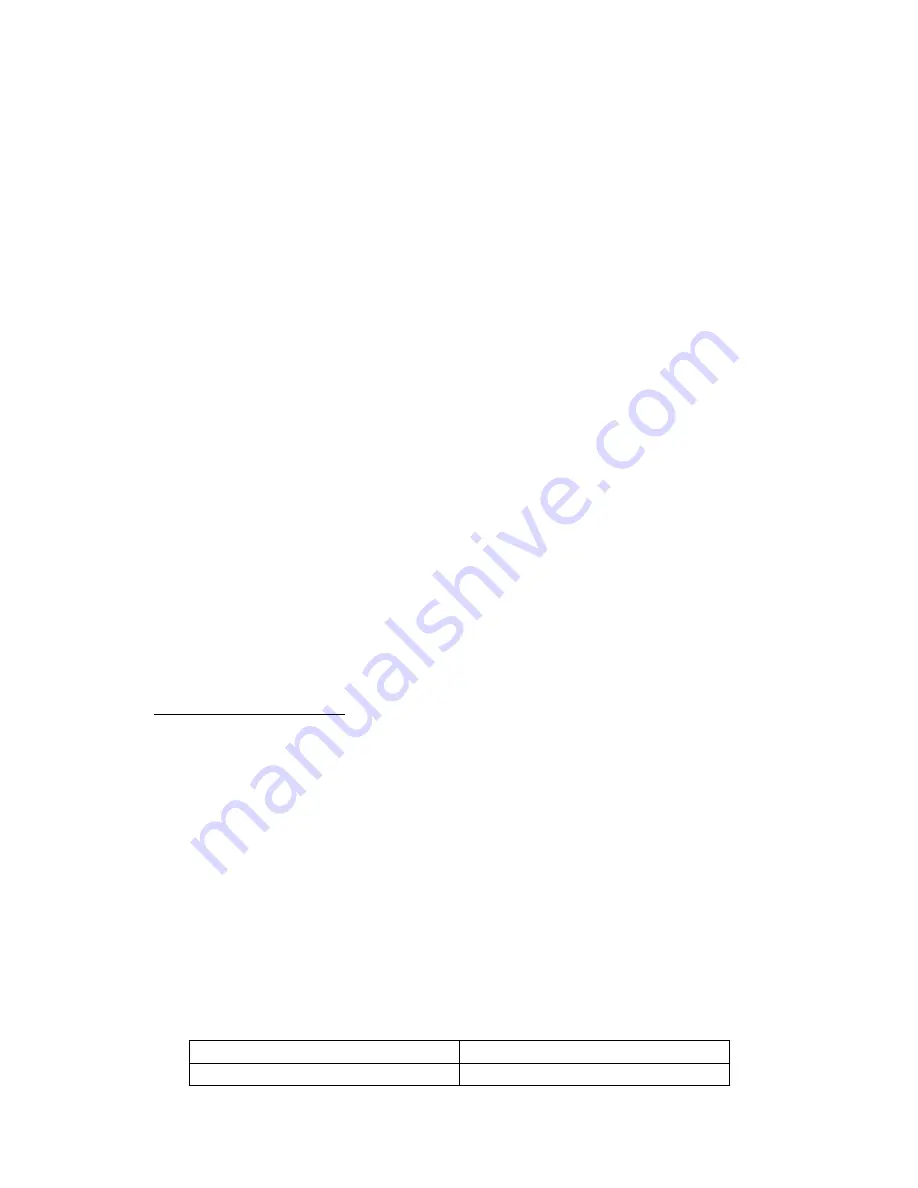
3
Application Information
Polyflue™ Gas Vent Systems may be used to vent safety certified Category II, IV and Certain Direct Vent gas
appliances with a flue gas temperature of not more than 230°F (110°C). Polyflue can also be used to vent
category II, IV gas fired appliances, when used as a re-liner for an unused existing masonry chimney liner or
unused existing Type B Gas Vent. The Polyflue system is for use with appliances which produce positive vent
pressures of 15” w.c. (3733 Pa) or less. Because these types of appliances may produce vent gases under
positive pressure and/or at or near their dew point, special installation considerations may be required.
Install in accordance with these instructions and those of the appliance manufacturer. Consult the appliance
manufacturer’s instructions for the maximum horizontal length of the vent connector as well as any restriction on
total vent height, proper sizing of the vent, common venting considerations and procedures for connecting the
vent to the appliance.
The installation must conform to applicable National, Regional, State and local codes. Contact the Authority
Having Jurisdiction prior to beginning any work to obtain any required permits.
Pre-Installation Considerations
Proper planning prior to installation is essential. T
he authority having jurisdiction (such as gas inspection
authority, municipal building department, fire department, fire prevention bureau, etc.) should be consulted before
installation to determine the need to obtain a permit.
A continuous straight-line
upward
pitch of minimum 3/8” rise per foot (31mm / 1000mm) (2
°
) on horizontal runs
must be maintained in order to properly rid the system of the flue gas condensate via the appliance drain, inline
drains, or drain tee caps.
Terminations must comply with the requirements USA Natural Gas & Propane Codes (NFPA 54 / ANSI Z223.1).
In Canada,
shall terminate in accordance with the requirements of CAN/CSA-B149.1, Natural Gas and Propane
Installation Code, or CAN/CSA-B149.2, Propane Storage and Handling Code, as applicable.
Plastic venting systems shall not pass through rated fire separations
Be sure to plan a sufficient number of supports for the entire system to maintain the required straight-line pitch
and to hold the system in place. Where the vent is enclosed within a chase, the enclosures should be built to
permit future inspection of the system.
Reference
Combustion & Ventilation Air
on the last page for proper air supply guidelines
Safety
Wear eye protection and heavy gloves throughout the installation. In addition, wear an approved dust and vapor
respirator whenever in contact with building insulation. Proper and safe scaffolding and/or ladders should be
used. Check overhead for antennas, power lines or other obstacles before erecting ladders or scaffolding and
while working with conduit on any roof structure.
The safe operation of a system is based on the use of parts supplied by the manufacturer and the performance of
the system may be affected if the combination of these parts is not used in actual building construction
Tools Required for Installation
Common building tools including but not limited to a Tape Measure, Pliers, Screw Drivers, Saws and/or Snips,
Drills, Drop Cloth(s); Ladder/Scaffold; Safety and Personal Protective Clothing.
Clearance to Combustibles
Polyflue single wall rigid and flexible pipe has zero clearance to combustibles for flue gases not exceeding 230
°
F
(110
°
C) and can be fully enclosed within combustible construction.
Maximum Flue Temperature
Clearances to Combustibles
230
°
F( 110
°
C)
0” (0mm) for all orientations & fully enclosed
Summary of Contents for Polyflue BH
Page 16: ...16 NOTES ...