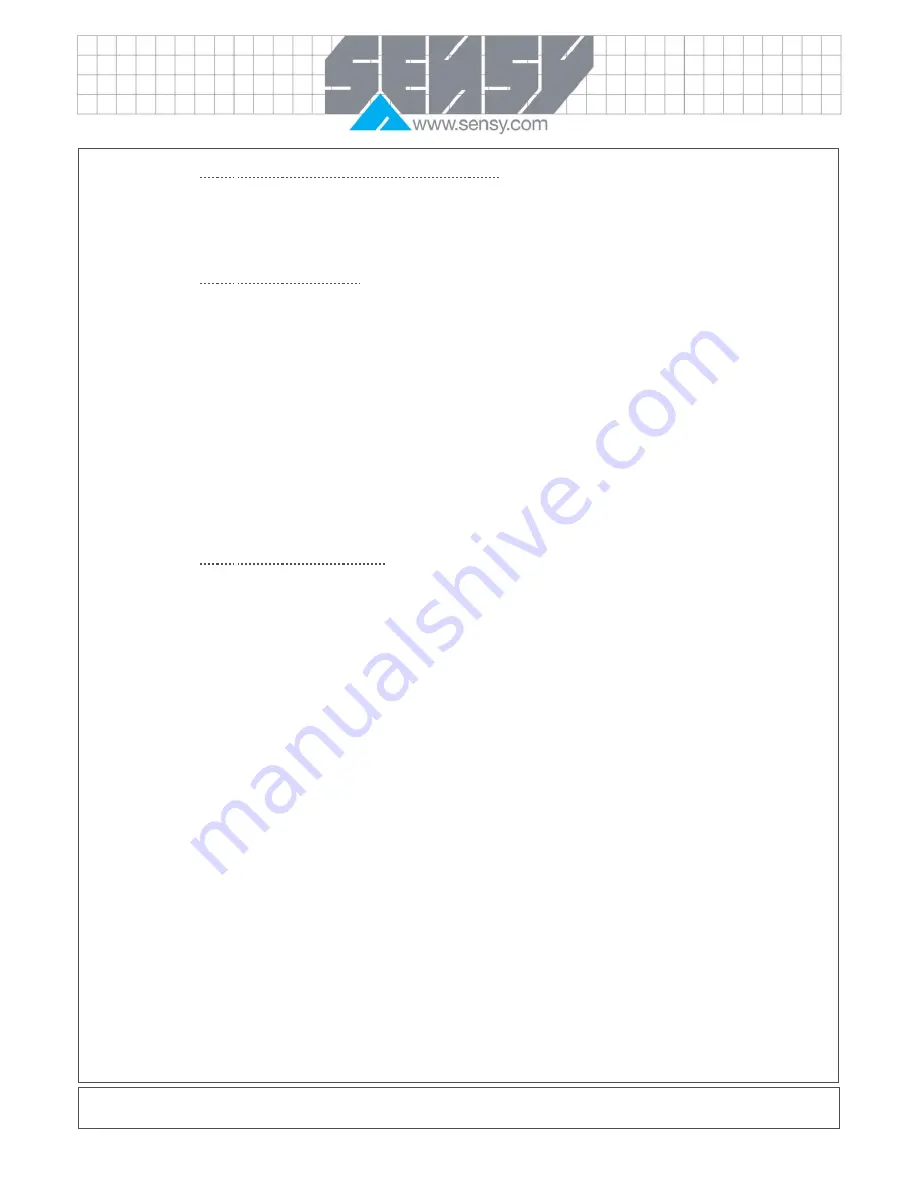
MA-CRANE-BOY_EN
Page 7 on 10
Rev: 11/01/2012
2.3.2.
Overload, slack cable and load verification
To verify the overload, first overload and then check that the SP2 relay opens and that lifting is prohibited.
Check that the SP3 relay opens in a slack cable situation and that lowering is prohibited.
Check that the values displayed match the actual values of the loads being handled.
2.3.3.
Periodic verification
In compliance with the legislation in force, the lifting force limiter must be regularly checked during periodic
inspections.
This inspection includes a functional test for the triggering limit and the correct condition of the sub-assembly
along with the connections and links. The inspection must be carried out when the equipment is commissioned
then, unless indicated otherwise, at least once a year.
To check the operation of the SP2 overload triggering relay and the display, a test button (*) is fitted on the
load limiter, which destabilises the signal from the force transducer and simulates an overload.
The display offset generated by this test button must be identical to the offset that was obtained when the
equipment was installed and recorded on the calibration sheet.
(*) Push-button in the OEM version: connect the special push-button supplied by SENSY between the
and power terminals (green and brown transducer wires, respectively as standard wire colours).
2.3.4.
Peak values registration
Pushing on the DSP key will allow you to visualise the MIN and MAX values the system has recorded while in
operation since the last maintenance check.
In this case, the red LEDS MAX or MIN are “ON” (on the left-hand side of the control panel).
During normal operation (load indication), those LEDS on the left-hand side of the front panel should be off.
CAUTION: using these MIN and MAX values only make sense if you have reset the recorded values by using
the F1 key after the first operation tests and after any subsequent overload simulation by means of the test
button !