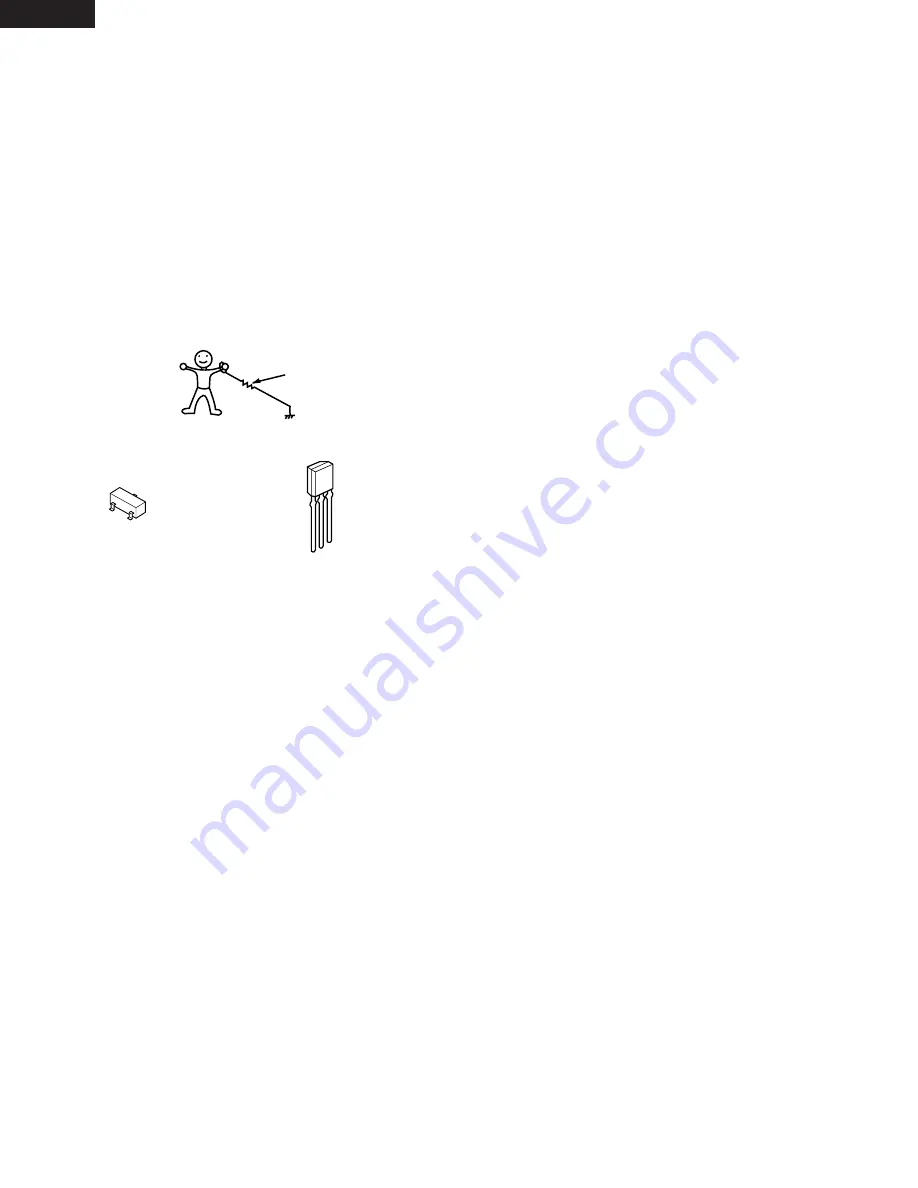
10
R-21JCA
1. Precautions for Handling Electronic Components
This unit uses CMOS LSI in the integral part of the
circuits. When handling these parts, the following
precautions should be strictly followed. CMOS LSI have
extremely high impedance at its input and output
terminals. For this reason, it is easily influenced by the
surrounding high voltage power source, static electricity
charge in clothes, etc., and sometimes it is not fully
protected by the built-in protection circuit.
In order to protect CMOS LSI.
1) When storing and transporting, thoroughly wrap them
in aluminium foil. Also wrap PW boards containing
them in aluminium foil.
2) When soldering, ground the technician as shown in
the figure and use grounded soldering iron and work
table.
2. Shapes of Electronic Components
3. Servicing of Touch Control Panel
We describe the procedures to permit servicing of the
touch control panel of the microwave oven and the
precautions you must take when doing so. To perform
the servicing, power to the touch control panel is available
either from the power line of the oven itself or from an
external power source.
(1) Servicing the touch control panel with power supply
of the oven :
CAUTION:
THE HIGH VOLTAGE TRANSFORMER OF THE MI-
CROWAVE OVEN IS STILL LIVE DURING SERVIC-
ING AND PRESENTS A HAZARD .
Therefore, before checking the performance of the touch
control panel,
1) Disconnect the power supply cord and then remove
outer case.
2) Open the door and block it open.
3) Discharge high voltage capacitor.
4) Disconnect the leads to the primary of the power
transformer.
5) Ensure that these leads remain isolated from other
components and oven chassis by using insulation
tape.
6) After that procedure, re-connect the power supply
cord.
After checking the performance of the touch control
panel,
1) Disconnect the power supply cord.
2) Open the door and block it open.
3) Re-connect the leads to the primary of the power
transformer.
4) Re-install the outer case (cabinet).
SERVICING
5) Re-connect the power supply cord after the outer
case is installed.
6) Run the oven and check all functions.
A. On some models, the power supply cord between the
touch control panel and the oven itself is so short that the
two can't be separated. For those models, check and
repair all the controls (sensor-related ones included) of
the touch control panel while keeping it connected to the
oven.
B. On some models, the power supply cord between the
touch control panel and the oven proper is so long
enough that they may be separated from each other. For
those models, therefore, it is possible to check and repair
the controls of the touch control panel while keeping it
apart from the oven proper; in this case you must short
both ends of the door sensing switch (on PWB) of the
touch control panel with a jumper, which brings about an
operational state that is equivalent to the oven door
being closed. As for the sensor-related controls of the
touch control panel, checking them is possible if the
dummy resistor(s) with resistance equal to that of the
controls are used.
(2) Servicing the touch control panel with power supply
from an external power source:
Disconnect the touch control panel completely from the
oven proper, and short both ends of the door sensing
switch (on PWB) of the touch control panel, which brings
about an operational state that is equivalent to the oven
door being closed. Connect an external power source to
the power input terminal of the touch control panel, then
it is possible to check and repair the controls of the touch
control panel; it is also possible to check the sensor-
related controls of the touch control panel by using the
dummy resistor(s).
4. Servicing Tools
Tools required to service the touch control panel
assembly.
1) Soldering iron: 30W
(It is recommended to use a soldering iron with a
grounding terminal.)
2) Oscilloscope: Single beam, frequency range: DC -
10MHz type or more advanced model.
3) Others: Hand tools
5. Other Precautions
1) Before turning on the power source of the control unit,
remove the aluminium foil applied for preventing
static electricity.
2) Connect the connector of the key unit to the control
unit being sure that the lead wires are not twisted.
3) After aluminium foil is removed, be careful that
abnormal voltage due to static electricity etc. is not
applied to the input or output terminals.
4) Attach connectors, electrolytic capacitors, etc. to
PWB, making sure that all connections are tight.
5) Be sure to use specified components where high
precision is required.
Transistor
KTC3198A
Transistor
KTA1504SGRRTK
KRC105S
KRA101S
KRC101S
approx. 1M ohm
E
C B
E
C
B
Summary of Contents for R21JCA - Commercial Microwave Oven
Page 23: ...21 R 21JCA ...