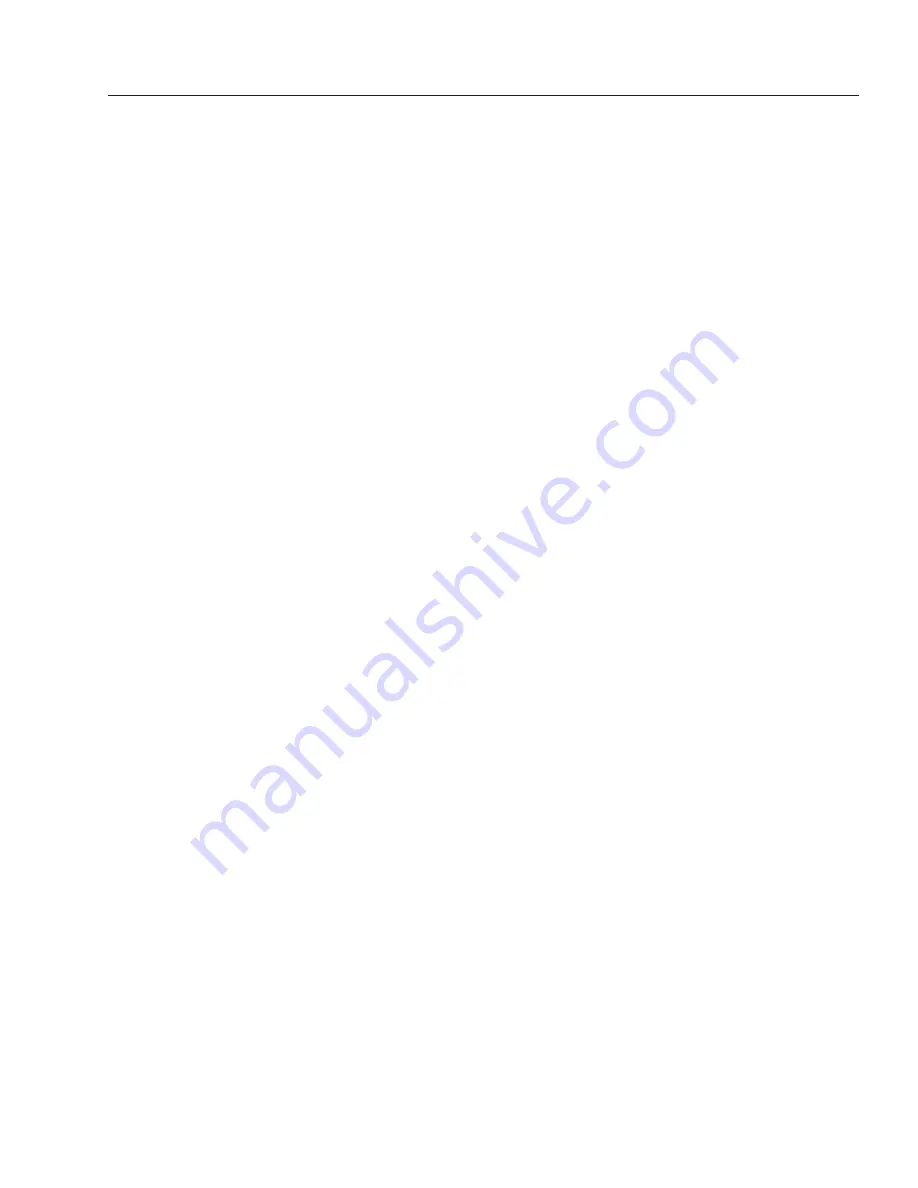
SSD DIESEL SERIES
OPERATOR’S MANUAL
9
SHARK SSD DIESEL
•
REV. 11/02
PREVENTATIVE MAINTENANCE
1. Check to see that water pump is properly lubricated.
2. Follow winterizing instructions to prevent freeze dam-
age to pump and coils.
3. Always neutralize and flush detergent from system
after use.
4. If water is known to have high mineral content, use a
water softener in your water system, or de-scale as
needed.
5. Do not allow acidic, caustic or abrasive fluids to be
pumped through system.
6. Always use high grade quality cleaning products.
7. Never run pump dry for extended periods of time.
8. Use clean fuel: kerosene, No. 1 fuel oil, or diesel. Clean
or replace fuel filter every 100 hours of operation. Avoid
water contaminated fuel as it will damage the fuel pump.
9. If machine is operated with smoky or eye burning
exhaust, coils will soot up, not letting water reach
maximum operating temperature.
10. Never allow water to be sprayed on or near the engine
or burner assembly or any electrical component.
11. Periodically delime coils as per instructions.
12. Check to see that engine is properly lubricated.
It is advisable, periodically, to visually inspect the burner.
Check air inlet to make sure it is not clogged or blocked.
Wipe off any oil spills and keep equipment clean and dry.
The flow of combustion and ventilating air to the burner
must not be blocked or obstructed in any manner.
The area around the TUFF washer should be kept clean
and free of combustible materials, gasoline and other
flammable vapors and liquids.
MAINTENANCE AND SERVICE
Unloader Valves:
Unloader valves are preset and tested at the factory be-
fore shipping. Occasional adjustment of the unloader may
be necessary to maintain correct pressure.
Winterizing Procedure:
Damage due to freezing is not covered by warranty. Ad-
here to the following cold weather procedures whenever
the washer must be stored or operated outdoors under
freezing conditions.
During winter months, when temperatures drop below
32°F, protecting your machine against freezing is nec-
essary. Store the machine in a heated room. If this is not
possible then mix a 50/50 solution of anti-freeze and
water in the float tank. Turn the engine on to siphon the
anti-freeze mixture through the machine. If compressed
air is available, an air fitting can be screwed into the float
tank by removing the float tank strainer and fitting. Then
inject the compressed air. Water will be blown out of the
machine when the trigger on the spray gun is opened.
High Limit Hot Water Thermostat:
For safety, each machine is equipped with a temperature
sensitive high limit control switch. In the event that the wa-
ter should exceed its operating temperature, the high limit
control will turn the burner off until the water cools, then it
will automatically reset itself. The thermostat sensor is lo-
cated on the discharge side of the heating coil. The ther-
mostat control dial is located on the control panel.
Pumps:
Use only SAE 30 weight non-detergent oil. Change oil
after first 50 hours of use. Thereafter, change oil every
three months or at 500 hour intervals. Oil level should be
checked through use of dipstick found on top of pump,
or the red dot visible through the oil gauge window. Oil
should be maintained at that level.
Cleaning of Coils:
In alkaline water areas, lime deposits can accumulate
rapidly inside the heating coil. This growth is increased
by the extreme heat build up in the coil. The best preven-
tative for liming conditions is to use high quality cleaning
detergents. In areas where alkaline water is an extreme
problem, periodic use of Deliming Powder (Part
#9-028008) will remove lime and other deposits before
coil becomes plugged. (See Deliming instructions for use
of Deliming Powder.)
Deliming Coils:
Periodic flushing of coils or optional float tank is recommended.
Step 1 Fill a container with 4 gallons of water, then add
1 lb. of deliming powder. Mix thoroughly. Pour
mixture into float tank.
Step 2 Remove wand assembly from spray gun and put
spray gun into float tank. Secure the trigger on
the spray gun into the open position.
Step 3 Turn engine on, allowing solution to be pumped
through coils back into the float tank. The solu-
tion should be allowed to circulate 2-4 hours or
until the color changes.
Step 4 After circulating solution, flush the entire sys-
tem with fresh water. Clean out float tank and
then reinstall wand assembly to spray gun.
Removal of Soot from Heating Coil:
In the heating process, fuel residue in the form of soot
deposits may develop between the heating coil pipes,
and block air flow which will affect burner combustion.
When soot has been detected on visual observation, the
soot on the coil must be washed off after following the
coil removal steps (See Coil Removal on page 11).