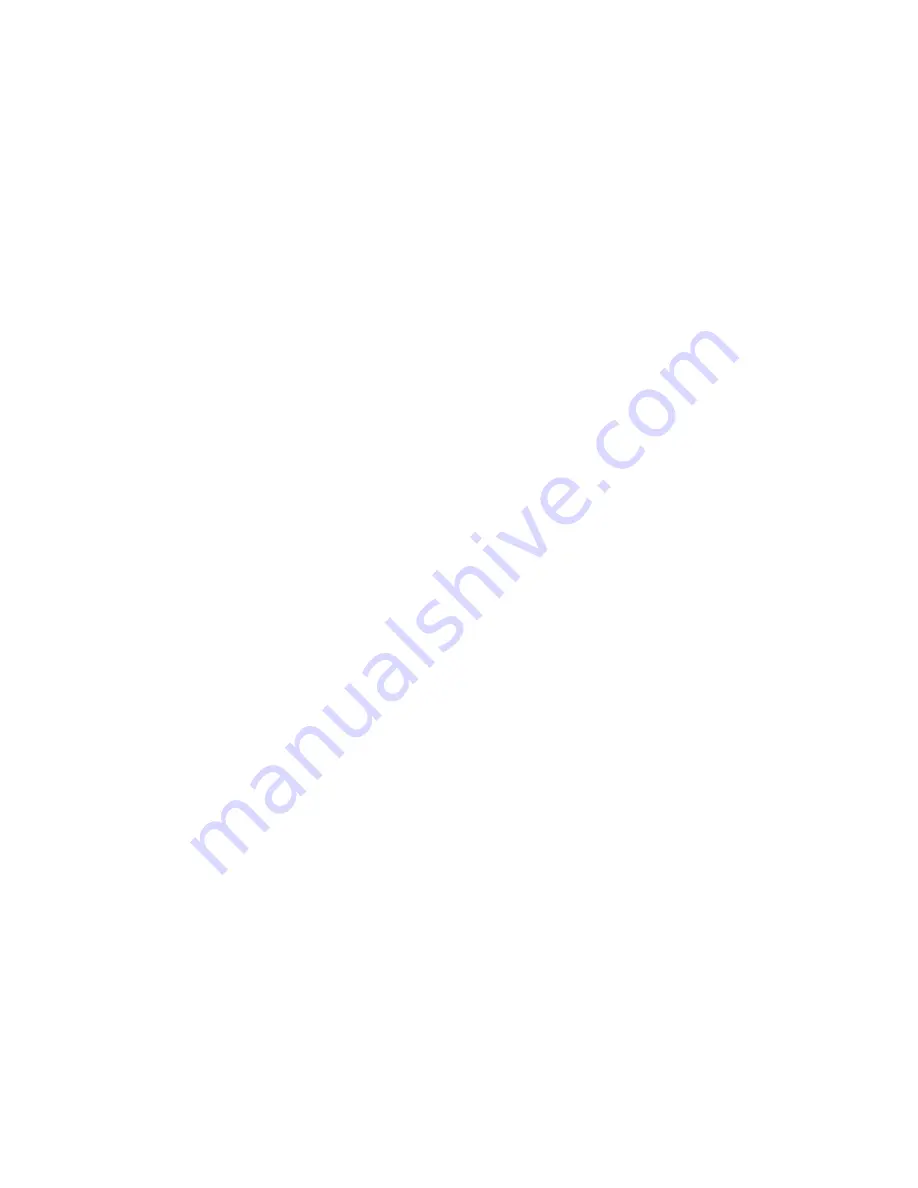
R426LS
2 – 1
R426LS
Service Manual
CHAPTER 2.
MICROWAVE MEASUREMENT PROCEDURE
[1] Requirements:
1. Microwave leakage limit (Power density limit): The power density of microwave radiation emitted by a microwave oven should not exceed 1mW/
cm
2
at any point 5cm or more from the external surface of the oven, measured prior to acquisition by a purchaser, and thereafter (through the use-
ful life of the oven), 5 mW/cm
2
at any point 5cm or more from the external surface of the oven.
2. Safety interlock switches:
Primary interlock switch shall prevent microwave radiation emission in excess of the requirement as above mentioned. Secondary interlock relay
and door sensing switch shall prevent microwave radiation emission in excess of 5 mW/cm
2
at any point 5cm or more from the external surface of
the oven.
[2] Preparation for testing:
Before beginning the actual measurement of leakage, proceed as follows:
1. Make sure that the actual instrument is operating normally as specified in its instruction booklet.
Important:
Survey instruments that comply with the requirement for instrumentation as prescribed by the performance standard for microwave ovens, 21 CFR
1030.10(c)(3)(i), must be used for testing.
2. Place the oven tray in the oven cavity.
3. Place the load of 275
±
5 ml (9.8 oz) of tap water initially at 20
±
5
°
C (68
°
F) in the center of the oven cavity.
The water container shall be a low form of 600 ml (20 oz) beaker with an inside diameter of approx. 8.5 cm (3-1/2 in.) and made of an electrically
nonconductive material such as glass or plastic.
The placing of this standard load in the oven is important not only to protect the oven, but also to insure that any leakage is measured accurately.
4. Set the cooking control on Full Power Cooking Mode
5. Close the door and select a cook cycle of several minutes. If the water begins to boil before the survey is completed, replace it with 275 ml of cool
water.
[3] Leakage test:
Closed-door leakage test (microwave measurement)
1. Grasp the probe of the survey instrument and hold it perpendicular to the gap between the door and the body of the oven.
2. Move the probe slowly, not faster than 1 in./sec. (2.5 cm/sec.) along the gap, watching for the maximum indication on the meter.
3. Check for leakage at the door screen, sheet metal seams and other accessible positions where the continuity of the metal has been breached (eg.,
around the switches, indicator, and vents).
While testing for leakage around the door pull the door away from the front of the oven as far as is permitted by the closed latch assembly.
4. Measure carefully at the point of highest leakage and make sure that the highest leakage is no greater than 4mW/cm
2
, and that the secondary
interlock relay and the primary interlock switch do turn the oven OFF before any door movement.
NOTE:
After servicing, record data on service invoice and microwave leakage report.