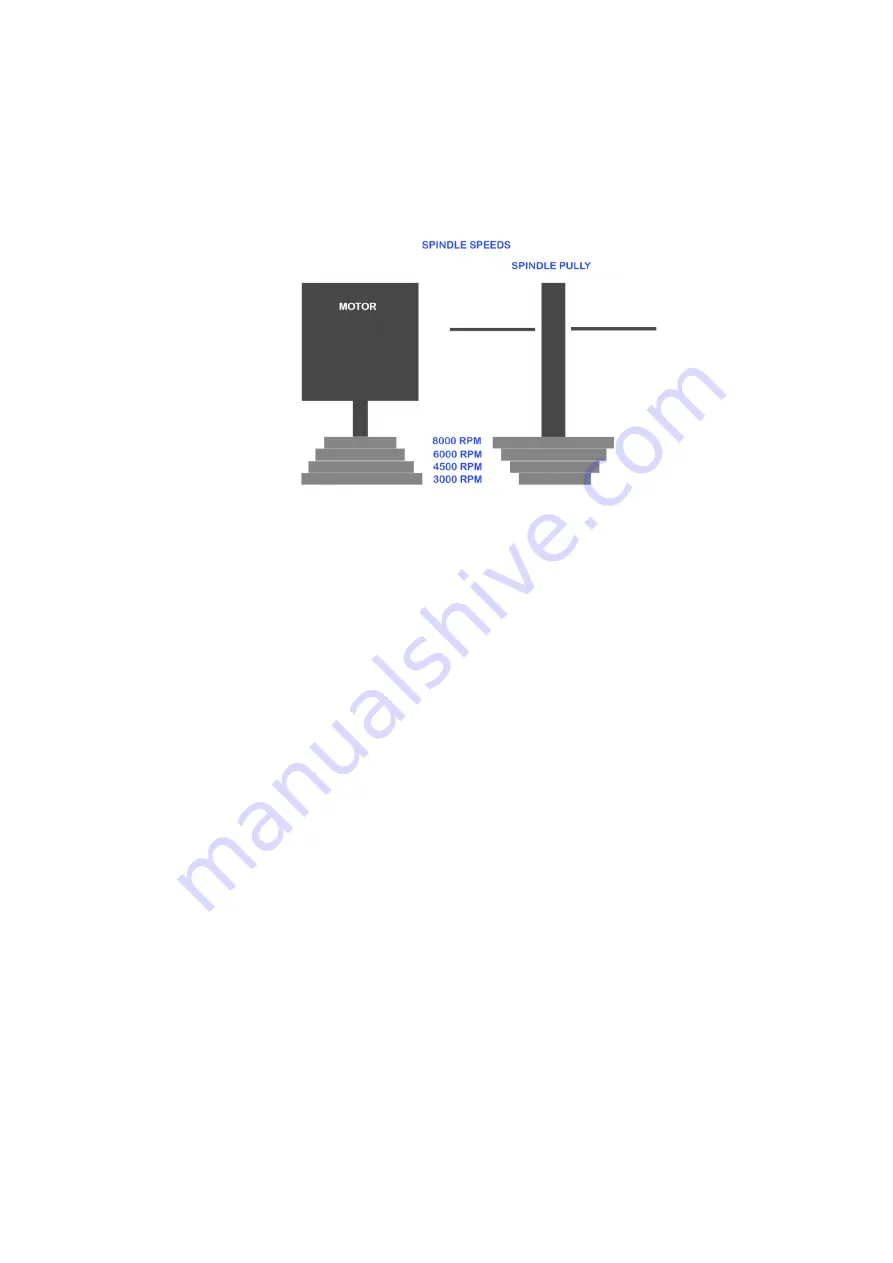
SM210 Operation/Maintenance Instructions Page 16 of 29
The motor is foot mounted to a hinged platform, which is adjustable for position along a
slotted shaft in which the locking lever runs. To change the selected speed the lever must be
unlocked, and the motor plate pulled forward to release the tension on the drive belt. The
poly-vee belt may then be relocated on the pulleys, the motor plate pushed away to re-
tension the belt, and the lever re-locked. Always ensure that the belt is fully engaged within
the full set of grooves for each speed setting on both motor and spindle pulleys before
starting the machine.
7.0 Tool Selection
Only tools conforming to EN847-1:1997 and marked MAN should be fitted to this machine
(refer to manufacturer’s sales literature).
Only use tooling with the manual feed cutter block
s usually mark with ‘MAN’.
LIMITED CUTTER PROJECTION TOOLING
Where possible,
always
use limited cutter projection tooling.
The following information is cont
ained in the HSE Information Sheet ‘PUWER 98: Selection of
tooling for use with hand-fed woodworking
machines’:
Limited cutter projection tooling (sometimes referred to as chip thickness limitation
tooling) significantly reduces:
● the severity of i
njury
if a machine operator’s fingers contact the rotating tool;
● the risk of workpiece kickback.
Most ac
cidents at woodworking machines are due to the operator’s hands or fingers
encountering the rotating cutters. Amputation usually results. Between 1993 and 1996
there were 165 injuries (amputations and severe lacerations) at machines where
limited cutter projection tooling could have been fitted. It is estimated that limited
cutter projection tooling would have reduced the seriousness of injury in 90% of these
accidents. By reducing the risk of kickback, this type of tooling can also help prevent
many other serious injuries.
Summary of Contents for SM210
Page 11: ...SM210 Operation Maintenance Instructions Page 11 of 29 4 1 Three Phase Wiring Diagram ...
Page 12: ...SM210 Operation Maintenance Instructions Page 12 of 29 4 2 Single Phase Wiring Diagram ...
Page 28: ...SM210 Operation Maintenance Instructions Page 28 of 29 ...
Page 29: ...SM210 Operation Maintenance Instructions Page 29 of 29 ...