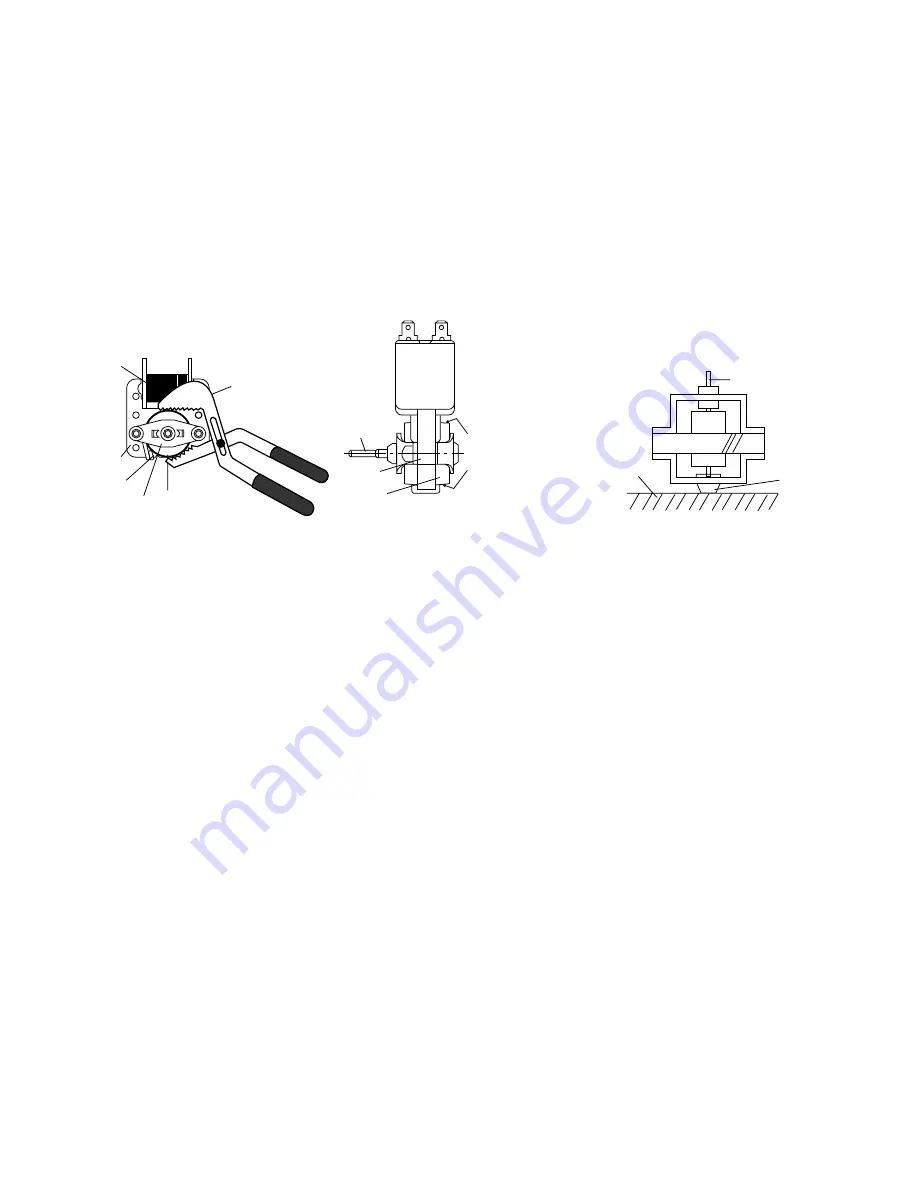
R220KW
11 – 5
8. Remove the fan blade assembly from the shaft of the fan motor by
pulling and rotating the fan blade with your hand.
9. Now, the fan blade will be free.
CAUTION: DO NOT RE-USE THE REMOVED FAN BLADE
BECAUSE THE HOLE (FOR SHAFT) MAY BE LARGER
THAN NORMAL.
10.Now, the fan motor is free.
2. INSTALLATION
1. Install the fan blade to the fan motor shaft according to the following
procedure.
2. Hold the center of the bracket which supports the shaft of the fan
motor on the flat table.
3. Apply the screw lock tight into the hole (for shaft) of the fan blade.
4. Install the fan blade to the shaft of fan motor by pushing the fan
blade with a small, light weight, ball peen hammer or rubber mallet.
CAUTION: DO NOT HIT THE FAN BLADE STRONGLY WHEN
INSTALLED BECAUSE THE BRACKET MAY BE TRANS-
FORMED.
MAKE SURE THAT THE FAN BLADE ROTATES
SMOOTH AFTER INSTALLED.
MAKE SURE THAT THE AXIS OF THE SHAFT IS NOT
SLANTED.
5. Install the fan motor assembly to the oven cavity back plate with
two (2) screws.
6. Connect the wire leads to the magnetron and fan motor, referring to
the pictorial diagram.
[12] DOOR SENSING SWITCH/SECONDARY INTERLOCK SWITCH AND MONITOR SWITCH
REMOVAL
1. REMOVAL
1. Disconnect the power supply cord and remove outer case.
2. Open the door and block it open.
3. Discharge high voltage capacitor.
4. Remove the control panel assembly, referring to section of CON-
TROL PANEL ASSEMBLY REMOVAL.
5. Remove the switch lever from the oven cavity.
6. Disconnect wire leads from the switches.
7. Remove two (2) screws holding latch hook to oven flange.
8. Remove latch hook assembly from oven flange.
9. Push outward on the two (2) retaining tabs holding switch in place.
10.Switch is now free.
2. REINSTALL
1. Re-install each switch in its place. The secondary interlock/monitor
switches are in the lower position and the door sensing switch is in
the upper position.
2. Secure latch hook (with two (2) mounting screws) to oven flange.
3. Re-connect wire leads to each switch. Refer to pictorial diagram.
4. Install the switch lever to the oven cavity.
5. Reinstall the control panel assembly to the oven cavity.
6. Reconnect wire leads to the control unity, referring to the pictorial
diagram.
7. Make sure that the monitor switch is operating properly and check
continuity of the monitor circuit. Refer to chapter "Test Procedure"
and Adjustment procedure.
[13] DOOR SENSING SWITCH/SECONDARY INTERLOCK SWITCH AND MONITOR SWITCH
ADJUSTMENT
1. Adjustment
1. Disconnect the power supply cord, and then remove outer case.
2. Open the door and block it open.
3. Discharge high voltage capacitor.
If the door sensing switch, secondary interlock switch and monitor
switch do not operate properly due to a misadjustment, the following
adjustment should be made.
4. Loosen the two (2) screws holding latch hook to the oven cavity
front flange.
5. With door closed, adjust latch hook by moving it back and forth,
and up and down. In and out play of the door allowed by the upper
and lower position of the latch hook should be less than 0.5mm.
The vertical position of the latch hook should be adjusted so that
the door sensing switch and secondary interlock switch are acti-
vated with the door closed. The horizontal position of the latch hook
should be adjusted so that the plunger of the monitor switch is
pressed with the door closed.
6. Secure the screws with washers firmly.
7. Check the operation of all switches. If each switch has not activated
with the door closed, loosen screw and adjust the latch hook posi-
tion.
Gap
Rotor
Bracket
Stator
Groove joint pliers
Coil
Shaft
Axis
Stator
Rotor
These are the positions
that should be pinched
with pliers.
Shaft
Table
Center of
bracket
Rear View
Side View