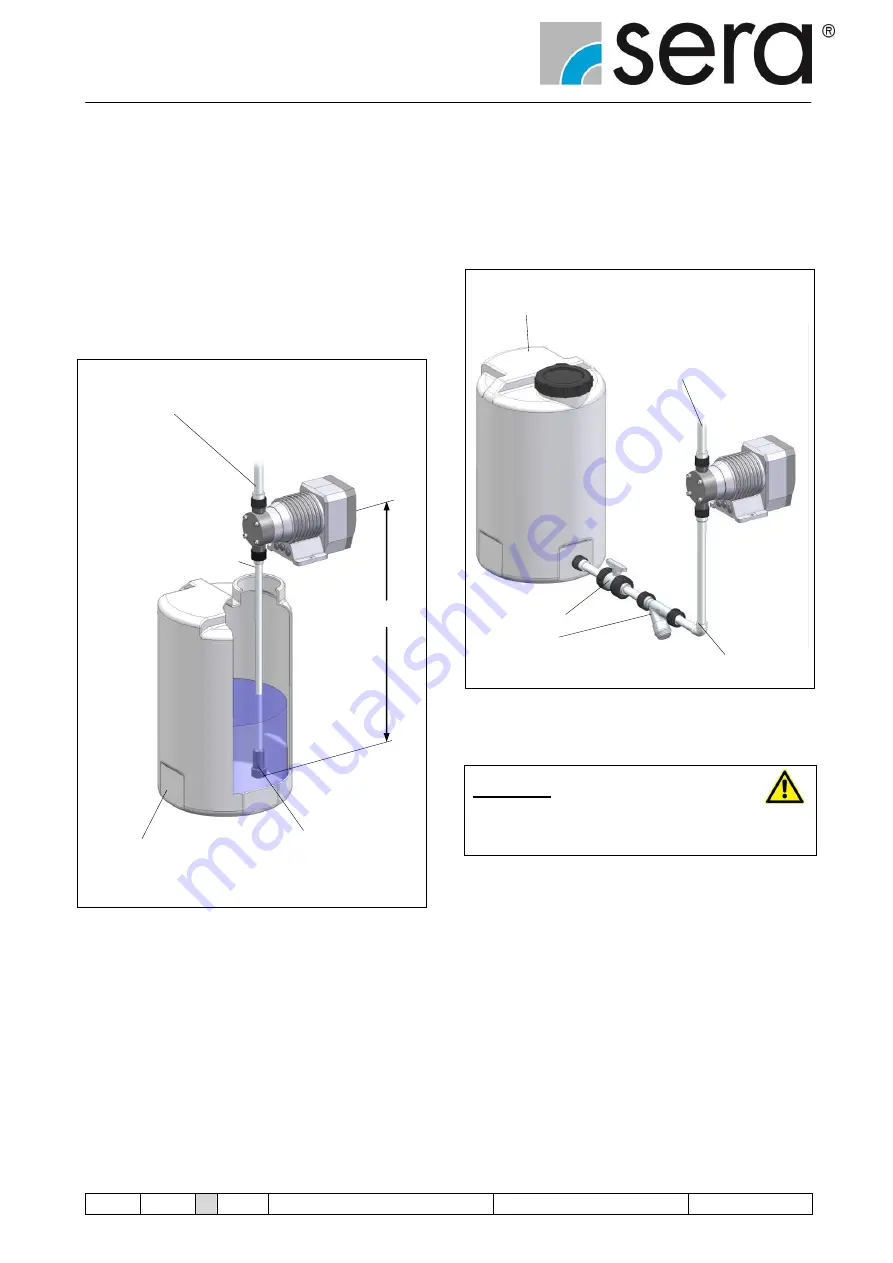
Solenoid diaphragm pump
Series R/RS 204.1
Operating Instructions
TA 416
Rev.
11 en
04/2013
Subject to technical modifications!
www.sera-web.com
25
8.1.6
How to avoid an emptying of the
suction line
Install a foot valve at the end of the suction line.
Based o
n calculations, the dimension ‘
H
’ may not exceed the
number that is equal to the specified maximum suction height
of the pump divided by the density of the pumped medium and
under consideration of mass accelearation and viscosity of the
medium.
Pressure line
Suction lance / Suction line
H
Foot valve
Container
Fig. 22 Avoiding an emptying of the suction line
8.1.7
Line strainer
Connect the suction line slightly above the bottom of the tank
and install a line strainer (
≤
0,1mm
– aperture size – depend-
ing on nominal width of the valve).
Container
Pressure line
Shut-off valve
Line strainer
Suction line
Fig. 23 Installing a line strainer
CAUTION !
If contaminations are not removed this may result in mal-
functions of the pump and the system.