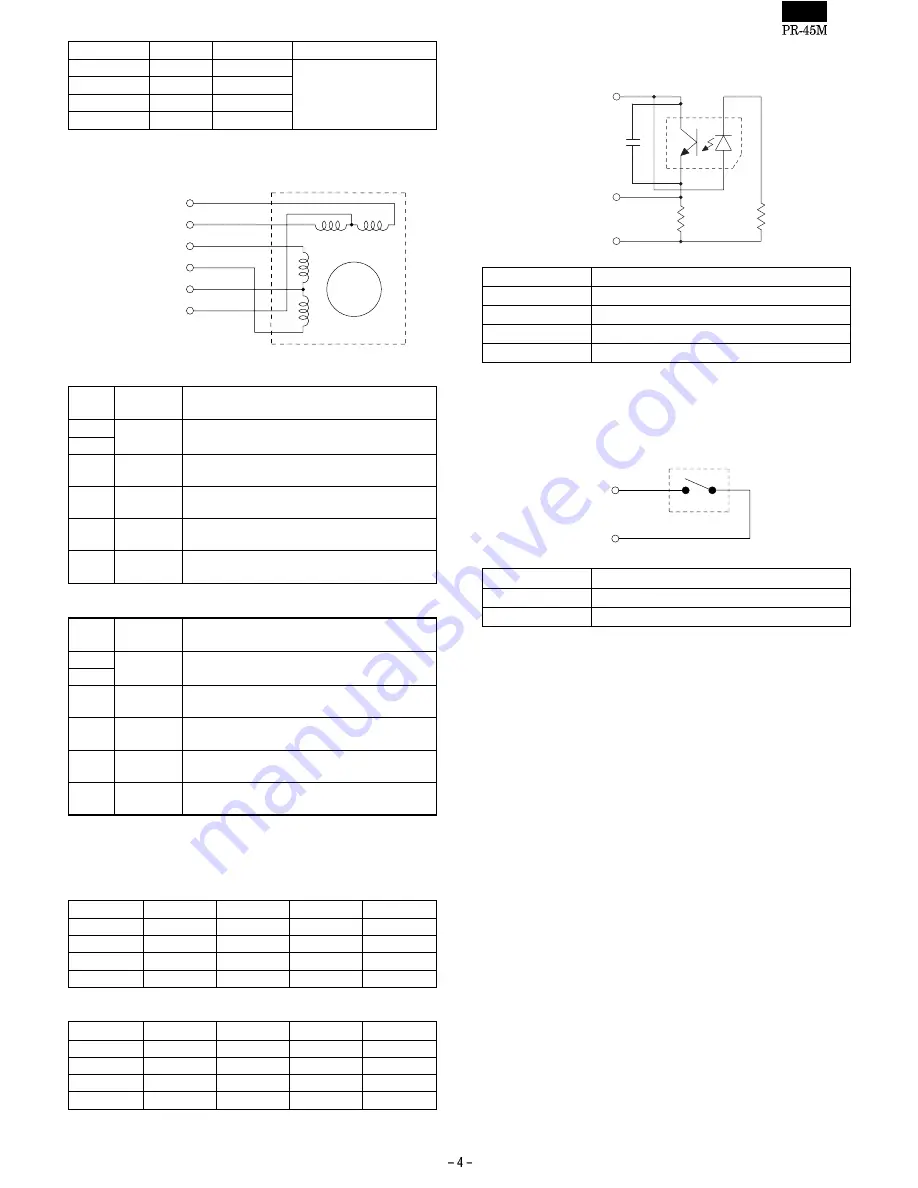
STROBE No.
DOT No.
Dots/Strobe
Note
/STROBE4
577
∼
864
288
Excluding dots No.1
∼
88,
377
∼
488 and 777
∼
864
/STROBE3
433
∼
576
144
/STROBE2
289
∼
432
144
/STROBE1
1
∼
288
288
4) Motor block diagram
<JOURNAL MOTOR>
PIN
No.
SIGNAL
NAME
DESCRIPTION
1
VJCOM
COMMON voltage
2
3
/JPFA
JOURNAL-side paper feed motor phase A
driving signal
4
/JPFB
JOURNAL-side paper feed motor phase B
driving signal
5
/JPFC
JOURNAL-side paper feed motor phase C
driving signal
6
/JPFD
JOURNAL-side paper feed motor phase D
driving signal
<RECEIPT MOTOR>
PIN
No.
SIGNAL
NAME
DESCRIPTION
1
VRCOM
COMMON voltage
2
3
/RPFA
RECEIPT-side paper feed motor phase A
driving signal
4
/RPFB
RECEIPT-side paper feed motor phase B
driving signal
5
/RPFC
RECEIPT-side paper feed motor phase C
driving signal
6
/RPFD
RECEIPT-side paper feed motor phase D
driving signal
The paper feed motors are stepping motors with 4-phase driving
coils. The motors are driven by switching over the driving coils.
<MOTOR DRIVE SEQUENCE> ON: Energized/OFF: Not energized
JOURNAL MOTOR
STEP No.
PHASE A
PHASE B
PHASE C
PHASE D
1
ON
OFF
OFF
ON
2
ON
OFF
ON
OFF
3
OFF
ON
ON
OFF
4
OFF
ON
OFF
ON
RECEIPT MOTOR
STEP No.
PHASE A
PHASE B
PHASE C
PHASE D
1
ON
OFF
ON
OFF
2
ON
OFF
OFF
ON
3
OFF
ON
OFF
ON
4
OFF
ON
ON
OFF
5) End sensor block diagram
SIGNAL NAME
DESCRIPTION
+5V
+5V
/RPES
Receipt paper end sensor detecting signal
/JPES
Journal paper end sensor detecting signal
GNDL
GND
The photo diode on the PWB detects the presence/absence of the
paper passing under the journal and receipt platens.
6) Head up sensor
SIGNAL NAME
DESCRIPTION
PHUPS
Head-up detecting signal
GNDL
GND
The micro switch at the left side of the printer detects the head-up
state.
ON:
Head-down
OFF: Head-up
A
B
C
D
M
/RPFA, /JPFA
/RPFB, /JPFB
/RPFC, /JPFC
/RPFD, /JPFD
VRCOM, VJCOM
VRCOM, VJCOM
stepping motor
+5V
/RPES, /JPES
GND-L
1
2
3
4
39K
Ω
220
Ω
reflex photo sensor
0.1µF
GND-L
PHUPS
micro switch