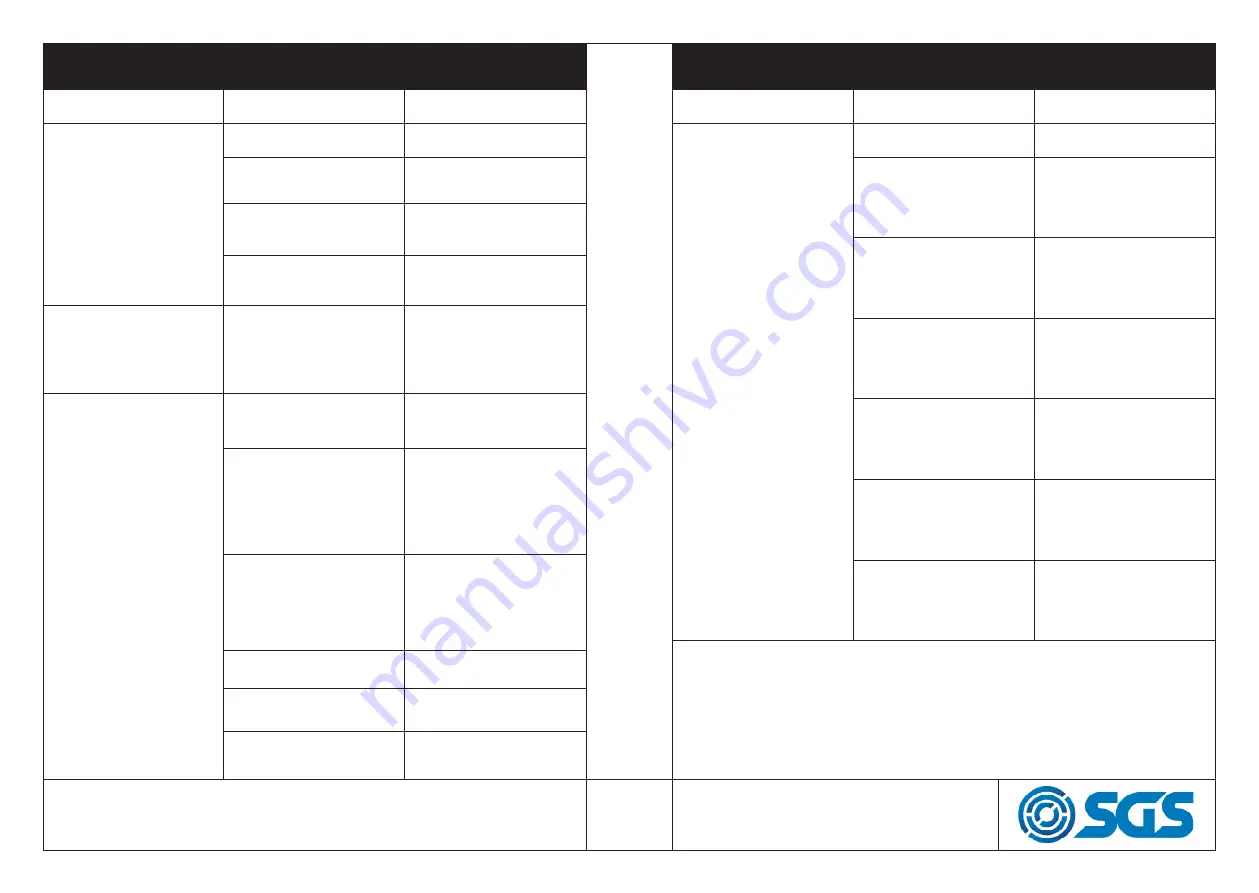
PAGE 15
PAGE 14
TROUBLESHOOTING
STORAGE & HANDLING
PROBLEM
CAUSE
SOLUTION
Engine fails to start
Lack of fuel in tank.
Fill tank as necessary.
No fuel reaching carbu-
retor.
Fuel cock isolated. Turn
on fuel shut-off valve.
Engine switch is in the
OFF position.
Set engine switch to the
ON position.
Lack of spark at the
spark plug.
Lack of spark at the
spark plug.
Engine stops and will
not restart
Lack of oil in engine
causing ‘Low Oil Pro-
tection’ sensor to stop
engine from running.
Fill oil reservoir as neces-
sary.
Pump fails to prime
Priming chamber not
filled correctly.
Fill priming chamber
leaving no air gap.
Air leaks through the
suction line joints (dam-
aged hose, broken hose
clamps, broken / ill-
fitting gasket).
Carry out repairs as
necessary/check, repair
connections as required.
Blocked inlet hose.
Clean strainer & ensure
it is not submerged in
mud or sediment etc.
Ensure there are no kinks
in delivery hose.
Engine speed too low.
Increase engine speed.
Damaged impeller.
Renew impeller after
dismantling pump.
Air leaks through dam-
aged seal.
Renew seal.
PROBLEM
CAUSE
SOLUTION
Low output from pump
Engine speed too low
Increase engine speed.
Impeller clogged
Clean strainer and en-
sure it is not submerged
in mud or sediment etc.
Suction or delivery line
obstructed
Remove obstruction and
ensure there are no kinks
in delivery line.
High friction losses in
the suction line
Avoid un-necessary
curves, restrictions or
valves.
Suction lift too high
Set pump as close as
possible to the level of
the liquid to be pumped.
Congested material
inside pump
Dismantle pump & clean
out.
Damaged impeller
Dismantle pump and
renew impeller.
WWW.SGS-ENGINEERING.COM