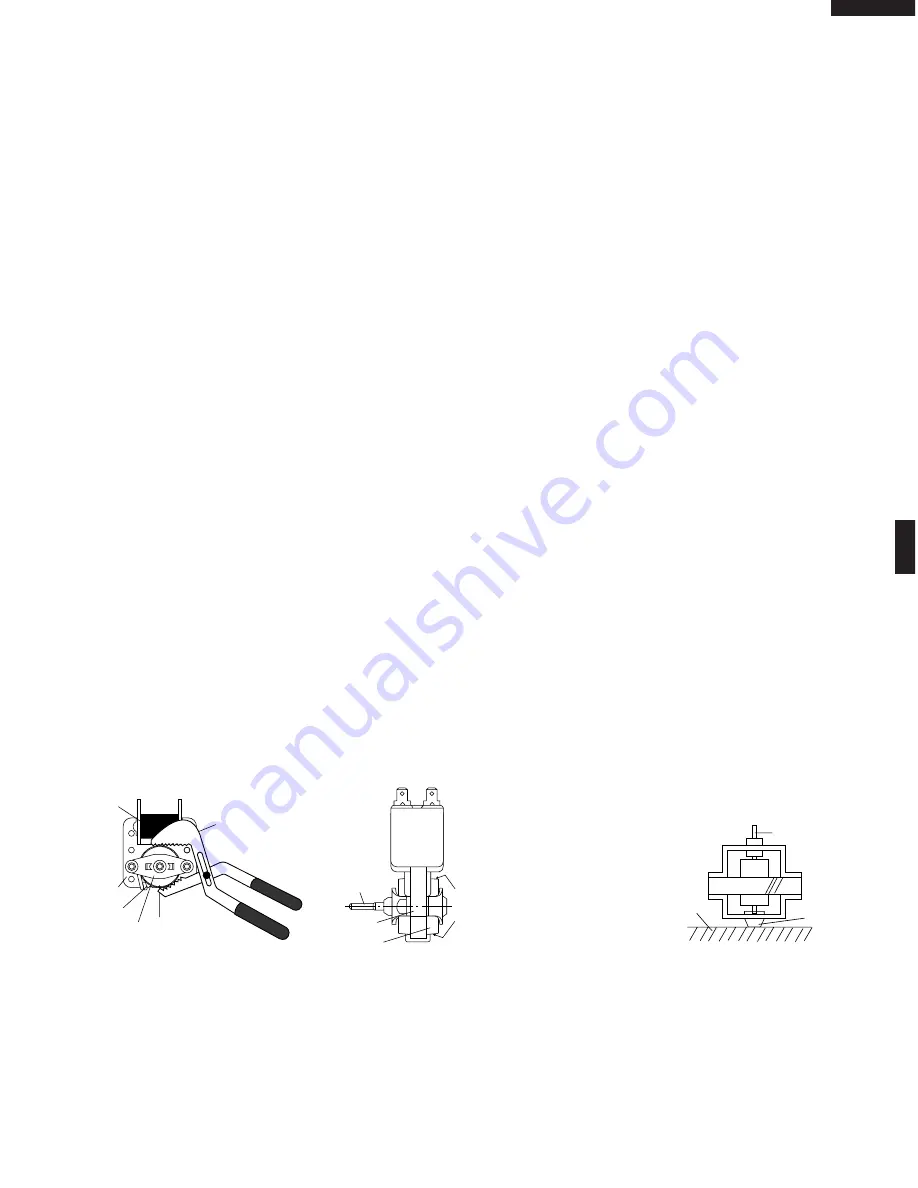
25
R-220DW
R-230DK
R-230DW
COOLING FAN MOTOR REMOVAL
REMOVAL
1. Disconnect the power supply cord and remove outer case.
2. Open the door and block it open.
3. Discharge high voltage capacitor.
4. Disconnect the wire leads from the fan motor.
5. Remove the one (1) screw holding the chassis support
to the oven cavity front plate.
6. Remove the chassis support .
7. Release the filament lead of the power transformer and
the H.V. wire from the fan duct.
8. Remove the one (1) screw holding the light mounting
plate to the oven cavity.
9. Release the wire leads (to the oven lamp) from the hole
of the fan duct.
10.Remove the one (1) screw holding the fan duct to the
waveguide flange.
11.Release the fan motor assembly from the oven cavity.
12.Remove the fan blade from the fan motor shaft according
to the following procedure.
13.Hold the edge of the rotor of the fan motor by using a pair
of groove joint pliers.
CAUTION:
• Make sure that no metal pieces enter the gap
between the rotor and the stator of the fan
motor. Because the rotor is easily damaged by
pliers and metal pieces may be produced.
• Do not touch the pliers to the coil of the fan
motor because the coil may be cut or damaged.
• Do not disfigure the bracket by pinching with
the pliers.
14.Remove the fan blade assembly from the shaft of the fan
motor by pulling and rotating the fan blade with your
hand.
15.Now, the fan blade will be free.
CAUTION:
• Do not re-use the removed fan blade because
the hole (for shaft) may be larger than normal.
16.Remove the two (2) screws holding the fan motor to the
fan duct.
17.Now, the fan motor is free.
INSTALLATION
1. Install the fan motor to the fan duct with the two (2)
screws.
2. Install the fan blade to the fan motor shaft according to
the following procedure.
3. Hold the center of the bracket which supports the shaft
of the fan motor on the flat table.
4. Apply the screw lock tight into the hole (for shaft) of the
fan blade.
5. Install the fan blade to the shaft of fan motor by pushing
the fan blade with a small, light weight, ball peen hammer
or rubber mallet.
CAUTION:
• Do not hit the fan blade strongly when installed
because the bracket may be transformed.
• Make sure that the fan blade rotates smooth after
installed.
• Make sure that the axis of the shaft is not slanted.
6. Install the fan motor assembly to the oven cavity by fitting
the tabs of the fan duct into the holes of the oven cavity
and the waveguide flange.
7. Hold the fan duct to the waveguide flange with the one (1)
screw.
8. Re-install the light mounting plate to the oven cavity with
the one (1) screw.
9. Insert the end of the chassis support into the slit of the
oven cavity rear cabinet.
10.Re-install the chassis support to the oven cavity front
plate with the one (1) screw.
11.Install the filament lead and the H.V. wire into the hole of
the fan duct .
12.Re-install the wire leads (to the oven lamp) to the hole of
the fan duct.
13.Connect the wire leads to the fan motor, referring to the
pictorial diagram.
Side View
Rear View
Shaft
Table
Center of
bracket
1. Disconnect the power supply cord and remove outer case.
2. Open the door and block it open.
3. Discharge high voltage capacitor.
4. Disconnect wire leads from the switches and control
panel.
5. Remove the control panel assembly from the oven cavity
front flange. Refer to chapter "CONTROL PANEL
ASSEMBLY REMOVAL"
6. Remove two (2) screws holding latch hook to oven
flange.
7. Remove latch hook assembly from oven flange.
8. To remove the secondary interlock switch.
8-1. Pull out the secondary interlock switch from the latch
hook, by pushing outward on the tab that is holding the
DOOR SENSING SWITCH, SECONDARY INTERLOCK SWITCH AND MONITOR SWITCH REMOVAL
Gap
Rotor
Bracket
Stator
Groove joint pliers
Coil
Shaft
Axis
Stator
Rotor
These are the positions
that should be pinched
with pliers