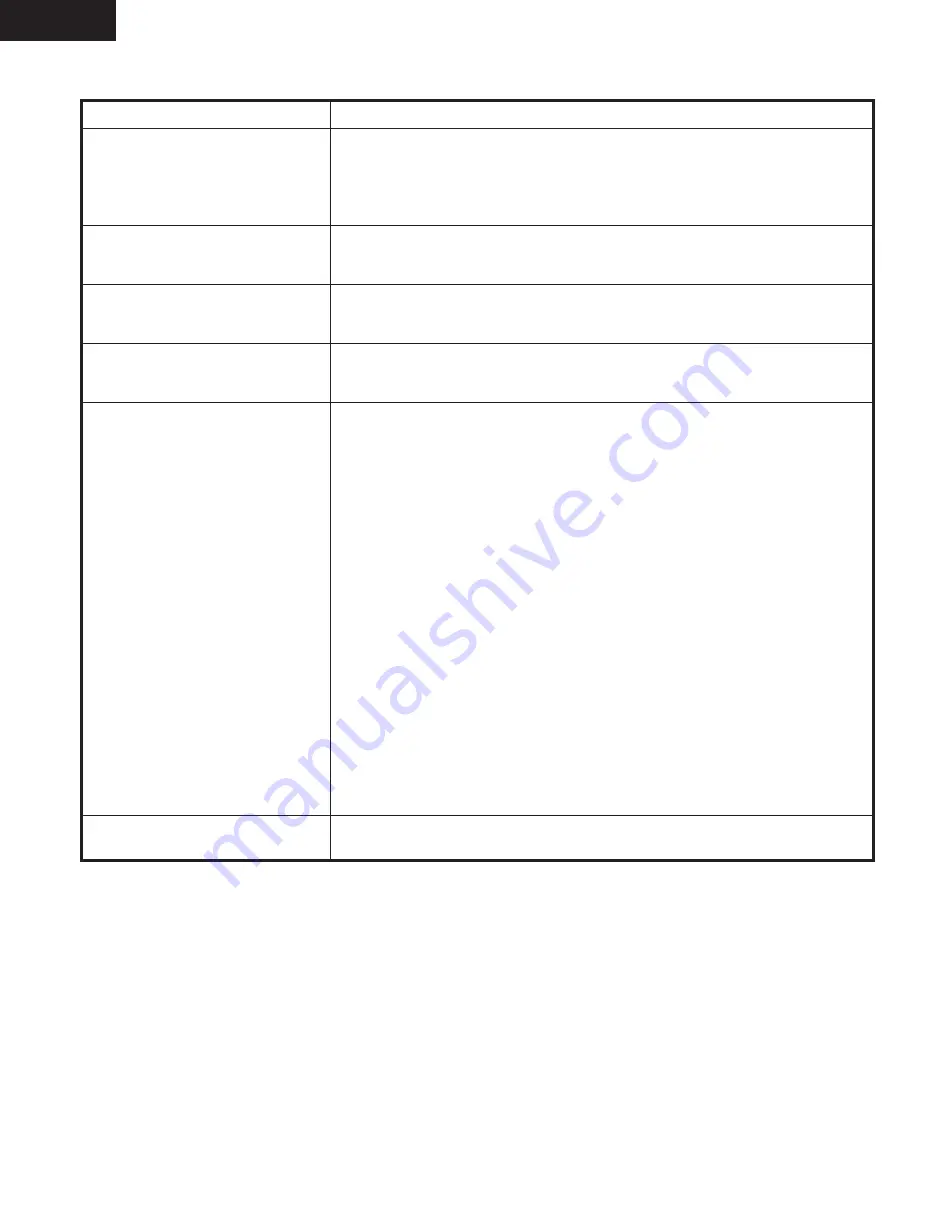
4
R - 5 2 0 J K
R - 5 2 0 J W
GENERAL INFORMATION
GROUNDING INSTRUCTIONS
This oven is equipped with a three prong grounding plug. It must be plugged into a wall receptacle that is properly installed
and grounded in accordance with the National Electrical Code and local codes and ordinances.
In the event of an electrical short circuit, grounding reduces the risk of electric shock by providing an escape wire for the electric
current.
WARNING:
Improper use of the grounding plug can result in a risk of electric shock.
Electrical Requirements
The electrical requirements are a 120 volt 60 Hz, AC only,
15 or 20 amp. fused electrical supply. It is recommended that a separate circuit serving only this appliance be provided. When
installing this appliance, observe all applicable codes and ordinances.
A short power-supply cord is provided to reduce risks of becoming entangled in or tripping over a longer cord.
Where a two-pronged wall-receptacle is encountered, it is the personal responsibility and obligation of the customer to contact
SPECIFICATION
ITEM
DESCRIPTION
Power Requirements
120 Volts
14.3 Amperes, 1700 watts
60 Hertz
Single phase, 3 wire grounded
Power Output
1200 watts (IEC 705 TEST PROCEDURE)
Operating frequency of 2450MHz
Case Dimensions
Width 24"
Height 13-3/8"
Depth 19-1/8"
Cooking Cavity Dimensions
Width 17-3/8"
Height 10-1/2"
2.0 Cubic Feet
Depth 18-5/8"
Control Complement
Touch Control System
Clock ( 1:00 - 12:59 )
Timer (0 - 99 min. 99 seconds)
Microwave Power for Variable Cooking
Repetition Rate;
P-HI .................................................. Full power throughout the cooking time
P-90 .................................................................... approx. 90% of Full Power
P-80 .................................................................... approx. 80% of Full Power
P-70 .................................................................... approx. 70% of Full Power
P-60 .................................................................... approx. 60% of Full Power
P-50 .................................................................... approx. 50% of Full Power
P-40 .................................................................... approx. 40% of Full Power
P-30 .................................................................... approx. 30% of Full Power
P-20 .................................................................... approx. 20% of Full Power
P-10 .................................................................... approx. 10% of Full Power
P-0 ...................................................... No power throughout the cooking time
START/MINUTE PLUS pad, Sensor cook pads, Reheat pads, Defrost pads,
Number selection pads, Power Level pad, Timer/Clock pad,Stop/Clear pad,
Keep warm plus, Hot Water, Sensor reheat, custom help and Night light.
Oven Cavity Light
Yes
Safety Standard
UL Listed FCC Authorized
DHHS Rules, CFR, Title 21, Chapter 1, Subchapter J