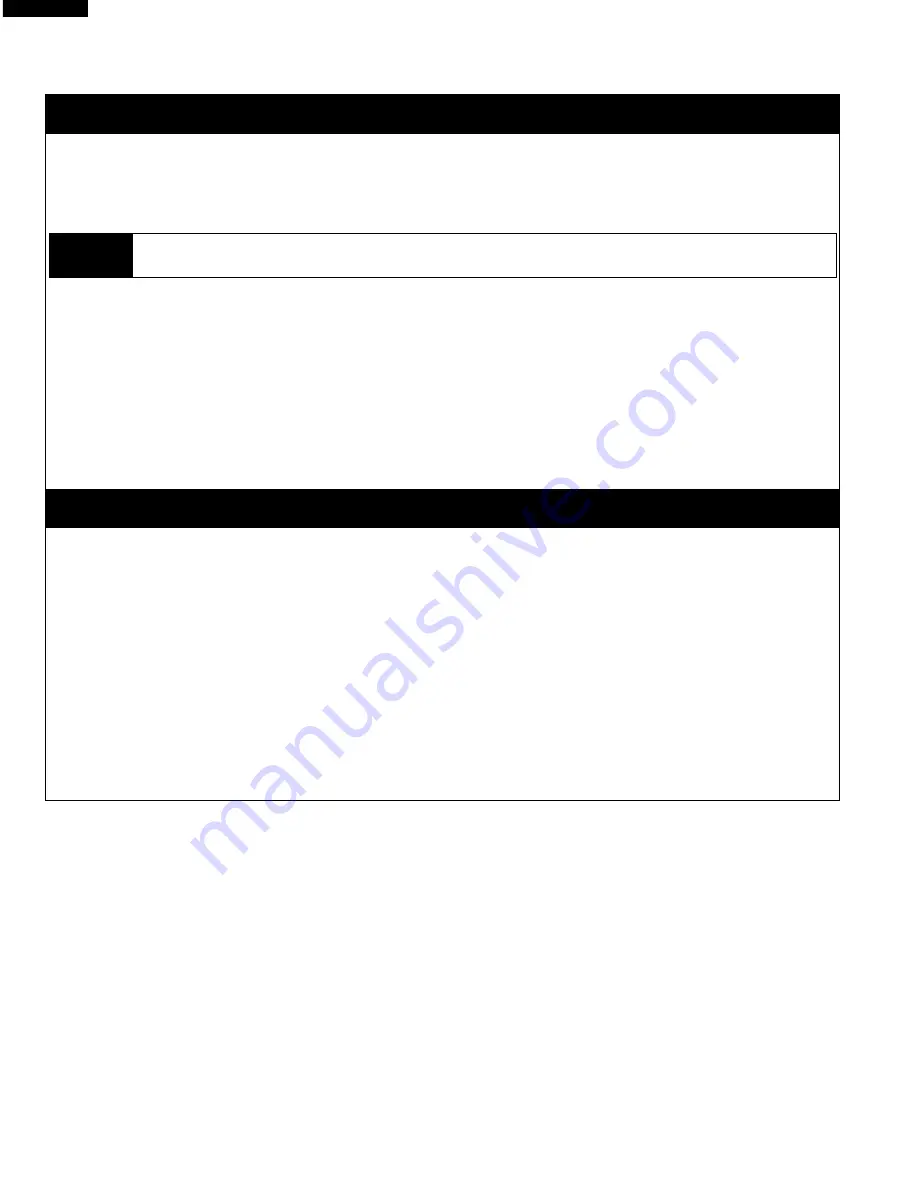
14
R-1610
R-1611
R-1612
To prevent an electric shock, take the following pre-
cautions.
1. Before wiring,
1) Disconnect the power supply cord.
2) Open the door block it open.
3) Discharge the high voltage capacitor and wait for 60
seconds.
2. Don’t let the wire leads touch to the followiong parts;
1) High voltage parts:
Magnetron, High voltage transformer, High voltage
capacitor and High voltage rectifier assembly.
2) Hot parts:
Oven lamp, Magnetron, High voltage transformer
and Oven cavity.
WARNING FOR WIRING
3) Sharp edge:
Bottom plate, Oven cavity, Waveguide flange,
Chassis support and other metallic plate.
4) Movable parts (to prevent a fault)
Fan blade, Fan motor, Switch, Switch lever, Open
button.
3. Do not catch the wire leads in the outer case cabinet.
4. Insert the positive lock connector until its pin is locked
and make sure that the wire leads do not come off even
if the wire leads are pulled.
5. To prevent an error function, connect the wire leads
correctly, referring to the Pictorial Diagram.
Please refer to ‘OVEN PARTS, CABINET PARTS, CONTROL PANAL PARTS, DOOR PARTS’, when carrying out any of
the following removal procedures:
HOOD FAN MOTOR, HOOD DUCT, OVEN LAMP SOCKET AND AH. SENSOR REMOVAL
1. Disconnect the power supply cord and remove the oven
from wall and remove outer case. (Refer to procedure of
"Removal of Oven from Wall" and "Outer case Removal"
of the base model Service Manual)
2. Open the door and block it open.
3. Discharge high voltage capacitor.
4. Disconnect the 6-pin connector of the hood fan motor
from the main wire harness located at the right edge of the
hood duct and release the snap band from the hood duct.
5. Remove the hood fan motor from the hood duct by lifting
it up.
6. Now, the hood fan motor is free.
7. Disconnect the connector CN-F from the control unit.
8. Remove one (1) screw holding the hood duct to the oven
cavity front plate.
9. Release the 6-pin connector and the 3-pin connector of
the main harness A from the hood duct.
10.Disconnect the wire leads from the fan motor and chassis
support, and release the wire leads from holes of the
hood duct.
11.Remove the two (2) unit mounting screws from the
chassis support (right side) and the hood duct (left side).
12.Remove the one (1) screw holding the chassis support.
13.Remove the chassis support.
Microwave ovens contain circuitry capable of producing very high voltage and current, contact with following parts may
result in severe, possibly fatal, electric shock.
(Example)
High Voltage Capacitor, Power Transformer, Magnetron, High Voltage Rectifier Assembly, High Voltage Harness etc..
WARNING:
Avoid possible exposure to microwave energy. Please follow the instructions below before
operating the oven.
WARNING AGAINST HIGH VOLTAGE:
COMPONENT REPLACEMENT AND ADJUSTMENT PROCEDURE
1. Disconnect the power supply cord.
2. Visually check the door and cavity face plate for damage
(dents, cracks, signs of arcing etc.).
Carry out any remedial work that is necessary before
operating the oven.
Do not operate the oven if any of the following conditions
exist;
1. Door does not close firmly.
2. Door hinge, support or latch hook is damaged.
3. The door gasket or seal is damaged.
4. The door is bent or warped.
5. There are defective parts in the door interlock system.
6. There are defective parts in the microwave generating
and transmission assembly.
7. There is visible damage to the oven.
Do not operate the oven:
1. Without the RF gasket (Magnetron).
2. If the wave guide or oven cavity are not intact.
3. If the door is not closed.
4. If the outer case (cabinet) is not fitted.