
108
XPRP30M
ROLL
�
PIN
�
5
�
X
�
50
183
XPLW02
LOCK
�
WASHER
�
1/4
109
XM1048109
BRACKET
184
XPSB02M
CAP
�
SCREW
�
M6-1
�
X
�
20
110
XM1048110
SHAFT
185
XPN03M
HEX
�
NUT
�
M8-1.25
141
XPSB72M
CAP
�
SCREW
�
M10-1.5
�
X
�
30
186
XPSS09M
SET
�
SCREW
�
M8-1.25
�
X
�
20
142
XPLW06M
LOCK
�
WASHER
�
10MM
187
XM1048187
BLADE
�
ADJUSTABLE
�
KNOB
143
XM1048143
IDLER
�
WHEEL
�
BOX
188
XPW04M
FLAT
�
WASHER
�
10MM
144
XPSB130M
CAP
�
SCREW
�
M10-1.5
�
X
�
16
189
XM1048189
ARM
�
(LEFT)
145
XM1048145
TENSION
�
LABEL
190
XM1048190
GIB
146
XM1048146
RIVET
191
XM1048191
HOSE
�
CLAMP
147
XPS68M
PHLP
�
HD
�
SCR
�
M6-1
�
X
�
10
192
XPS05M
PHLP
�
HD
�
SCR
�
M5-.8
�
X
�
8
148
XM1048148
BRACKET
193
XM1048193
ARM
�
(RIGHT)
149
XPSB77M
CAP
�
SCREW
�
M12-1.75
�
X
�
30
194
XPW04M
FLAT
�
WASHER
�
10MM
150
XPSB06M
CAP
�
SCREW
�
M6-1
�
X
�
25
195
XPSB71M
CAP
�
SCREW
�
M10-1.5
�
X
�
60
151
XM1048151
BUSHING
200
XM1048200
BEARING
�
SPACER
152
XM1048152
IDLER
�
WHEEL
�
ASSY
203
XM1048203
BEARING
�
BRACKET
�
(IDLER)
152-3
XPB70M
HEX
�
BOLT
�
M10-1.5
�
X
�
16
204
XPSS20M
SET
�
SCREW
�
M8-1.25
�
X
�
8
152-4
XPW04M
FLAT
�
WASHER
�
10MM
205
XM1048205
CARBIDE
�
GUIDE
153
XPSB11M
CAP
�
SCREW
�
M8-1.25
�
X
�
16
206
XPSB02M
CAP
�
SCREW
�
M6-1
�
X
�
20
154
XM1048154
HANDLE
207
XM1048207
ECCENTRIC
�
SHAFT
�
SET
155
XM1048155
SPEED
�
INDICATOR
�
LABEL
208
XM1048208
BEARING
�
SHAFT
�
ASSY
156
XM1048156
IDLER
�
WHEEL
�
COVER
209
XM1048209
MICRO
�
CONTROL
�
BLOCK
Summary of Contents for M1048
Page 2: ......
Page 36: ...34 M1048 10 x 18 Metal Cutting Bandsaw PARTS Blade Guides Parts Breakdown...
Page 38: ...36 M1048 10 x 18 Metal Cutting Bandsaw PARTS Drive Wheel Parts Breakdown...
Page 40: ...38 M1048 10 x 18 Metal Cutting Bandsaw PARTS Main Parts Breakdown...
Page 47: ......
Page 48: ......