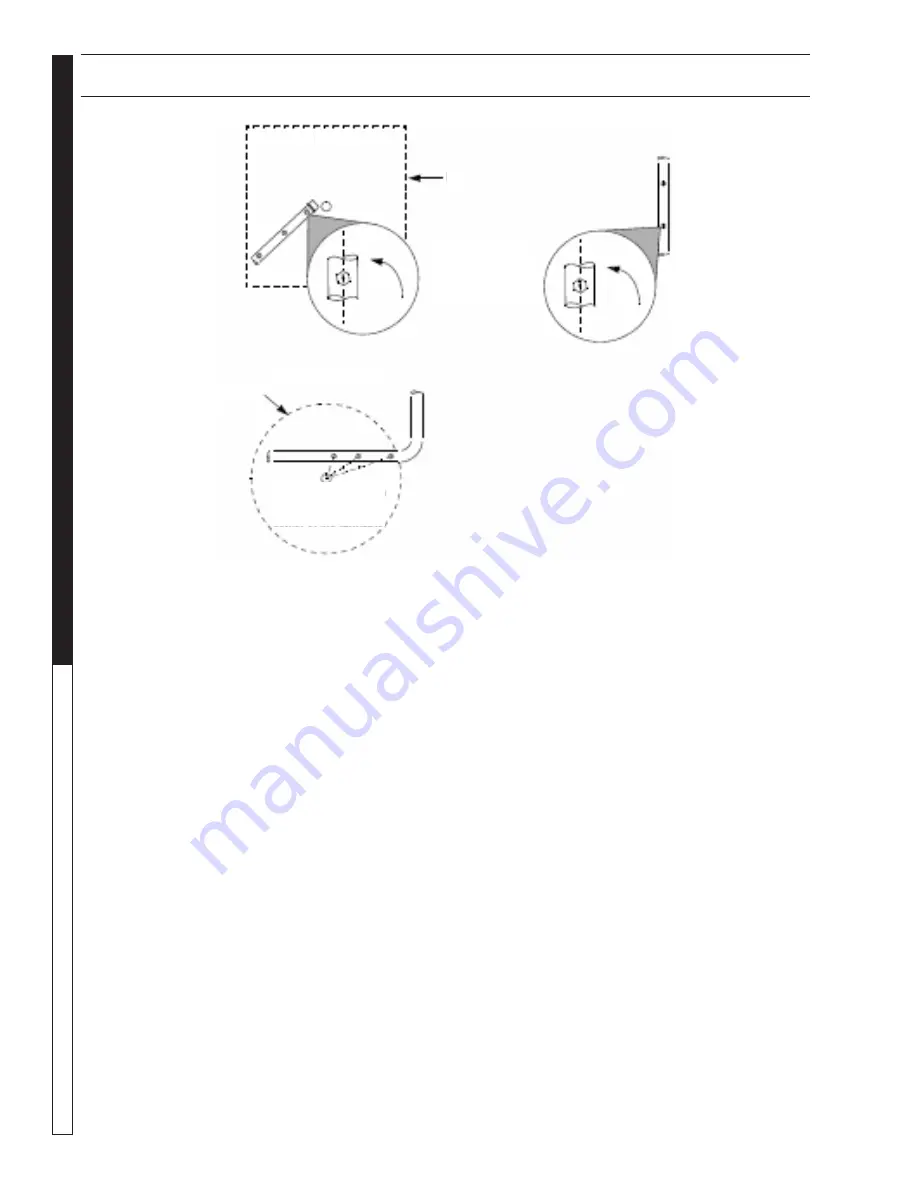
SHARK SC-2412 • 97-6267 • REV. 3/04
A
U
T
OMA
TIC P
A
R
TS
W
ASHER Maintenance Guide
20
Cleaning and Aligning the Spray Nozzles
To ensure optimum cleaning performance, it is impor-
tant that you examine the spray nozzles periodically and
clean and align them if necessary.
To clean a plugged nozzle, remove it from the spray
pipe and use a small wire brush to free the nozzle of
any obstructions. When you replace the nozzle on the
spray pipe, make sure you align it according to Figure
Above to maintain a proper spray pattern.
Note: The spray nozzles are sized and positioned to
optimize the distribution of cleaning solution in the wash
chamber. If you remove the nozzles make sure you re-
place them in the correct position on the appropriate
pipe. Spray nozzle specifications are stamped on the
face of each nozzle, as shown above.
Cleaning out the Sump
Step 1:
Remove oil from the cleaning solution using the DOS
System (See
Using the DOS System).
Step 2:
Remove the debris screen.
Step 3:
Drain the wash solution from the sump chamber. To drain
the solution either use the sump drain or a small sub-
mersible pump.
Section 5: Maintenance and Repair
TOP NOZZLES
SIDE NOZZLES
Align the notch in
each spray nozzle
with the center of the
turntable
Rotate each nozzle
approximately 3°
from the centerline of
the pipe
BOTTOM NOZZLES
Turntable
SIDE NOZZLES
Note: Manufacturer recommends that you reuse the
wash solution. To do so, transfer it to a suitable holding
container (such as a 55-gallon drum) while you clean
out the sump chamber.
Step 4:
Remove sand and other debris from the bottom of the
sump chamber. To remove the debris either flush it out
through the sump drain, or vacuum it out using a wet/
dry vac. Dispose of the debris in accordance with appli-
cable local, state, and federal regulations.
Note: Take special care to ensure that the heating ele-
ment and the low-water float are free of debris. A build
up of debris around the heating element will decrease
heating performance and may cause the element to
overheat and fail. A build up of debris around the float
may cause the low water shut-off system to malfunc-
tion (See
Low Water Shutoff System)
Step 5:
Transfer the wash solution back to the sump chamber,
and add fresh water if necessary.
Step 6:
Replace the debris screen.
Step 7:
Heat the wash water to operating temperature, then add
appropriate amount of factory detergent.
Step 8:
Run the machine through a 15-minute wash cycle.
3°
3°
Lid