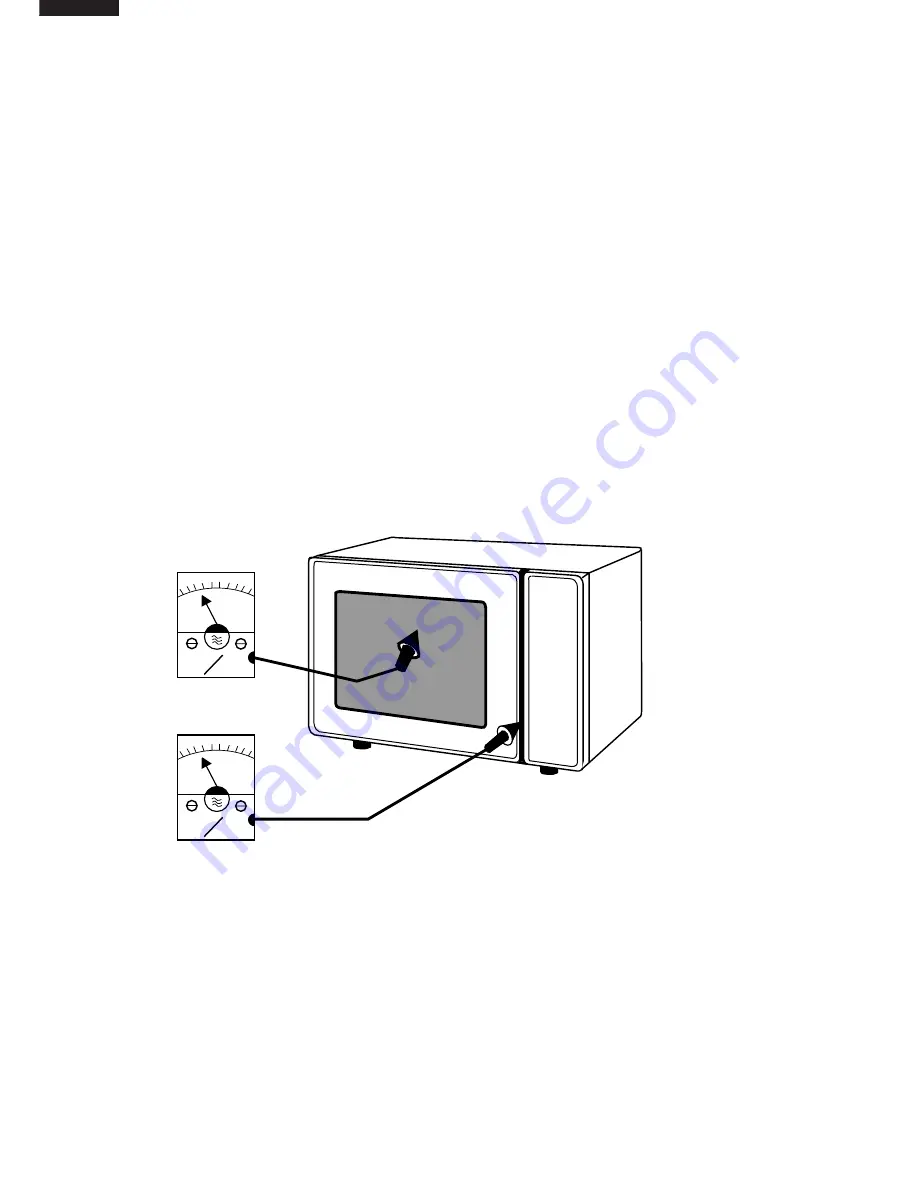
R-290H(S)
24
MICROWAVE MEASUREMENT
After adjustment of door latch switches, monitor switch
and door are completed individually or collectively, the
following leakage test must be performed with a survey
instrument and it must be confirmed that the result meets
the requirements of the performance standard for micro-
wave oven.
REQUIREMENT
The safety switch must prevent microwave radiation emis-
sion in excess of 5mW/cm
2
at any point 5cm or more from
external surface of the oven.
PREPARATION FOR TESTING:
Before beginning the actual test for leakage, proceed as
follows;
1. Make sure that the test instrument is operating nor-
mally as specified in its instruction booklet.
Important:
Survey instruments that comply with the requirement
for instrumentations as prescribed by the performance
standard for microwave ovens must be used for test-
ing.
Recommended instruments are:
NARDA 8100
NARDA 8200
HOLADAY HI 1500
SIMPSON 380M
2. Place the oven tray into the oven cavity.
3. Place the load of 275
±
15ml of water initially at 20
±
5˚C in the centre of the oven tray. The water
container should be a low form of 600 ml beaker with
inside diameter of approx. 8.5cm and made of an
electrically non-conductive material such as glass
or plastic.
The placing of this standard load in the oven is impor-
tant not only to protect the oven, but also to insure that
any leakage is measured accurately.
4. Close the door and turn the oven ON with the timer set
for several minutes. If the water begins to boil before
the survey is completed, replace it with 275ml of cool
water.
5. Move the probe slowly (not faster that 2.5cm/sec.)
along the gap.
6. The microwave radiation emission should be meas-
ured at any point of 5cm or more from the external
surface of the oven.
mW cm
2
mW cm
2
Microwave leakage measurement at 5 cm distance
SHARP
Summary of Contents for R-290H
Page 2: ...R 290H S 36 ...