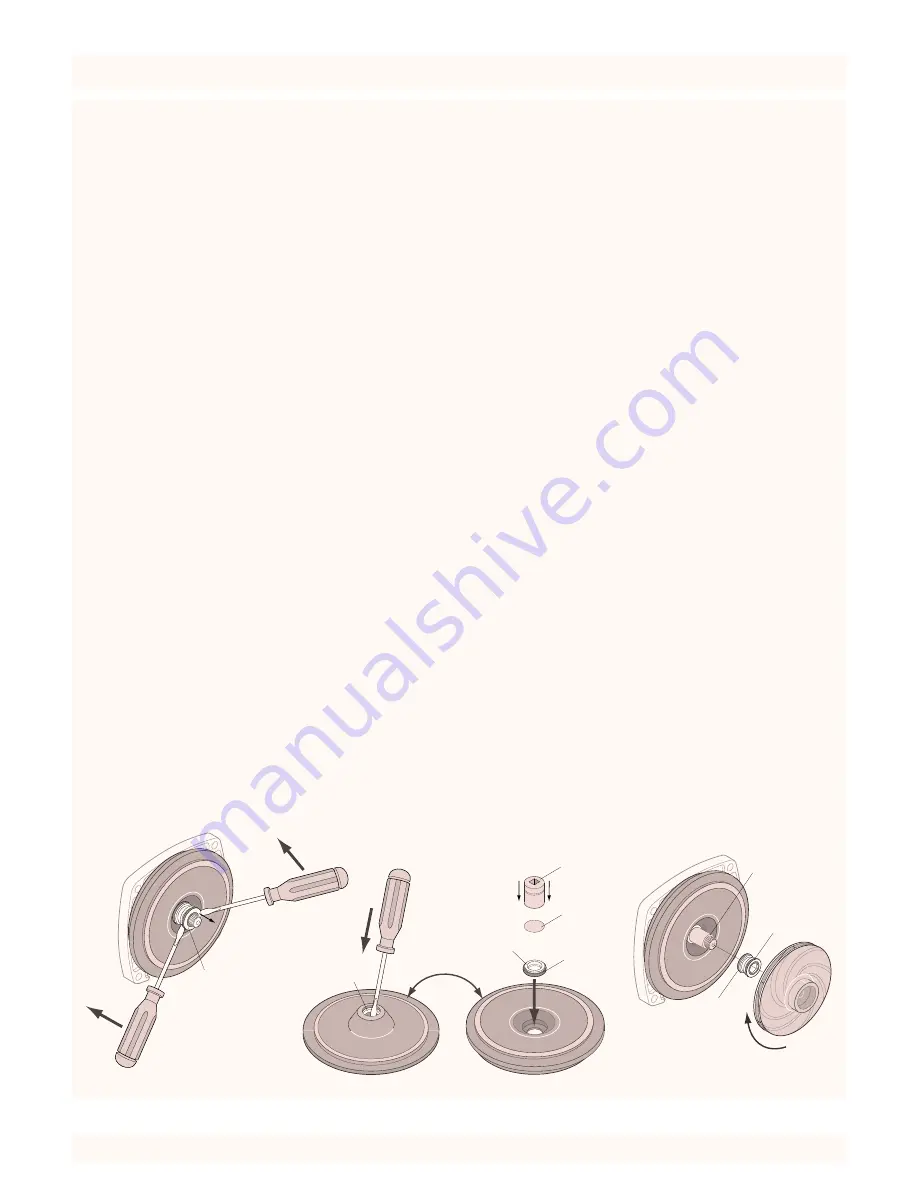
MAINTENANCE
Lubrication
It is not necessary to lubricate the pump or its motor.
The motor has two ball bearings lubricated for life. The
mechanical shaft seal in the pump is water lubricated
and self-adjusting.
Draining for Winter
When the pump is to be disconnected from service, or
is in danger of freezing, it should be drained.
Turn power to pump OFF. Remove the priming plug to
vent the pump. Drain the pressure tank. Drain all pip-
ing to a point below the freeze line.
To drain an air volume control, remove AVC tubing and
turn (loosen) it 180° on the 1/4” pipe fitting in the
tank. This will permit any water remaining in the air
volume control to drain back into the tank.
To drain pressure tank, remove plug, piping or hose at
lowest point in the tank.
The Shaft Seal
The pump is designed for ease of servicing. Should re-
pair or replacement of the motor or seal be needed, the
pump and piping do not need to be disconnected or
disturbed.
If it is necessary to repair or replace the motor, it is a
good idea to replace the seal plate gasket and the shaft
seal, Key Nos. 4 and 5 of pump drawings, Page 10.
Therefore, we suggest that you order these two items
to have on hand for future use.
The seal consists of primarily two parts; a rotating half
and a ceramic seat.
NOTICE:
The highly polished and lapped faces of the
seal are easily damaged. Read the instructions thor-
oughly and handle the seal with care.
1. Disconnect electric service (pull switch), and dis-
connect wiring to pump. Disconnect pressure
switch tube.
2. Remove capscrews holding motor to pump body.
Motor with impeller and diffuser can now be re-
moved.
3. Carefully tap diffuser to remove from seal plate.
4. Remove canopy from end of motor.
5. Partially unscrew capacitor clamp; move capacitor
to one side.
6. Hold motor shaft with 7/16” wrench on the flats on
the motor shaft and unscrew impeller.
Removal of Old Seal
1. After unscrewing impeller, carefully remove rotat-
ing part of seal by prying up on sealing washer,
using two screwdrivers (see Figure 5A). Use care
not to scratch motor shaft.
2. Remove seal plate from motor and place on flat sur-
face, face down. Use a screwdriver to push ceramic
seat out from seal cavity (see Figure 5B).
Installation of Floating Seat
(Figure 5C)
1. Clean polished surface of floating seat with clean
cloth.
2. Turn seal plate over so seal cavity is up. Clean cav-
ity thoroughly.
3. Lubricate outside rubber surface of ceramic seat
with soapy water and press firmly into seal cavity
with finger pressure. If seal will not locate properly
in this manner, place cardboard washer over pol-
ished face of seat and press into seal cavity using a
3/4” socket or 3/4” piece of standard pipe.
4.
DISPOSE OF CARDBOARD WASHER.
Be sure
polished surface of seat is free of dirt and has not
been damaged by insertion. Remove excess soapy
water.
Installation of Rotating Part of Seal Unit
(Figure 5D)
1. Reinstall seal plate using extreme caution not to
nick or scratch ceramic portion of seal on motor
shaft.
2. Inspect shaft to make sure that it is clean.
3. Clean face of sealing washer with clean cloth.
7
Seal Plate
Mechanical seal
rotating half
Mechanical seal
ceramic seat
A-Seal removal-rotating half
B-Seal removal-ceramic seat
C
-
Ceramic seat installation
D
-
Rotating half installation
Tur
n over
Polished
surface
Rubber
surface
Cardboard
washer
(supplied w/seal)
3/4" socket
or pipe
Sealing
face
Rubber drive
ring
Impeller
Shaft
shoulder
685 0294
Figure 5