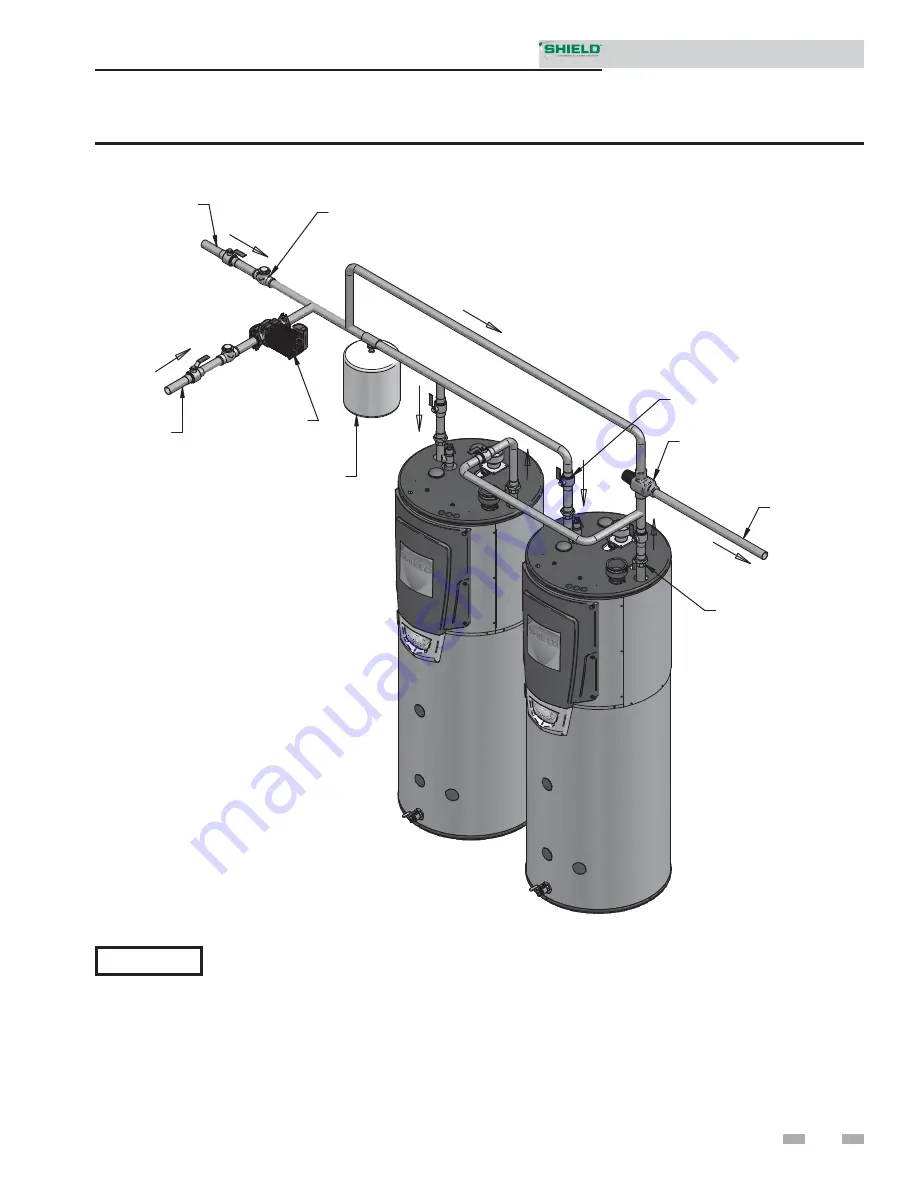
37
5
System piping
(continued)
EXPANSION
TANK
BUILDING
RETURN
SYSTEM
CIRCULATOR
COLD WATER
SUPPLY
FLOW CHECK VALVE
(TYPICAL)
BALL VALVE
(TYPICAL)
UNION
(TYPICAL)
HOT WATER
SUPPLY
MIXING VALVE
(IF REQUIRED)
IMG00473
Figure 5-3 Multiple Units
Installation & Service Manual
Please note that these illustrations are meant to show system piping concept only, the installer is responsible
for all equipment and detailing required by local codes.
NOTICE
Summary of Contents for SNA151-100
Page 74: ...74 Notes ...
Page 75: ...75 Notes ...