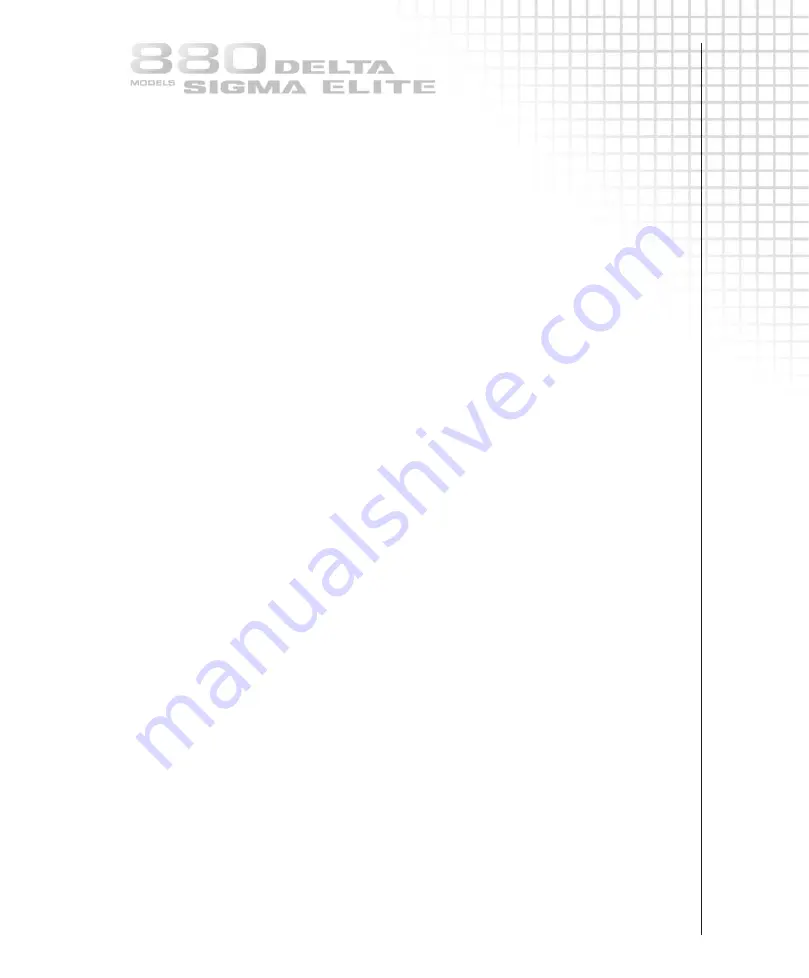
4
.1
MAINTENANCE INSTRUCTIONS
QCP386 issue 2
Quarterly (routine) and annual (complete) maintenance requirements
Radiographic exposure devices and associated equipment must be maintained regularly by
trained and qualified personnel to ensure consistent and safe operation of the radiographic
system. The routine inspection and maintenance also ensures the integrity of the Type B(U)
transport packages are maintained in compliance with the Type B(U) package, Certification
Number USA/9296/B(U)-XX (for XX, enter either 85 or 96 according to the package certification).
Manufacturers base the recommended inspection and maintenance requirements on the
system's design, application, materials, anticipated work cycles, environmental factors of use
under the normal and abnormal conditions of industrial radiography and while in the
transport system. A program of systematic maintenance will prolong the working life of the
radiographic exposure device and associated equipment in addition to ensuring safety
during use. By most national regulations, routine maintenance of the systems is required at
intervals not to exceed 3 months in addition to the radiographer's daily inspections for
obvious defects. The complete annual servicing ensures the integrity of the system.
Maintenance program administrators must recognize the need for maintenance intervals
that are less than the required 3 month interval especially in cases where the systems are
used in severe environmental conditions. Maintenance program administrators must ensure
the systems are completely serviced immediately after certain jobs in severe conditions.
Extreme or severe conditions may include, but is not limited to:
G
Conditions where the equipment was immersed in water or mud.
G
Subjected to high-concentrations of particulate such as fly ash or sand.
G
Subjected to hot radiography conditions.
G
Subjected to salt-water conditions, caustic or acidic materials.
G
Subjected to accidental drops or falling objects.
G
Whenever subjected to extreme environmental conditions.
The routine maintenance performed every 3 months requires partial disassembly, cleaning,
inspection, re-lubrication and operational checks of the system. The complete maintenance
(performed once a year) involves a complete disassembly, cleaning, inspection, re-lubrication
and operational tests of the entire system.
Equipment maintenance can be performed by trained and qualified individuals within the
licensee's organization. AEA Technology QSA service engineers are available to provide
maintenance on the systems at the licensee's premises or at one of the service centers.
Routine (quarterly) maintenance requirements
1 Remote controls
Disassemble, clean, inspect and maintain the remote control crank, control conduits and
control cable according to the complete service section. Record the results of the inspection
and any repairs that are performed. Any components found to be deficient during the
inspection must be removed from service until repaired or replaced. Deficient components
must be labeled with a status indicator to prevent inadvertent use.
2 Source guide tubes
Clean and inspect the source guide tubes in accordance to the complete service section.
Record the results of the inspection and any repairs that are performed. All source guide
tubes found to be deficient during this inspection must be removed from service and
sent to a service center for repairs. Deficient components must be tagged with a status
indicator to prevent inadvertent use.
3 Radiographic exposure device
Clean and inspect the exposure device for wear and obvious damage. Record any defects
that might affect safe operation of the exposure device. If deficiencies are found during this