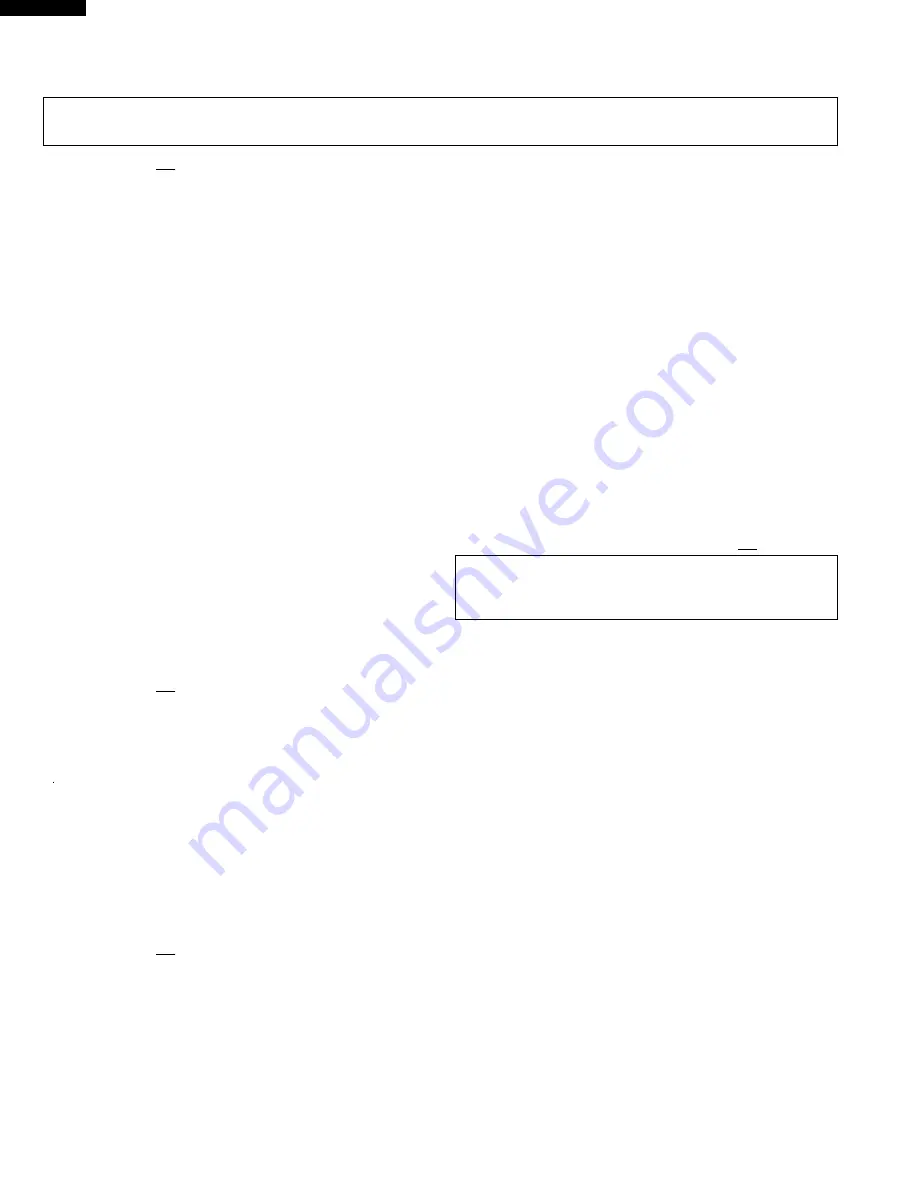
26
R-7H55
COMPONENT REPLACEMENT AND ADJUSTMENT PROCEDURE
WARNING: AVOID POSSIBLE EXPOSURE TO MICROWAVE ENERGY. PLEASE FOLLOW THE INSTRUCTIONS
BELOW BEFORE OPERATING THE OVEN.
1. Door does not close firmly.
2. Door hinge, support or latch hook is damaged.
3. The door gasket or seal or damaged.
4. The door is bent or warped.
5. There are defective parts in the door interlock system.
6. There are defective parts in the microwave generating
and transmission assembly.
7. There is visible damage to the oven.
Do not operate the oven:
1. Without the RF gasket (Magnetron).
2. If the wave guide or oven cavity are not intact.
3. If the door is not closed.
4. If the outer case (cabinet) is not fitted.
1. CARRY OUT 3D CHECKS.
2. Make sure that a definite” click” can be heard when the
microwave oven door is unlatched. (Hold the door in a
closed position with one hand, then push the door open
button with the other, this causes the latch leads to rise,
it is then possible to hear a “click’ as the door switches
operate.)
3. Visually check the door and cavity face plate for damage
(dents, cracks, signs of arcing etc.).
Carry out any remedial work that is necessary before
operating the oven.
Do not operate the oven if any of the following conditions
exist;
Please refer to "OVEN PARTS AND CABINET PARTS" AND "DOOR PARTS", when carrying out any of the following
removal procedures:
To remove the outer case, procedure as follows.
1. Disconnect oven from power supply.
2. Open the oven door and wedge it open.
3. Remove the screws from rear and along the side edge of
case.
4. Slide the entire case back out about 3 cm to free it from
retaining clips on the cavity face plate.
5. Lift the entire case from the oven.
OUTER CASE REMOVAL
6. Discharge the H.V. capacitor before carring out any
further work.
7. Do not operate the oven with the outer case removed.
N.B.; Step 1, 2 and 6 from the basis of the 3D checks.
MAGNETRON REMOVAL
1. CARRY OUT 3D CHECKS.
2. Disconnect filament lead of transformer from magnetron.
3. Disconnect high voltage wire lead from magnetron.
4. Remove two (2) screws holding the chassis support to
the oven cavity face plate and the rear cabinet.
5. Remove one (1) screw holding the chassis support to the
magnetron.
6. Carefully remove four (4) mounting screws hold the
magnetron to waveguide, when removing the screws
holding the magnetron to prevent it from falling.
7. Remove the magnetron from the unit with care so the
magnetron tube should not hit by any metal object
around the tube.
8. Remove one (1) screw holding the magnetron duct to the
magnetron.
9. Remove one (1) screw holding the magnetron guide to
the magnetron.
10.Now the magnetron is free.
CAUTION: WHEN REPLACING THE MAGNETRON, BE
SURE THE R.F. GASKET IS IN PLACE AND
THE MAGNETRON MOUNTING SCREWS
ARE TIGHTENED SECURELY.
2. Insert the two edges of the transformer into two metal
tabs of the base plate.
3. Make sure the transformer is mounted correctly to the
corners underneath those tabs.
4. After re-installing the transformer, secure the transformer
with two screws to the base plate.
5. Re-connect the wire leads (primary and high voltage)
and high voltage lead to the transformer and filament
leads of transformer to the magnetron and capacitor,
referring to the “Pictorial Diagram”.
6. Re-install the outer case and check that the oven is
operating properly.
POWER TRANSFORMER REMOVAL
1. CARRY OUT 3D CHECKS.
2. Disconnect filament leads of transformer from the
magnetron and capacitor.
3. Disconnect high voltage lead of capacitor from the
transformer.
4. Disconnect wire leads from the transformer.
5. Remove two (2) screws holding the transformer to the
base plate.
Re-install
1. Rest the transformer on the base plate with its primary
terminals toward rear cabinet.
CAUTION: DISCHARGE THE HIGH VOLYAGE CAPACI-
TOR BEFORE TOUCHING ANY OVEN COM-
PONENTS OR WIRING.
Summary of Contents for R-7H55
Page 2: ...R 7H55 ...