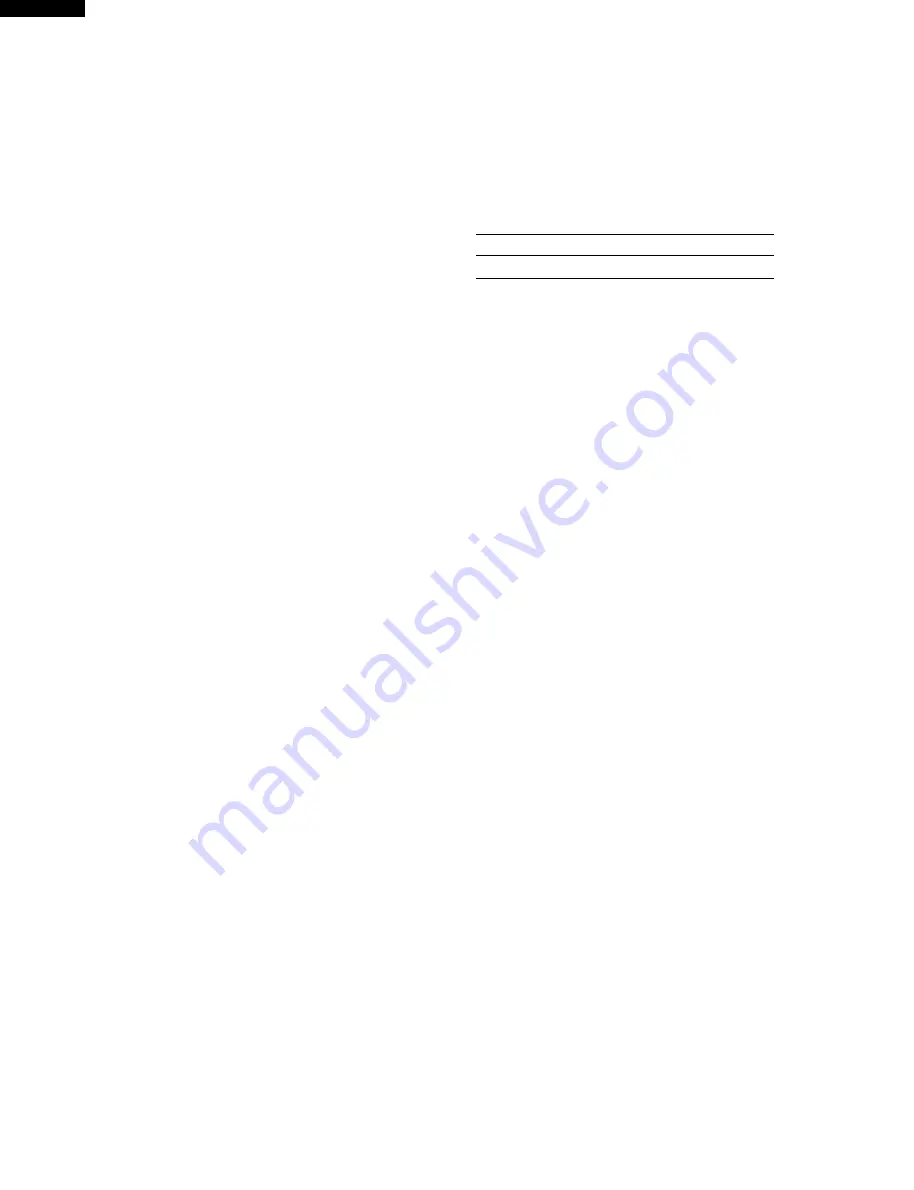
18
R-310BK
R-310BW
TOUCH CONTROL PANEL ASSEMBLY
OUTLINE OF TOUCH CONTROL PANEL
The touch control section consists of the following units.
(1) Key Unit
(2) Control Unit (The Control Unit consists of Power Unit and
CPU Unit).
The principal functions of these units and the signals com-
municated among them are explained below.
Key Unit
The key unit is composed of a matrix, signals generated in
the LSI are sent to the key unit through P73, P81, P82, P83,
P90 and P91
.
When a key pad is touched, a signal is completed through
the key unit and passed back to the LSI through P60 - P63
to perform the function that was requested.
Control Unit
Control unit consists of LSI, ACL circuit, indicator circuit,
power source circuit, relay circuit, buzzer circuit, synchroniz-
ing signal circuit and back light circuit.
1) ACL
This circuit generates a signal which resets the LSI to the
initial state when power is supplied.
2) Indicator Circuit
This circuit consists of 12 segments and 3 common elec-
trodes using a Liquid Crystal Display.
3) Power Source Circuit
This circuit generates voltages necessary in the control
unit from the AC line voltage.
In addition, the synchronizing signal is available in order to
compose a basic standard time in the clock circuit.
Symbol
Voltage
Application
VC
-5.3V
LSI(IC1)
4) Relay Circuit
A circuit to drive the magnetron, fan motor, turntable motor
and light the oven lamp.
5) Buzzer Circuit
The buzzer is responsive to signals from the LSI to emit
audible sounds (key touch sound and completion sound).
6) Synchronizing Signal Circuit
The power source synchronizing signal is available in order
to compose a basic standard time in the clock circuit.
It accompanies a very small error because it works on
commercial frequency.
7) Door Sensing Switch
A switch to “tell” the LSI if the door is open or closed.
8) Back Light Circuit
A circuit to drive the back light (Light emitting diodes LD1-
LD5).
Summary of Contents for R-310BK
Page 39: ...37 R 310BK R 310BW ...