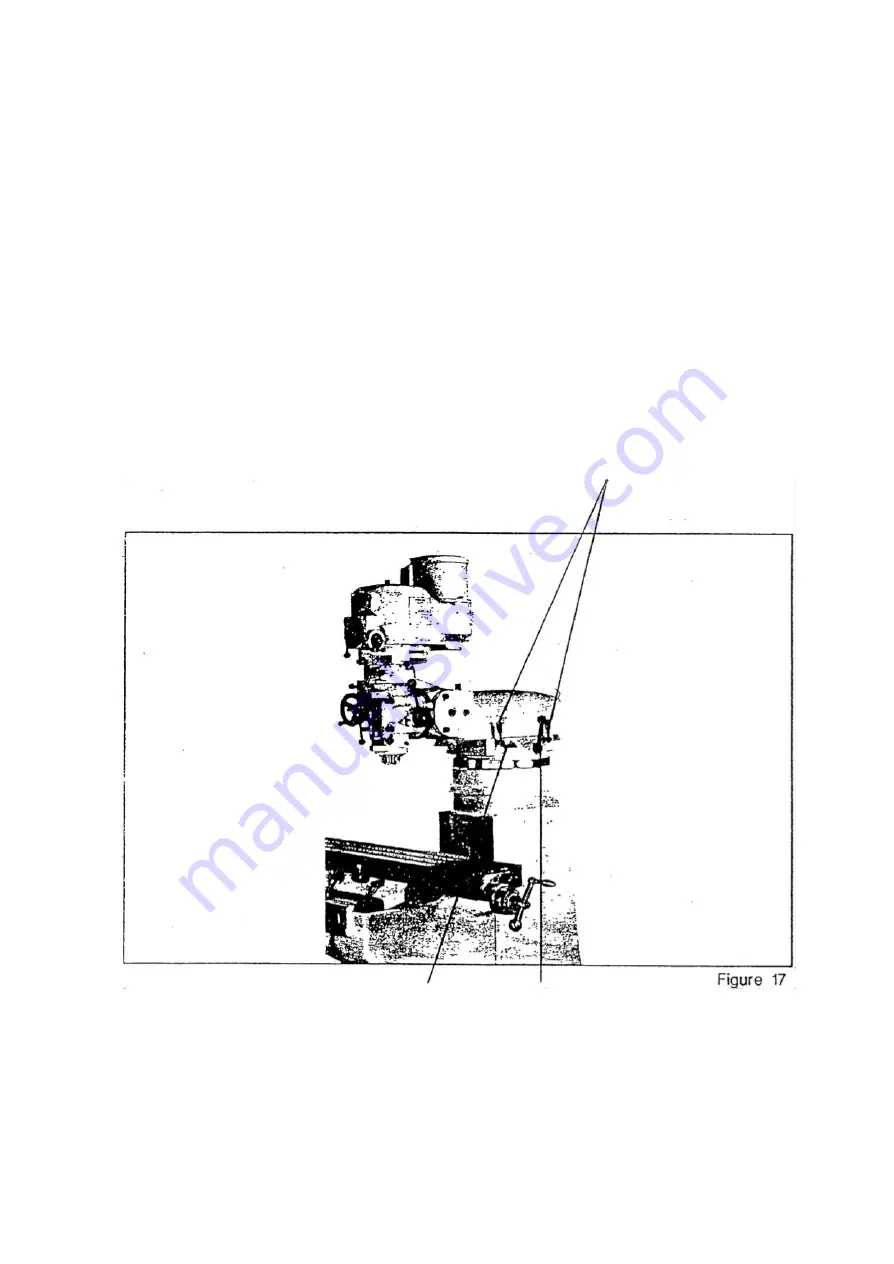
36
(C) Operations:
(a)
Ram Movement and
Swiveling:
1.
Ram
Movement:
a.
Loosen the two Ram lock levers
(A).
b.
Swivel the Ram pinion handle (B),
and the Ram can be moved.
c.
When it moves to the desired
position, lock up (A).
2. Ram Swiveling:
Loosen the four locking bolts (C), and force the cross arm to turn until the
desired angle is obtained. Lock up (C).
A
C
B
Summary of Contents for TMV Series
Page 1: ...Sharp Precision Machine Tools SERVICE AND PARTS MANUAL Vertical Mill TMV ...
Page 7: ...3 4 Headstock A Stepless Speed Headstock 195VS a Names of machine parts ...
Page 8: ...4 Emergency Stop Forward Reverse Switch Brake Speed Meter Speed Knob ...
Page 15: ...11 ...
Page 17: ...13 ...
Page 19: ...15 B Headstock 195TM a Names of machine parts ...
Page 22: ...18 5 PARTS REPLACEMENT a Names of machine parts Step speed Headstock TMV 185TM ...
Page 23: ...19 Emergency Stop Forward Reverse Switch Brake Speed Meter Speed Knob ...
Page 31: ...27 ...
Page 33: ...29 ...
Page 36: ...32 5 Machine Body A Names of machine parts a Column Turret and Ram 185 TM VS ...
Page 37: ...33 b Column Turret and Ram 195 TM VS ...
Page 38: ...34 c Work Table Saddle and Knee TMV 185 LC 195 ...
Page 53: ...49 ...
Page 55: ...51 PARTS LIST ...
Page 58: ...54 DVS HEAD PARTS 1 ...
Page 60: ...56 DVS HEAD PARTS 2 ...
Page 62: ...58 ...
Page 67: ...63 ...
Page 69: ...65 ...
Page 72: ...68 ...
Page 76: ...72 ...
Page 78: ...74 ...
Page 80: ...76 ...
Page 82: ...78 ...
Page 84: ...80 ...
Page 86: ...82 ...
Page 88: ...84 ...
Page 90: ...86 ...
Page 92: ...88 ...
Page 94: ...90 ...
Page 97: ...93 ...
Page 98: ...94 ...
Page 99: ...95 ...
Page 101: ...97 ...
Page 103: ...99 ...
Page 105: ...101 ...