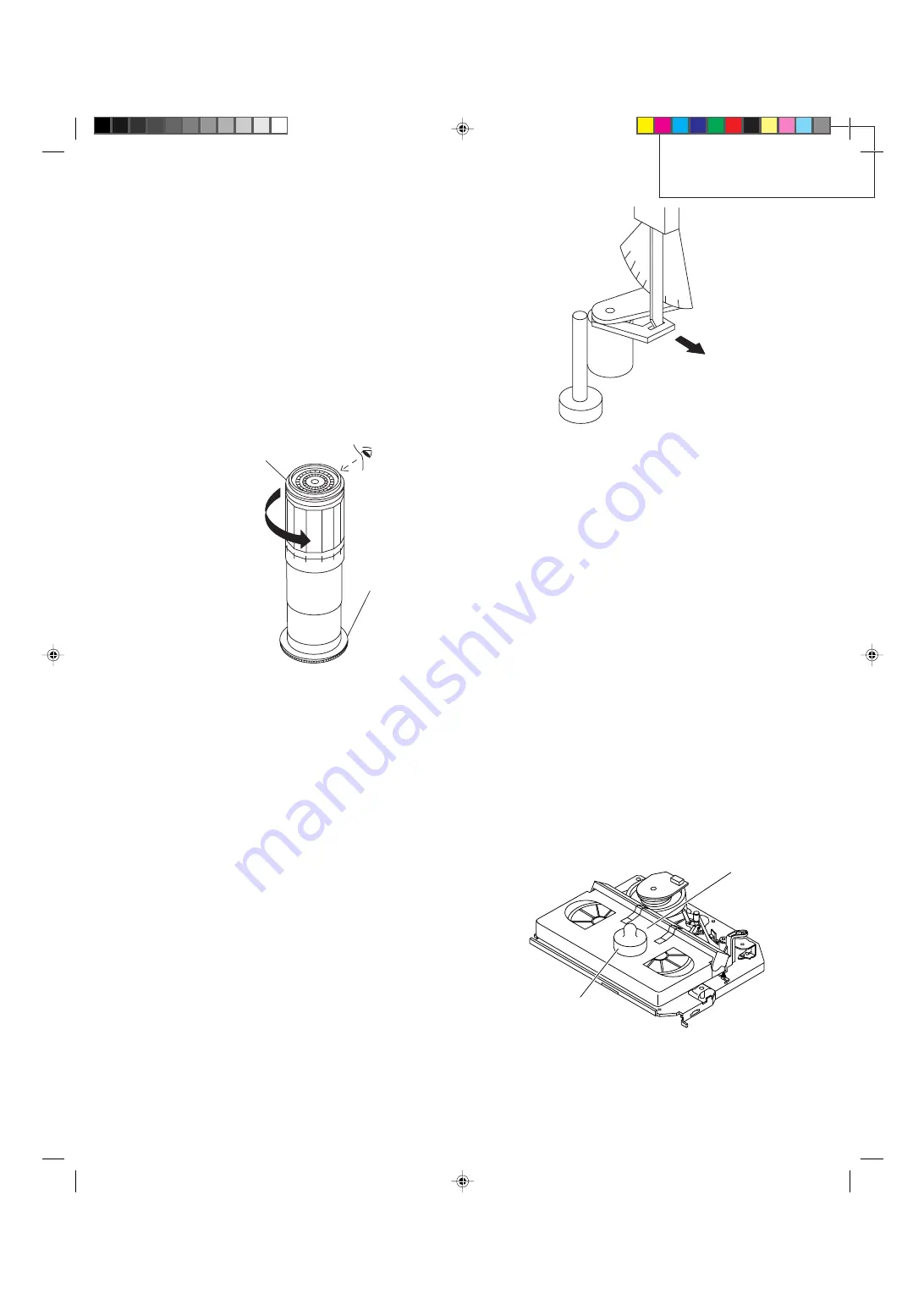
15
VC-TA350/TA351/351W
VC-TA352W/TA355/TA356
Figure 4-13.
1. Detach the pinch roller from the capstan shaft.
Do not separate excessively. Or the pinch lever and
pinch double action lever may disengage.
2. Engage the tension gauge adapter with the pinch roller
shaft, and pull in the arrow direction.
3. Gradually return the pinch roller, and measure the
pulling force when the pinch roller contacts the capstan
shaft.
4. Make sure that the measured value is within setting 8.8
to 11.8 N (900 to 1,200gf).
CHECKING AND ADJUSTMENT OF TENSION
POLE POSITION
•
Remove the cassette housing control assembly.
•
After short-circuiting TP801 provided at the center
(facing to the main PWB), plug in the power cord.
•
Setting
1. Turn off the power switch.
2. Open the cassette tape (E-180), and fix with tape.
3. Set the cassette tape in loading state.
4. Put the weight (500g) on the cassette tape.
5. Turn on the power switch.
6. Make the adjustment with the beginning of a E-180 tape.
CHECKING THE VIDEO SEARCH REWIND
BACK TENSION
• Remove the cassette housing control assembly.
• After short-circuiting TP801 provided at the center
(facing to the main PWB), plug in the power cord.
• Checking
1. After pressing the play button, press the rewind button,
and set the video search rewind mode.
2. Place the torque gauge on the take-up reel disk, and turn
it counterclockwise very slowly (one rotation every 2 to
3 seconds) and check that the torque is within the set
value 3.4
±
1.5mN
⋅
m (35
±
15gf
⋅
cm).
Pinch roller
Tension gauge
8.8 ~ 11.8 N
(900 - 1,200gf)
Capstan shaft
Tension gauge adapter
Figure 4-12.
Torque gauge
Take-up reel disk
Notes:
Set the torque gauge securely on the take-up reel disk.
If it is not secure, the measurement will be incorrect.
CHECKING THE PINCH ROLLER PRESSURE
•
Remove the cassette housing control assembly.
•
After short-circuiting TP801 provided at the center
(facing to the main PWB), plug in the power cord.
•
Checking
Press the play button to set the playback mode.
CCW
Figure 4-14.
500g
(E-180)
Weight to prevent
float (500g)
• Checking
1. Set a cassette tape, push the REC button to place the
unit in the SP record mode. Now check the tension pole
position.