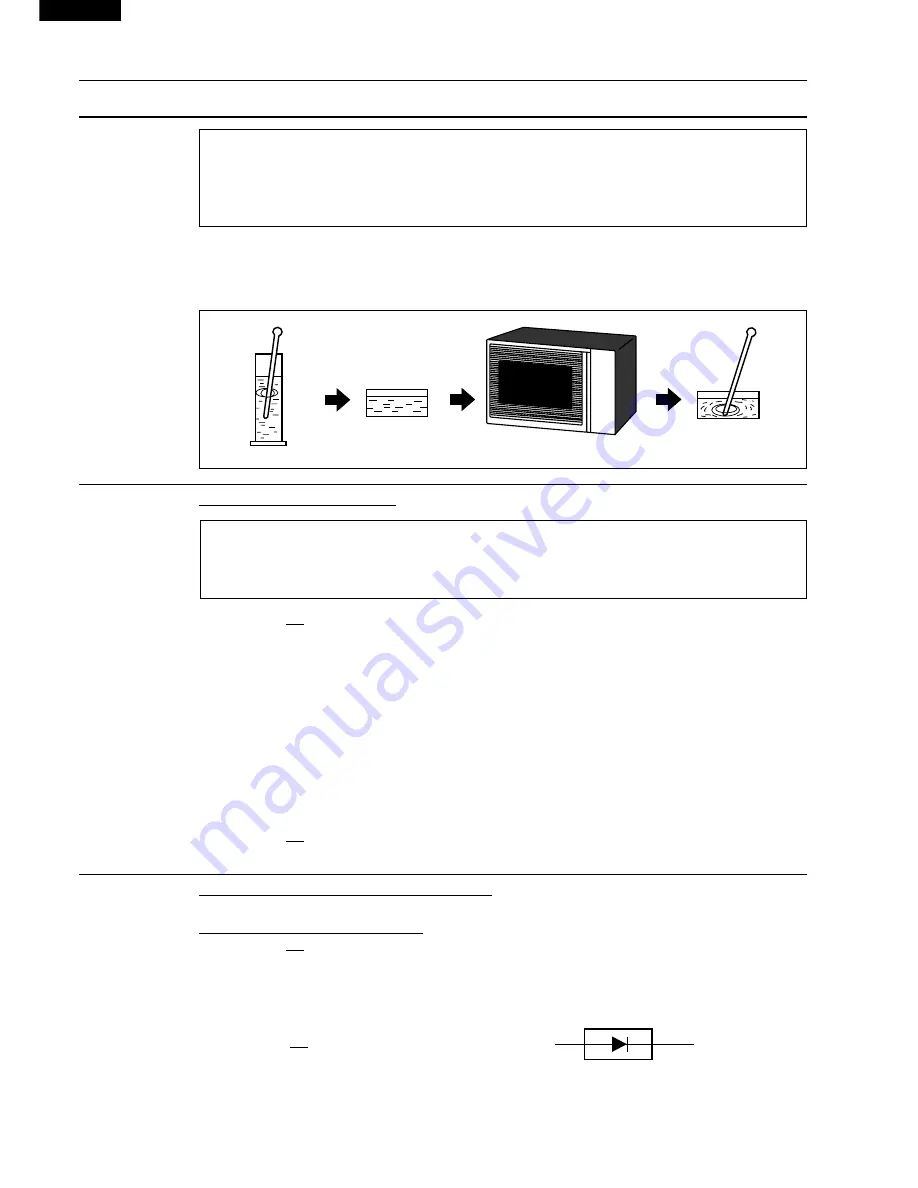
R-380E
10
Room temperature .................. To = 21˚C
Initial temperature ................. T1 = 11
°
C
Temperature after (36 + 3) = 39 sec. ................................................................ T2 = 21
°
C
Temperature difference Cold-Warm ..............................................................
∆
T1 = 10
°
C
Measured output power
The equation is “P = 115 x
∆
T” ........................................... P = 115 x 10
°
C = 1150 Watts
TEST PROCEDURES
PROCEDURE
LETTER
COMPONENT TEST
JUDGEMENT: The measured output power should be at least
±
15 % of the rated output power.
CAUTION: 1
°
C CORRESPONDS TO 115 WATTS REPEAT MEASUREMENT IF THE POWER IS
INSUFFICIENT.
1000g
1000g
1000g
T1˚C
T2˚C
Heat up for 39 sec.
B
POWER TRANSFORMER TEST
WARNING: High voltages and large currents are present at the secondary winding and filament
winding of the power transformer. It is very dangerous to work near this part when
the oven is on. NEVER make any voltage measurements of the high-voltage
circuits, including the magnetron filament.
CARRY OUT 3D CHECKS.
Disconnect the leads to the primary winding of the power transformer. Disconnect the filament and
secondary winding connections from the rest of the HV circuitry. Using an ohmmeter, set on a low
range, it is possible to check the continuity of all three windings. The following readings should be
obtained:
a. Primary winding .................... approx. 1.0
Ω
b. Secondary winding ............... approx. 86
Ω
c. Filament winding ................... less than 1
Ω
If the reading obtained are not stated as above, then the power transformer is probably faulty and
should be replaced.
CARRY OUT 4R CHECKS.
C
HIGH VOLTAGE RECTIFIER ASSEMBLY TEST
HIGH VOLTAGE RECTIFIER TEST
CARRY OUT 3D CHECKS.
Isolate the high voltage rectifier assembly from the HV circuit. The high voltage rectifier can be tested
using an ohmmeter set to its highest range. Connect the ohmmeter across the terminal B+C of the
high voltage rectifier and note the reading obtained. Reverse the meter leads and note this second
reading. The normal resistance is infinite in one direction and more than 100 k
Ω
in the other direction.
CARRY OUT 4R CHECKS.
NOTE: FOR MEASUREMENT OF THE RESISTANCE OF THE RECTIFIER, THE BATTERIES OF
THE MEASURING INSTRUMENT MUST HAVE A VOLTAGE AT LEAST 6 VOLTS, BECAUSE
OTHERWISE AN INFINITE RESISTANCE MIGHT BE SHOWN IN BOTH DIRECTIONS.
B
C
HIGH VOLTAGE RECTIFIER