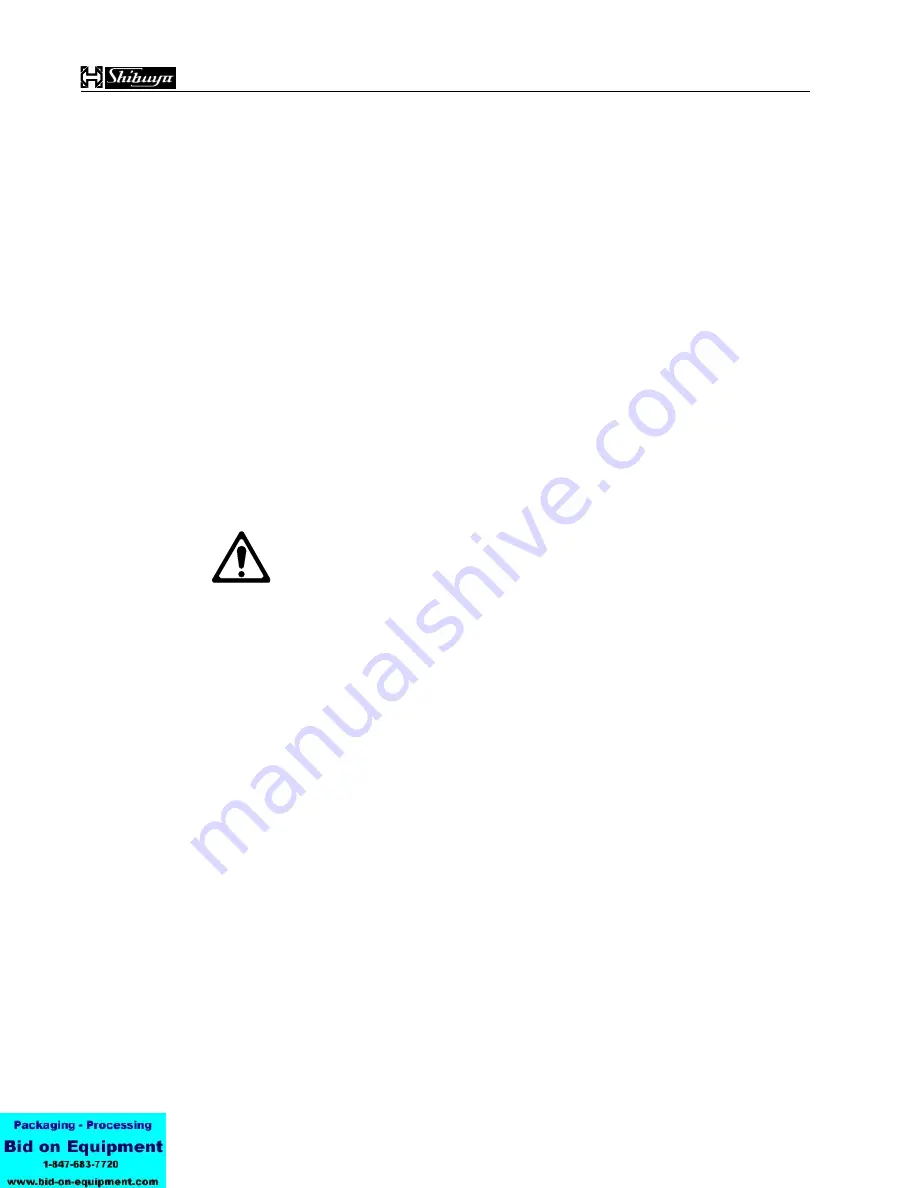
12
FR-20 & FR-30 Feeder Installation/Maintenance
DonÕt Adjust Air Jet Flow Controls.
It’s okay to adjust the main air
regulator to its correct setting for your installation. However, air
jets and their
individual flow controls
have all been carefully preset
to work with your product; they should
never
need adjustment. If
you move air jets or adjust their individual flow controls, the
feeder may jam or lose rate.
Do Perform Preventive Maintenance.
To keep the feeder running
without unexpected repairs and resulting “down” time, regularly
perform the preventive maintenance procedures in Chapter 4.
Do Carefully Replace Any Tooling You Remove.
To gain access
for repairs, you may need to remove tooling. Because Shibuya
Hoppmann and your dealer or OEM have no control over such
activities, they can not be responsible for any tooling you remove.
Carefully document the position of any tooling before you begin.
If you fail to replace all tooling exactly as it was, you may create
difficult and time consuming problems for yourself.
Don't Install the Feeder Near Flammable Gas, Vapor or Dust.
Do
not instal a feeder in these conditions unless you install additional,
approved explosion-proof or dust ignition-proof enclosures.
Without such additional enclosures, normal sparking of the brushes
inside the motor could ignite flammable gas, vapor or dust.