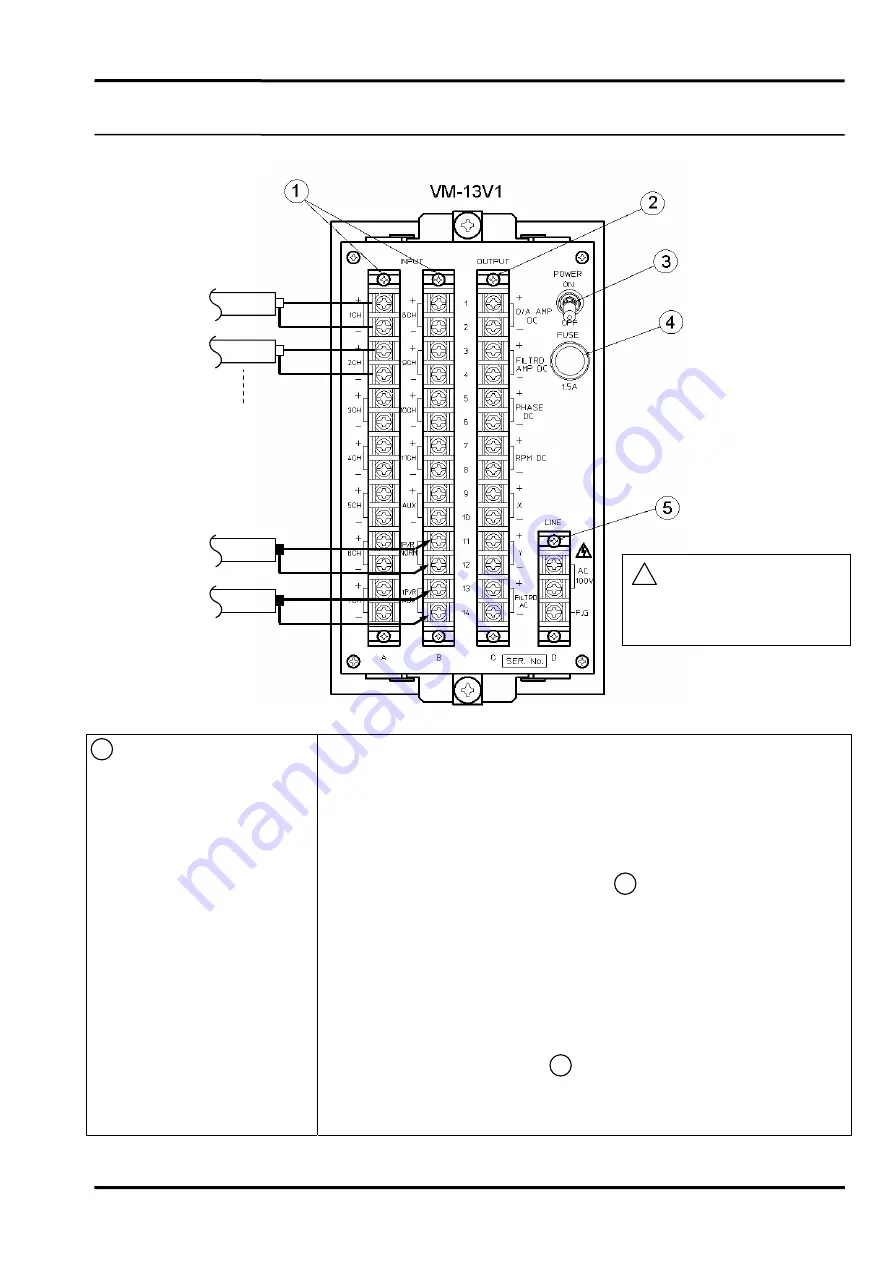
4.
DESCRIPTION OF EACH SECTION
VM-13V1
-9-
4-2 REAR PANEL
1 Signal Input Terminal Block
MEAS. 1ch to 11ch, AUX :
Input terminals for up to 11 separate vibration signals and one auxiliary
vibration
signal.
•
Connect vibration signals from vibration transducer or vibration
monitor (VM Series) “MONITOR” output.
•
AUX terminals is parallel connection to the front panel AUX
Vibration Input Connrctor. (See 4.1 15 on page 8.)
•
Connect signal common to COM treminal indepemdently for each
channel.
1P/R, NORM, AUX : Input terminal for one (normal) reference signal and
one auxiliary refernce signal.
•
Connect 1P/R signals from phase marker transducer or Phase Marker
(VM-5P) “MONITOR” output.
•
AUX terminlas is parallel connector to the front panel AUX Trigger
Input Connector. (See 4.1 13 on page 8.)
•
Connect signal common to COM terminal independently for each
channel.
VIBRATION SIGNAL INPUTS
1CH
2CH
NORMA
(AUX)
11CH
(AUX)
!
WARNING
Beware of electric shock
from high-voltage parts.
REFERENCE SIGNAL INPUTS