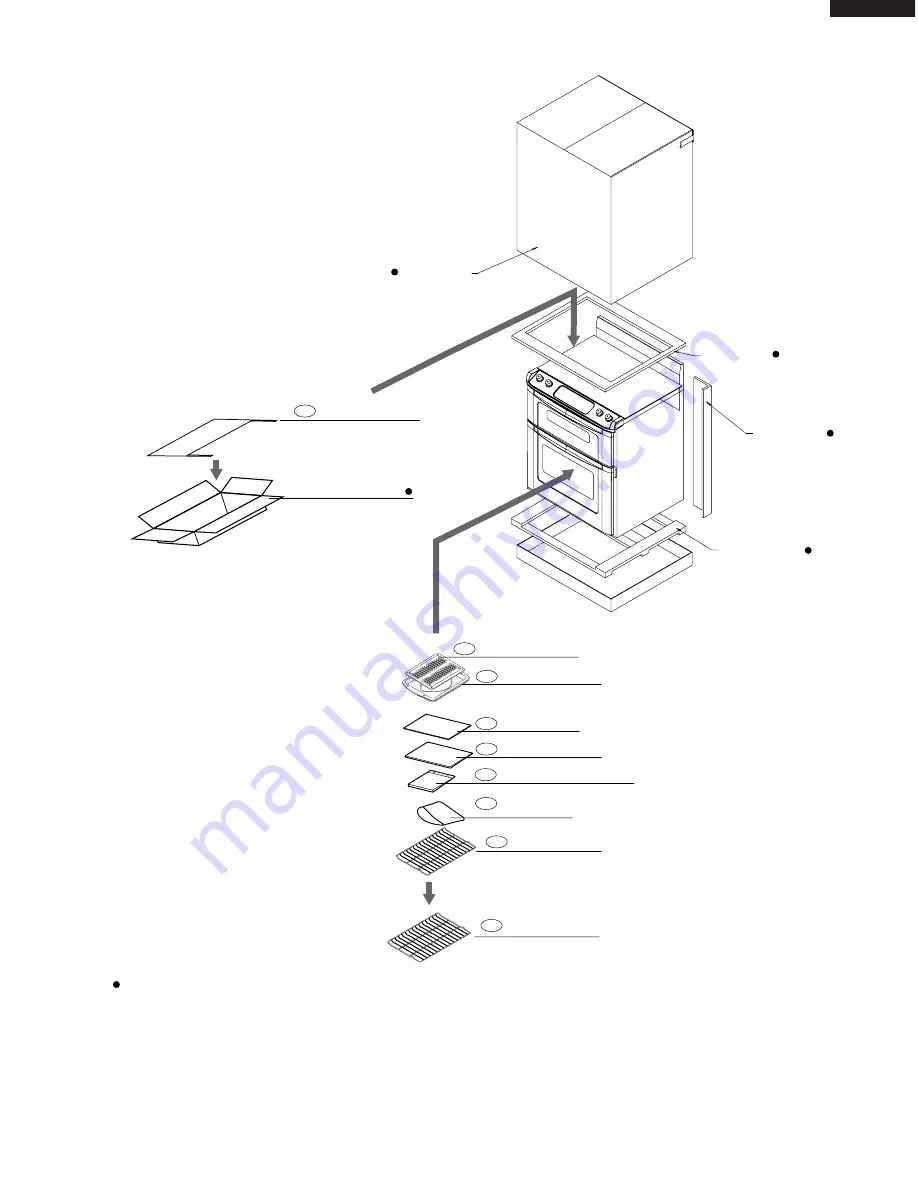
69
KB-3300JS
KB-3300JK
KB-3300JW
WOOD TOP FRAME
SUPPORT CORNERS
EXTENDED RACK ASSY
*
BOILER PAN
INSTALLION MANUAL
OPERATION MANUAL
ANTI-TIP TEMPLATE
ANTI-TIP KIT
PACKING CASE
Non-replaceable items
BACK SPLASH HOLDER
WOOD BOTTOM FRAME
BACK SPLASH
OVEN RACK x 2
6-9
6-7
6-1
6-8
6-4
6-5
6-6
6-2
BOILER INSERT
6-3
*
Not included in early models.
PACKING
Summary of Contents for KB-3300JS
Page 6: ...4 KB 3300JS KB 3300JK KB 3300JW NOTES ...
Page 35: ...33 KB 3300JS KB 3300JK KB 3300JW IC 7 IC 8 OVEN TEMPERATURE SELF CLEANING CONTROL CIRCUIT ...
Page 36: ...34 KB 3300JS KB 3300JK KB 3300JW OVEN DOOR LOCK MOTOR CONTROL CIRCUIT ...
Page 37: ...35 KB 3300JS KB 3300JK KB 3300JW OVEN DOOR LOCK MOTOR DETECTION CIRCUIT ...