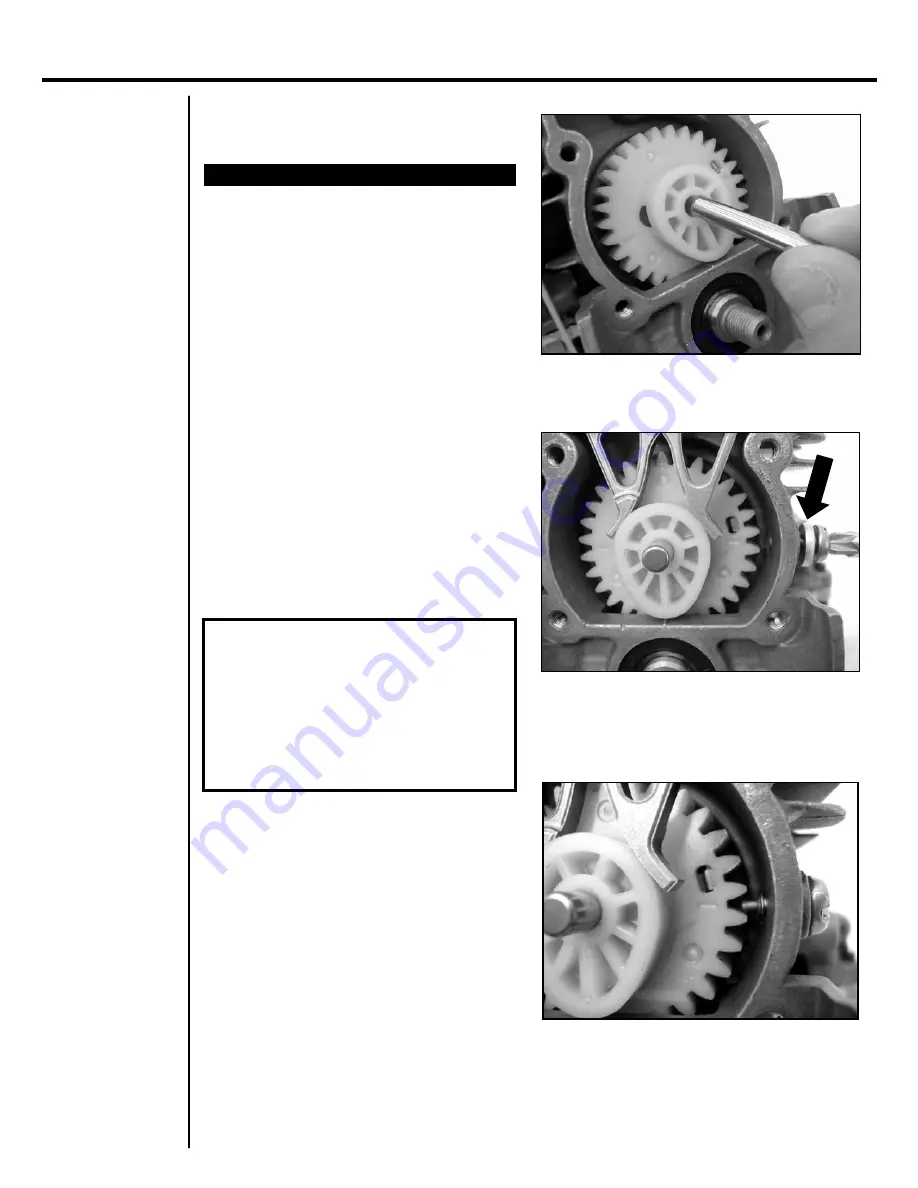
F. Install Cam Followers
Reverse steps above to in stall followers.
Install left-hand (intake valve) follower first.
G. Remove Cam Gear
STEP 1.
Remove pushrods and followers.
STEP 2.
Remove cam axle pin.
STEP 3.
Lift cam gear out of cam
compartment.
H. Install Cam Gear
STEP 1.
Rotate crankshaft so that piston is
situated at top-dead-center (TDC).
STEP 2.
Place cam gear in cam compartment,
with narrow, lobe-end pointing down. Make
sure that lobe's center rib aligns with ridge
on cylinder casting and that horizontal marks
on face of cam align with tip of timing screw
on right side of cam compartment.
STEP 3.
Align cam center hole with journal in
cylinder casting and insert axle pin.
STEP 4.
Replace cam followers and pushrods.
STEP 5.
Replace cam cover and rocker arm
cover. Be sure to use new gaskets.
NOTE:
Timing screw on right side of cam compartment
can be used to maintain proper cam alignment
during reassembly. To use, (1) remove muffler
to gain access. (2) Back out timing screw and
remove spacer washer. (3) Set cam in proper
alignment and reinstall screw. Tip of screw
should mesh with marked notch on cam gear.
(4) Complete engine assembly. (5) Remove
timing screw, install original washer and
reinstall with thread-locking compound.
Always
use the correct washer (P/N 15401-10028) or
damage to cam gear may result!
Servicing Pushrods/Followers/Cam
Section
5
12
Removing &
Installing
Cam Gear
IMPORTANT!
Servicing Pushrods/Followers/Cam
Section
5
CAUTION!
Be certain that the cam gear is
installed
correctly,
with
piston
at TDC and cam timing marks aligned
exactly. Failure to do so will result in
incorrect valve timing and an engine that
either will not run or that runs erratically.
!
When installing cam gear, place piston at TDC,
and insert cam with lobe down using timing
marks to assure proper alignment. Insert pin.
Timing screw can be used to preserve cam
position during reassembly. To use, remove
screw and reinstall without spacer washer
(arrow). Screw tip should mesh with marked
notch on cam gear.
Tip of timing screw should engage cam gear at
marked notch. It prevents changes in cam
position during reassembly. DON'T FORGET
TO REMOVE SCREW, REPLACE SPACER
WASHER AND ADD SEALANT AFTER
REASSEMBLY!
Locking Cam
Position With
Timing Screw
Edition 2• 09/2007