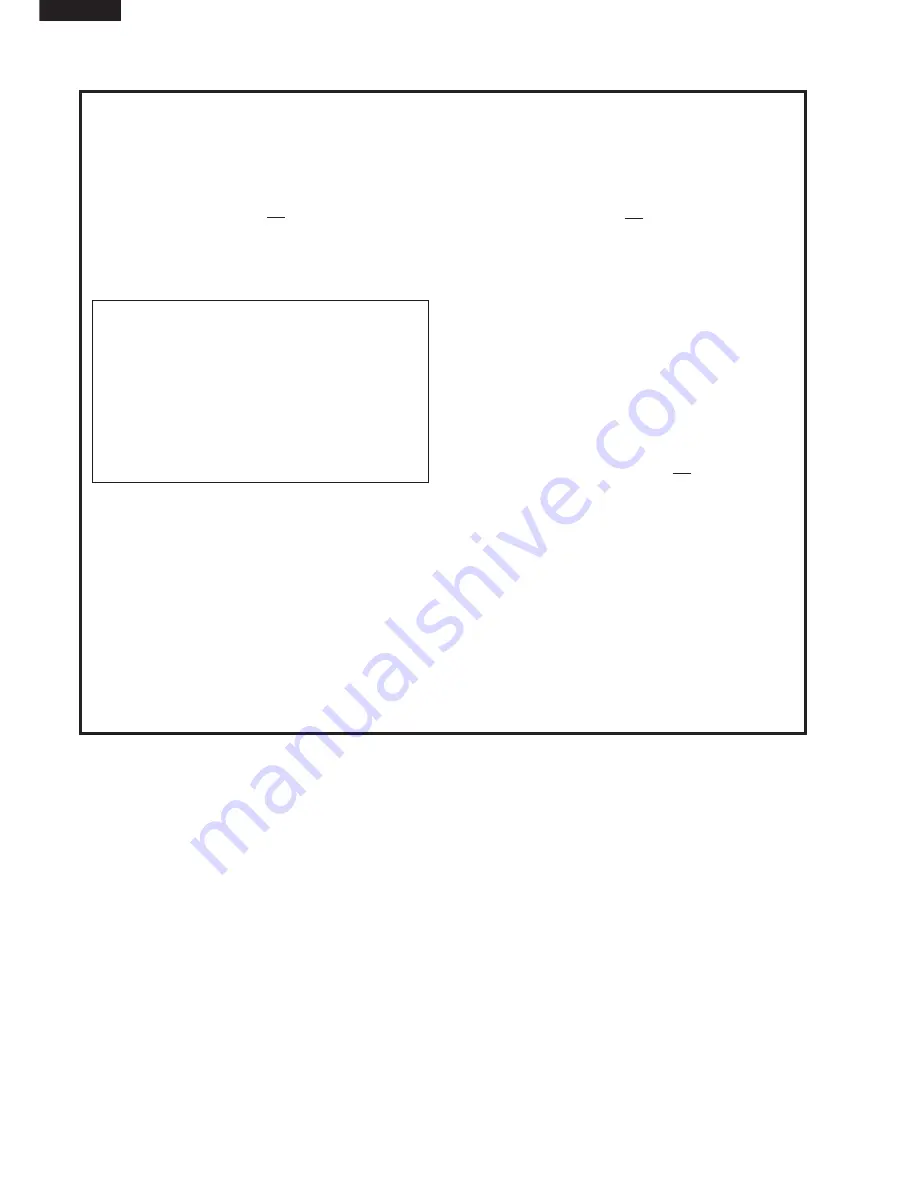
R-330H
6
SERVICING
WARNING TO SERVICE PERSONNEL
Microwave ovens contain circuitry capable of producing very high voltage and current, contact with following parts
of the high voltage circuit will result in electrocution. High voltage capacitor, Power transformer, Magnetron, High
voltage rectifier assembly, High voltage fuse, High voltage harness.
REMEMBER TO CHECK 3D
1) Disconnect the supply.
2) Door opened, and wedged open.
3) Discharge the high voltage capacitor.
WARNING: AGAINST THE CHARGE OF THE
HIGH-VOLTAGE CAPACITOR
The high-voltage capacitor remains charged about
60 seconds after the oven has been switched off.
Wait for 60 seconds and then short-circuit the
connection of the high-voltage capacitor (that is, of
the connecting lead of the high-voltage rectifier)
against the chassis with the use of an insulated
screwdriver.
Sharp recommend that wherever possible fault-finding
is carried out with the supply disconnected. It may in,
some cases, be necessary to connect the supply after
the outer case has been removed, in this event carry
out 3D checks and then disconnect the leads to the
primary of the power transformer. Ensure that these
leads remain isolated from other components and the
oven chassis. (Use insulation tape if necessary.) When
the testing is completed carry out 3D checks and
reconnect the leads to the primary of the power trans-
former.
REMEMBER TO CHECK 4R
1) Reconnect all leads removed from components
during testing.
2) Replace the outer case (cabinet).
3) Reconnect the supply.
4) Run the oven. Check all functions.
Microwave ovens should not be run empty. To test for
the presence of microwave energy within a cavity,
place a cup of cold water on the oven turntable, close
the door and set the microwave timer for two (2)
minutes. Set the power level to HIGH and push the
START button. When the two minutes has elapsed
(timer at zero) carefully check that the water is now hot.
If the water remains cold carry out 3D checks and re-
examine the connections to the component being
tested.
When troubleshooting the microwave oven, it is helpful to
follow the Sequence of Operation in performing the
checks. Many of the possible causes of trouble will require
that a specific test be performed. These tests are given a
procedure letter which will be found in the "Test Procedure
"section.
When all service work is completed, and the oven is fully assembled, the microwave power output should be
checked and microwave leakage test should be carried out.
TROUBLESHOOTING GUIDE
IMPORTANT: If the oven becomes inoperative because
of a blown fuse F10A in the 1st. latch
switch - 2nd. interlock relay - monitor switch
circuit, check the 1st. latch switch, 2nd.
interlock relay and monitor switch before
replacing the fuse F10A.
Summary of Contents for R-330H
Page 2: ...R 330H ...