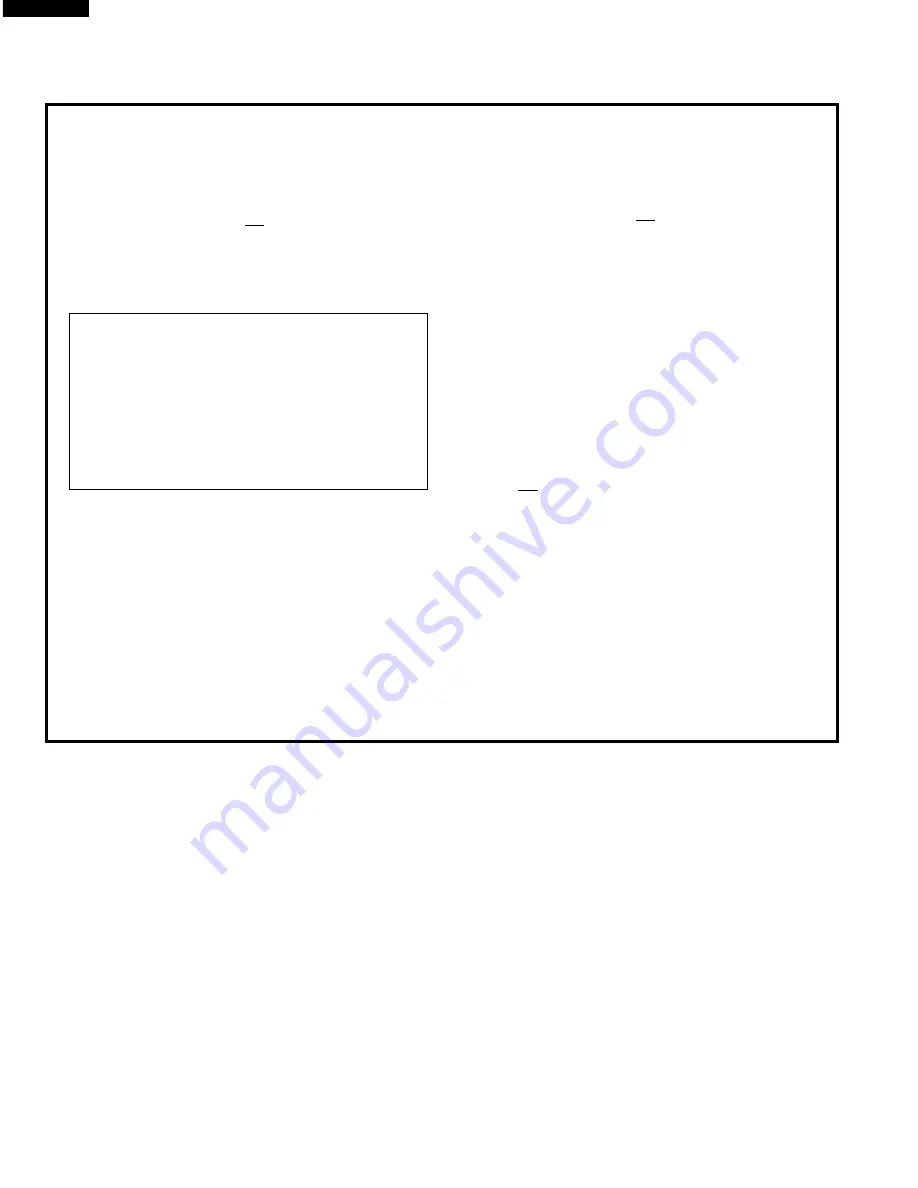
R-3S56
6
SERVICING
WARNING TO SERVICE PERSONNEL
Microwave ovens contain circuitry capable of producing very high voltage and current, contact with any part of the
high voltage circuit will result in electrocution. High voltage capacitor, Power transformer, Magnetron, High voltage
rectifier assembly, High voltage harness.
REMEMBER TO CHECK 3D
1) Disconnect the supply.
2) Door opened, and wedged open.
3) Discharge high voltage capacitor.
WARNING: AGAINST THE CHARGE OF THE
HIGH-VOLTAGE CAPACITOR
The high-voltage capacitor remains charged about
60 seconds after the oven has been switched off.
Wait for 60 seconds and then short-circuit the con-
nection of the high-voltage capacitor (that is, of the
connecting lead of the high-voltage rectifier) against
the chassis with the use of an insulated screwdriver.
Sharp recommend that wherever possible fault-finding
is carried out with the supply disconnected. It may in,
some cases, be necessary to connect the supply after
the outer case has been removed, in this event carry out
3D checks and then disconnect the leads to the primary
of the power transformer. Ensure that these leads re-
main isolated from other components and the oven
chassis. (Use insulation tape if necessary.) When the
testing is completed carry out 3D checks and reconnect
the leads to the primary of the power transformer.
REMEMBER TO CHECK 4R
1) Reconnect all leads removed from components during
testing.
2) Replace the outer case (cabinet).
3) Reconnect the supply.
4) Run the oven. Check all functions.
Microwave ovens should not be run empty. To test for
the presence of microwave energy within a cavity, place
a cup of cold water on the oven turntable, close the door
and set the microwave timer for two (2) minutes. Set the
power level to HIGH and push the START button. When
the two minutes has elapsed (timer at zero) carefully
check that the water is now hot. If the water remains cold
carry out 3D checks and re-examine the connections to
the component being tested.
When all service work is completed, and the oven is fully assembled, the microwave power output should be checked
and microwave leakage test carried out
When troubleshooting the microwave oven, it is helpful to
follow the Sequence of Operation in performing the
checks. Many of the possible causes of trouble will require
that a specific test be performed. These tests are given a
procedure letter which will be found in the "Test
Procedure"section.
TROUBLESHOOTING GUIDE
IMPORTANT: If the oven becomes inoperative because of
a blown fuse M6.3A in the 1st. latch switch
- 2nd. latch switch - monitor switch - monitor
resistor circuit, check the 1st. latch switch,
2nd. latch switch, monitor switch and moni-
tor resistor before replacing the fuse M6.3A.
Summary of Contents for Carousel R-3S56
Page 2: ...R 3S56 ...