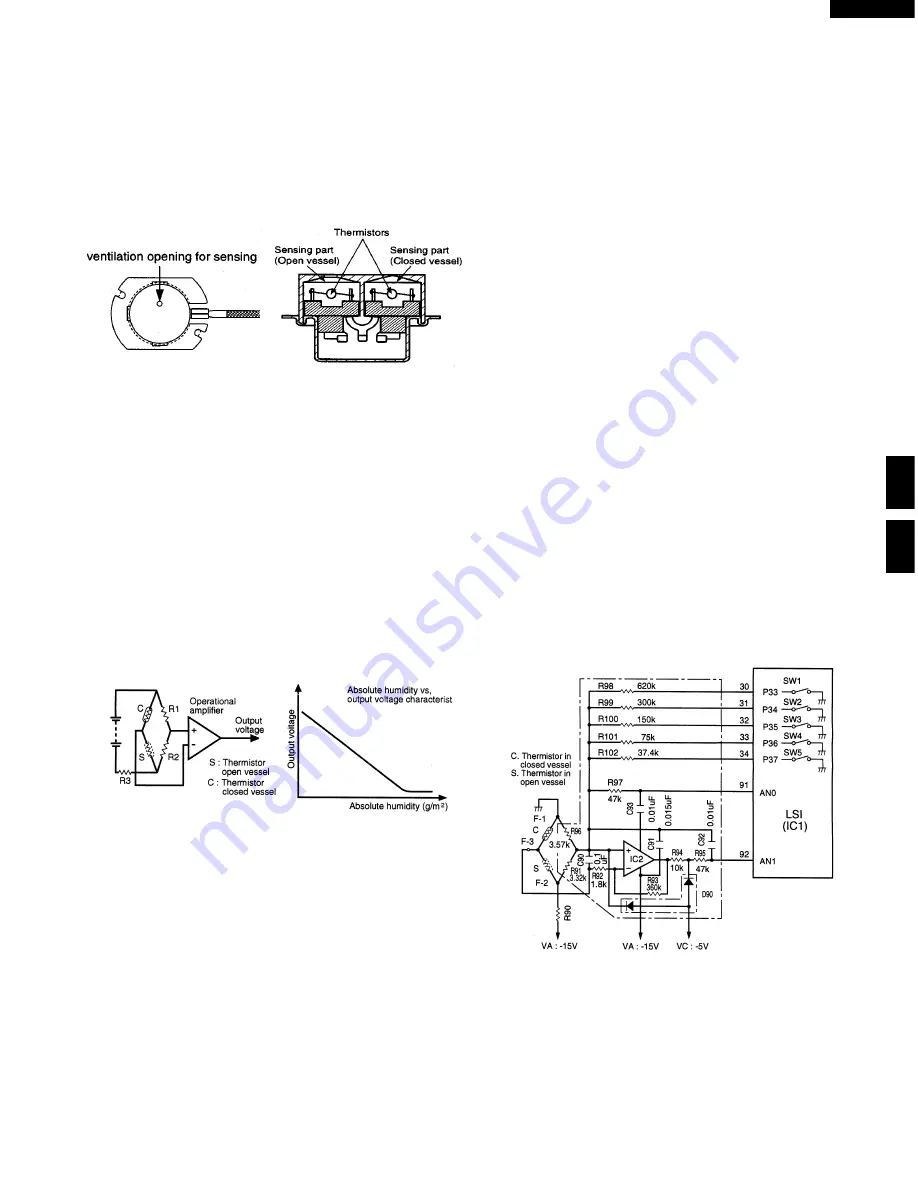
25
R-420CK
R-420CW
ABSOLUTE HUMIDITY SENSOR CIRCUIT
(1) Structure of Absolute Humidity Sensor
The absolute humidity sensor includes two thermistors
as shown in the illustration. One thermistor is housed in
the closed vessel filled with dry air while another in the
open vessel. Each sensor is provided with the protective
cover made of metal mesh to be protected from the
external airflow.
(2) Operational Principle of Absolute Humidity Sensor
The figure below shows the basic structure of an absolute
humidity sensor. A bridge circuit is formed by two
thermistors and two resistors(R1 and R2). The output of
the bridge circuit is to be amplified by the operational
amplifier.
Each thermistor is supplied with a current to keep it
heated at about 150
O
C (302
O
F), the resultant heat is
dissipated in the air and if the two thermistors are placed
in different degrees of heat conductivity leading to a
potential difference between them causing an output
voltage from the bridge circuit, the intensity of which is
increased as the absolute humidity of the air increases.
Since the output is very minute, it is amplified by the
operational amplifier.
(2) Detector circuit of Absolute Humidity Sensor circuit
This detector circuit is used to detect the output voltage
of the absolute humidity circuit to allow the LSI to control
sensor cooking of the unit. When the unit is set in the
sensor cooking mode, 16 seconds clearing cycle occurs
then the detector circuit starts to function and the LSI
observes the initial voltage available at its AN1 terminal.
With this voltage given, the switches SW1 to SW5 in the
LSI are turned on in such a way as to change the
resistance values in parallel with R107 ~ R111 of IC2 .
Changing the resistance value results in that there is the
same potential at both F-3 terminal of the absolute
humidity sensor and AN0 terminal of the LSI. The voltage
of AN1 terminal will indicate about 16 seconds about -
2.50 V. This initial balancing is set up about 16 seconds
after the unit is put in the Sensor Cooking mode. As the
sensor cooking proceeds, the food is heated to generate
moisture by which the resistance balance of the bridge
circuit is deviated to increase the voltage available at
AN1 terminal of the LSI.
Then the LSI observes that the voltage at AN1 terminal
and compares it with its initial value, and when the
comparison rate reaches the preset value (fixed for each
menu to be cooked), the LSI causes the unit to stop
sensor cooking; thereafter, the unit goes in the next
operation automatically. When the LSI starts to detect
the initial voltage at AN1 terminal 16 seconds after the
unit has been put in the Sensor Cooking mode, if it is not
possible to balance of the bridge circuit due to
disconnection of the absolute humidity sensor, ERROR
will appear on the display and the cooking is stopped.
1) Absolute humidity sensor circuit