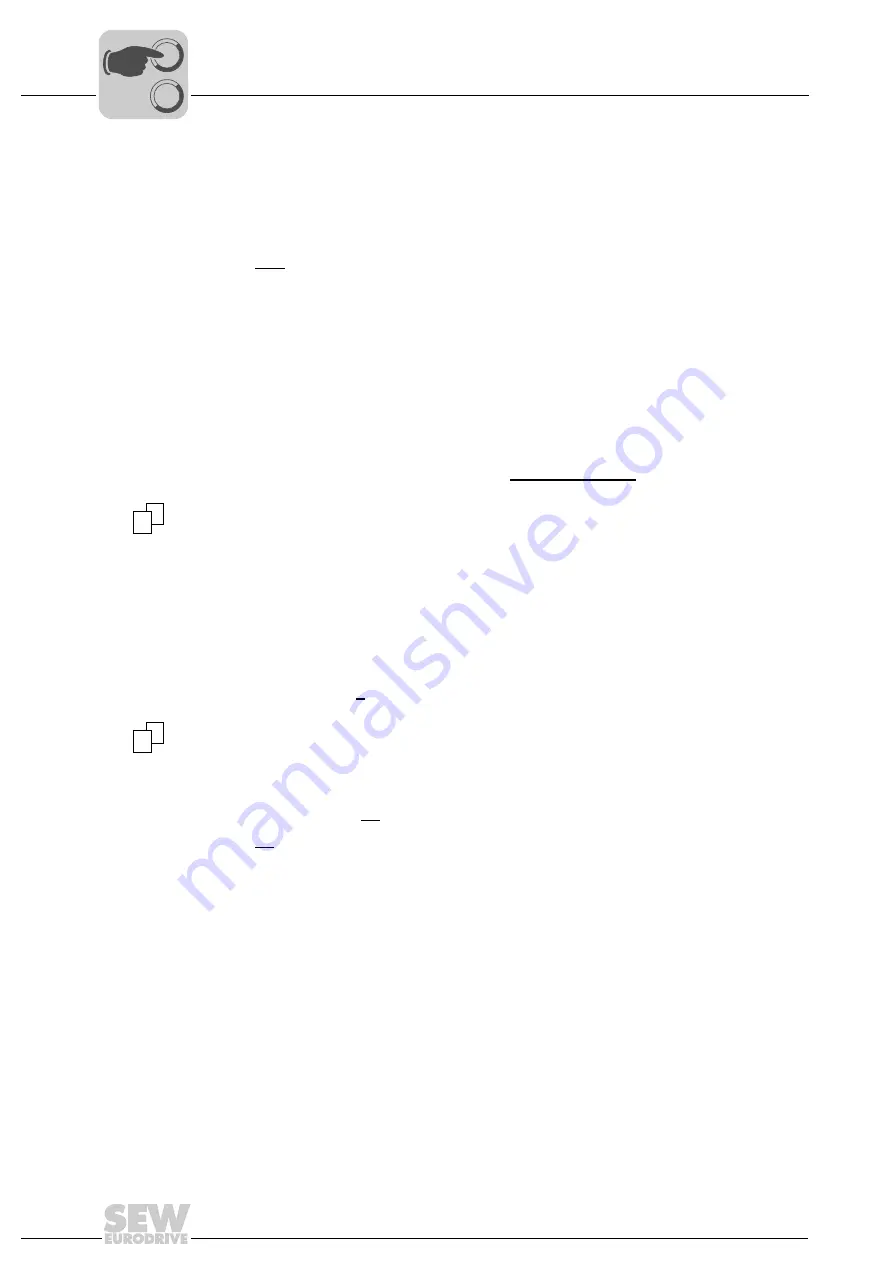
104
Manual – MOVIPRO® SDC with DeviceNet Interface
10
Explanation of the parameters
Parameterization of MOVIPRO
®
is connected properly and the reference point and travel positions are defined cor-
rectly when using this parameter.
NOTE:
Altering the "Direction of rotation reversal" parameter after the system has
been referenced causes the system to lose its reference point for the absolute posi-
tion. The result may be undesirable travel movements of the axis.
• OFF: The SEW definition applies.
10.4.6 P5xx Monitoring functions
The following monitoring functions have been implemented to monitor what happens to
drive-specific parameters in the specific application and to be able to react in case of
impermissible deviations. Some of the monitoring functions are available separately in
both parameter sets. The response to the control functions can be set with
P83x Fault
responses
(page 117).
P50x Speed monitoring
P500/P502 Speed
monitoring 1/2
Setting range: Off / motor / regenerative / motor/regenerative
The speed required by the setpoint can only be achieved if there is sufficient torque
available to meet the load requirements. Once
P303/P313 Current limit 1/2
(page 99)
and the external current limit have been reached, the power section assumes that the
torque has reached its maximum and the desired speed cannot be attained. Speed mon-
itoring is triggered if this situation persists for the duration specified in
P501/P503 Delay
time 1/2
(page 104).
Activate the speed monitoring for hoists and set the delay time to a rather small value.
Speed monitoring is not that important for safety since an incorrect movement of the
hoist does not necessarily mean operation in the current limitation.
P501/P503 Delay
time 1/2
Setting range: 0 – 1 – 10 s
The set current limit can be reached briefly during acceleration, deceleration, or load
peaks. You can prevent the speed monitoring from responding too sensitively by setting
the delay time accordingly. The current limit must be reached permanently for the dura-
tion of the delay time before monitoring responds.
P504 Encoder
monitoring motor
Setting range: Yes/No
• No: An open circuit between frequency inverter and motor encoder is not directly
detected. In case of a defective connection, error "A1.F08" (speed monitoring) will be
issued in enabled state unless it was deactivated.
• Yes: An open circuit between frequency inverter and motor encoder will be directly
detected when using sin/cos encoders and TTL encoders. The error message
"A1.F14" (encoder) will be issued in case of an error. This error will also be generated
in inhibited state.
NOTE:
Encoder monitoring is not a safety function! If you use a HIPERFACE
®
en-
coder, encoder monitoring (also for the track) is always active independent of the set-
ting in P504.
1
2
1
2
0
0
I