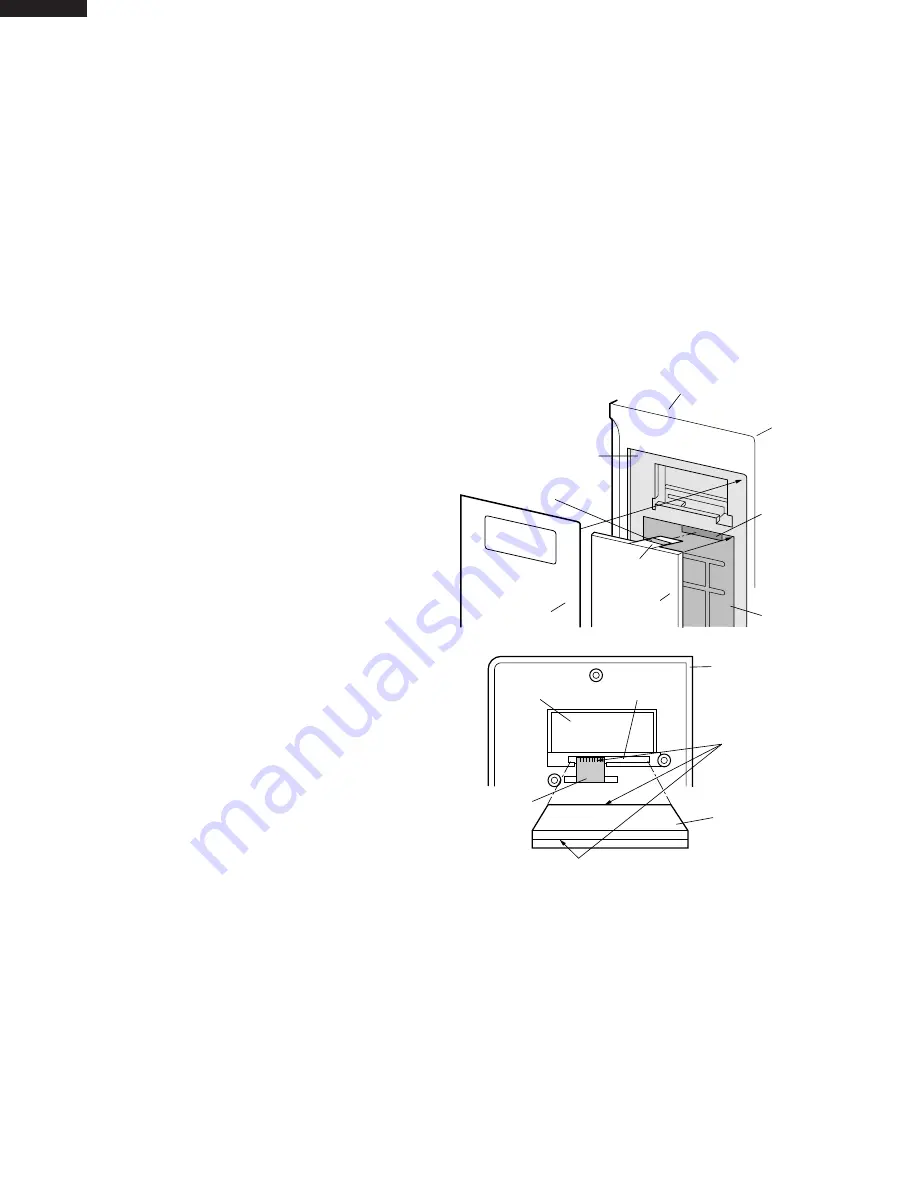
24
R-203HW
R-220HW
R-230HW
CONTROL PANEL ASSEMBLY REMOVAL
1. Disconnect the power supply cord and remove outer case.
2. Open the door and block it open.
3. Discharge high voltage capacitor.
4. Disconnect the leads from the control unit.
5. Remove the one (1) screw holding the control panel to
the front plate of the oven cavity.
6. Now, the control panel assembly is free.
Removal
1. Disconnect the power supply cord.
2. Remove the turntable and turntable support from the
oven cavity.
3. Turn the oven over.
4. Remove the one (1) screw holding the turntable motor
cover to the bottom plate.
5. Now, the turntable motor cover is free.
6. Disconnect the wire leads from the turntable motor.
TURNTABLE MOTOR REMOVAL
7. Remove the single (1) screw holding the turntable motor
to the oven cavity.
8. Remove the turntable motor from the oven cavity.
9. Remove the TTM packing from the turntable motor.
10.Now, the turntable motor is free.
Re-install
1. Re-install the TTM packing.
2. Re-install the turntable motor with theTTM packing with
the single (1) screw.
GRAPHIC SHEET AND MEMBRANE SWITCH REPLACEMENT
Removal
1. Disconnect the power supply cord and then remove
outer case.
2. Open the door and block it open.
3. Discharge high voltage capacitor.
4. Remove the control panel assembly, referring to chapter
of CONTROL PANEL ASSEMBLY REMOVAL.
5. Remove the three (3) screws holding the control unit to
the control panel frame. And remove the control unit.
6. Remove the rubber connector from the long slit on the
control panel frame.
7. Tear away the graphic sheet from the control panel
frame.
8. Tear away the membrane switch from the control panel
frame.
Installation
1. Remove remaining adhesive on the control panel frame
surfaces with a soft cloth soaked in alcohol.
2. Tear the backing paper from the new membrane switch.
3. Insert the ribbon cable of the membrane switch into the slit
of the control panel frame.
4. Adjust the upper edge and right edge of the membrane
switch to the small depression on the surface of the
control panel frame.
5. Attach the membrane switch to the control panel frame by
rubbing with a soft cloth not to scratch.
6. Tear the backing paper from the new graphic sheet.
7. Adjust the upper edge and right edge of the graphic sheet
to the large depression on the surface of the control
panel frame.
8. Attach the graphic sheet to the control panel frame by
rubbing with a soft cloth not to scratch.
9. Tear the small backing paper from the ribbon cable of the
membrane switch.
10. Attach the ribbon cable to the control panel frame rear
side.
11. Place the edge of the membrane switch’s ribbon cable
on the lower portion of the liquid crystal display.
12. Insert the rubber connector into the long slit on the
control panel frame.
13. Reinstall the control unit to the control panel frame with
the three (3) screws.
NOTE:
Do not contact the conductor portion of the ribbon
cable (edge) and the rubber connector directly with
your fingers. This is to avoid oxidized.
Figure C-2. Graphic Sheet and Membrane Switch
Replacement
Graphic sheet
Rubber connector
Conductor portions
Membrane
switch
Ribbon cable
of membrane
switch
Large depression
Small
depression
Small backing
paper
Ribbon
cable
Liquid crystal
display
Control panel frame
(Rear side)
Control panel frame
Long slit
Slit