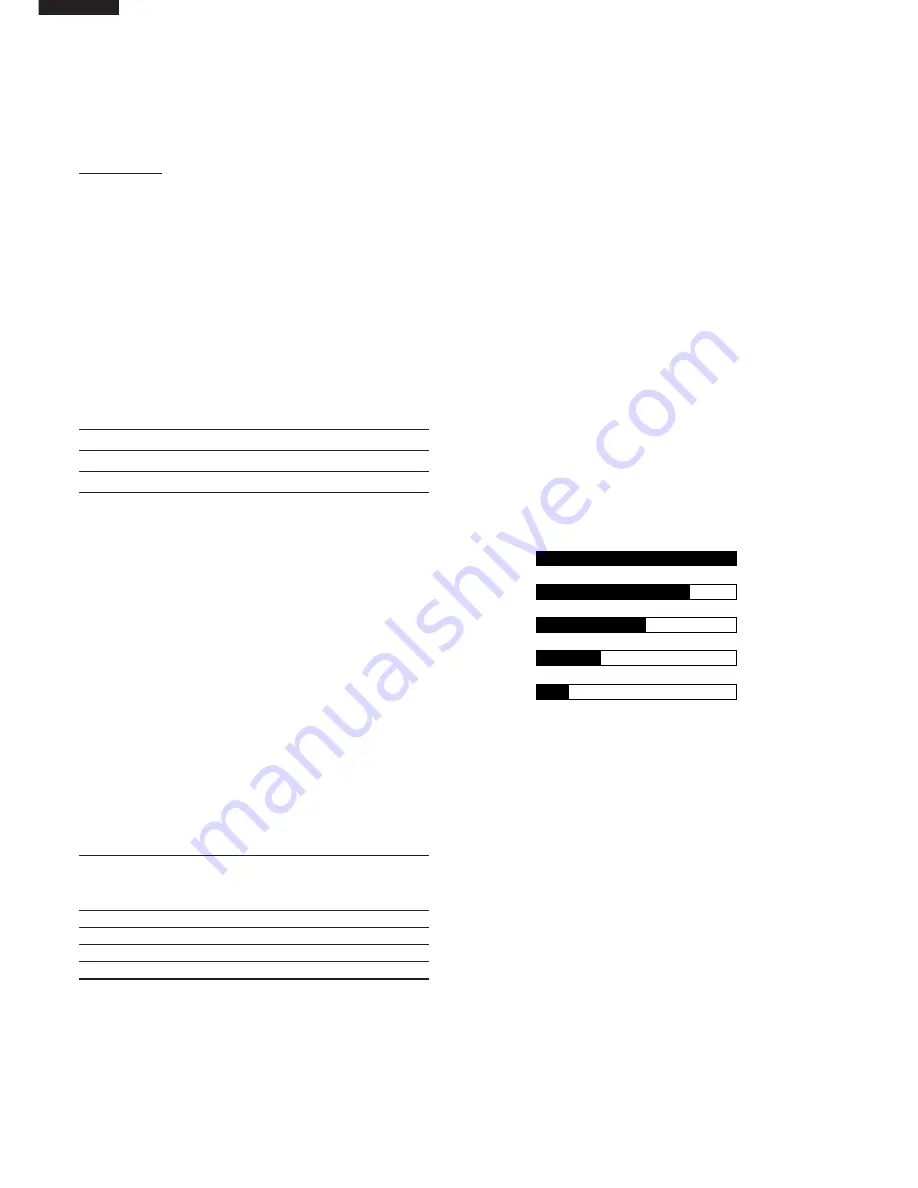
R-210D
4
OPERATION SEQUENCE
OFF CONDITION
Closing the door activates all door interlock switches
(1st. latch switch, 2nd. latch switch and stop switch).
IMPORTANT
When the oven door is closed, the monitor switch contacts
(COM-NC) must be open.
When the microwave oven is plugged in a wall outlet, rated
voltage is supplied to the noise filter and the control unit.
Figure O-1 on page 25
MICROWAVE COOKING CONDITION
HIGH COOKING
Select the power level HIGH by pressing the power level
button until the power level indicator indicates "HIGH".
And set the cooking time by rotating the Light Up Dial.
Function sequence
Figure O-2 on page 25
CONNECTED COMPONENTS
RELAY
Oven lamp, Fan motor, Turntable motor
RY1
Power transformer
RY2
1. Rated voltage is supplied to the primary winding of the
power transformer. The voltage is converted to about
3.3 volts A.C. output on the filament winding and high
voltage of approximately 2000 volts A.C. on the sec-
ondary winding.
2. The filament winding voltage (3.3 volts) heats the
magnetron filament and the high voltage (2000 volts) is
sent to the voltage doubling circuit, where it is doubled
to negative voltage of approximately 4000 volts D.C..
3. The 2450 MHz microwave energy produced in the
magnetron generates a wave length of 12.24 cm. This
energy is channelled through the waveguide (transport
channel) into the oven cavity, where the food is placed
to be cooked.
4. When the cooking time is up, a signal tone is heard and
the relays RY1+RY2 go back to their home position.
The circuits to the oven lamp, power transformer, fan
motor and turntable motor are cut off.
5. When the door is opened during a cook cycle, the
switches come to the following condition.
CONDITION
DURING
DOOR OPEN
SWITCH
CONTACT
COOKING
(NO COOKING)
1st. latch switches COM-NO
Closed
Open
2nd. latch switch
COM-NO
Closed
Open
Monitor switch
COM-NC
Open
Closed
Stop switch
COM-NO
Closed
Open
The circuits to the power transformer, fan motor, turn-
table motor and the oven lamp are cut off when the 1st.
latch switch, 2nd. latch switch, and stop switch are
made open.
6. MONITOR SWITCH CIRCUIT
The monitor switch is mechanically controlled by oven
door, and monitors the operation of the 1st and 2nd.
latch switches.
6-1 When the oven door is opened during or after the
cycle of a cooking program, the 1st. latch and stop
switch must open their contacts first. After that the
contacts (COM-NC) of the monitor switch can be
closed and the contacts (COM-NO) of the 2nd. latch
switch can be opened.
6-2. When the oven door is closed, the contacts (COM-
NC) of the monitor switch must be opened and the
contacts (COM-NO) of the 2nd. latch switch must be
closed. After that the contacts of the 1st. latch switch
and stop switch are closed.
6-3. When the oven door is opened and the contacts of the
1st and 2nd latch switches remain closed. The fuse
M8A will blow, because the monitor switch is closed
and a short circuit is caused.
MEDIUM HIGH, MEDIUM, MEDIUM LOW, LOW
COOKING
When the microwave oven is preset for variable cooking
power, rated voltage is supplied to the power transformer
intermittently within a 27-second time base through the
relay contact which is coupled with the current-limiting
relay. The following levels of microwave power are given.
SETTING;
NOTE: The ON/OFF time ratio does not exactly corre-
spond to the percentage of microwave power,
because approx. 2 seconds are needed for heat-
ing up the magnetron filament.
HIGH
27 sec. ON
MEDIUM HIGH
Approx. 70%
21 sec. ON
6 sec. OFF
12 sec. OFF
18 sec. OFF
22 sec. OFF
MEDIUM
Approx. 50%
15 sec. ON
MEDIUM LOW
Approx. 30%
9 sec. ON
LOW
Approx. 10%
5 sec. ON